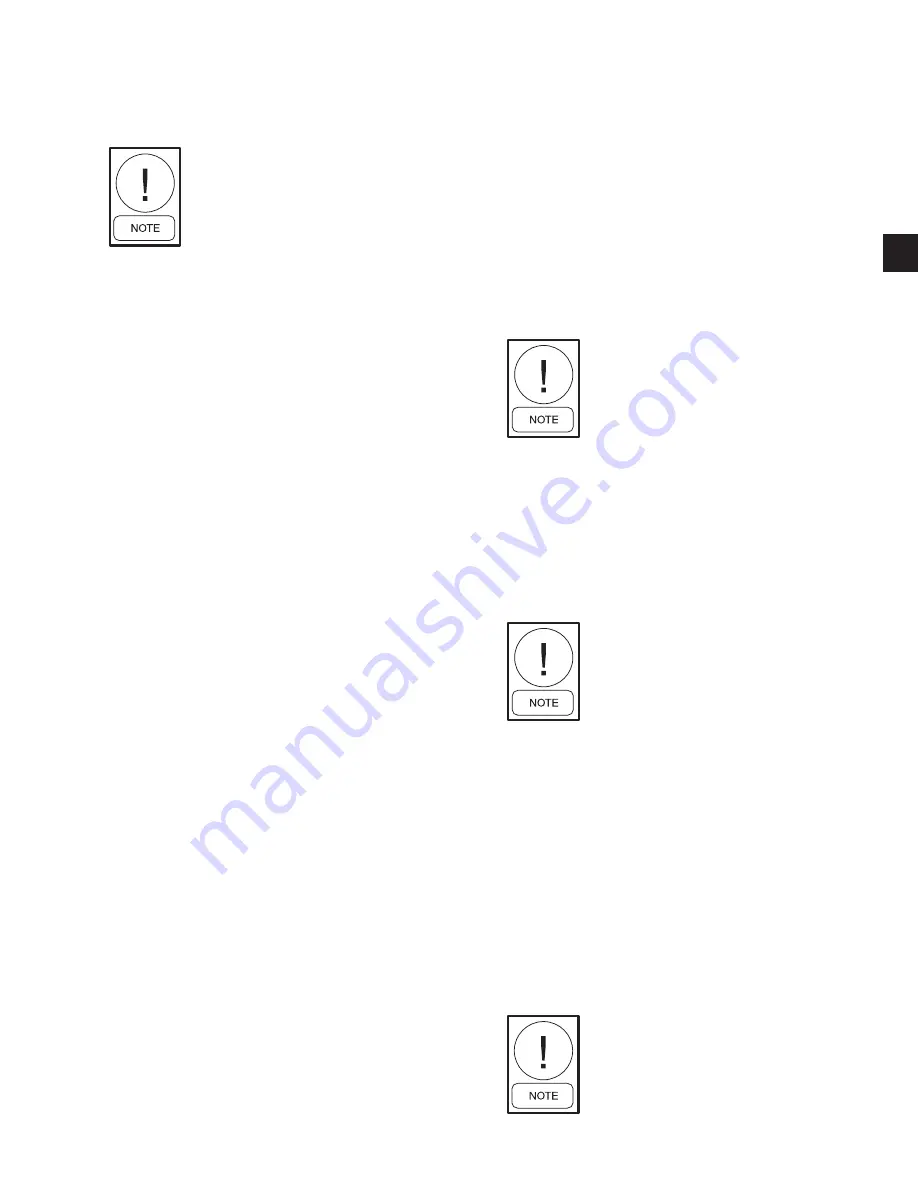
FORM 220.11-NM2 (602)
27
YORK INTERNATIONAL
3
8. Check if the suction temperature is excessively high
to cause elevated discharge temperature.
The minimum compressor discharge
temperature depends upon discharge
pressure and the gas being compressed.
9. If 10°F of discharge superheat, as a minimum, can-
not be maintained check the system for possible
liquid entrainment, unless liquid injection is used for
noise suppression.
THE AUXILIARY OIL PUMP
The Auxiliary Oil Pump (2, Figures 7 & 8) is typically
mounted on the side of the compressor. This pump is
automatically controlled, through the auxiliary oil pres-
sure differential switch mounted on the compressor, or
in the Control Center.
The primary function of the auxiliary oil pump is to au-
tomatically furnish oil to the compressor lubrication sys-
tem on start-up while the main oil pump is coming up to
speed, on shutdown while the rotor is coming to rest, or
at any time during operation if the main oil pump fails to
produce adequate pressure. In addition this pump was
used to charge oil into the reservoir of series piped sys-
tems.
On variable speed drives, the auxiliary oil pump may
also operate at very low compressor speeds when the
main oil pump can not develop adequate oil pressure.
On series arrangements this pump is equipped with two
separate suction connections as follows:
1. From main oil pump discharge (21).
2. From oil charging valve (23).
The auxiliary oil pump (2) has two discharge connec-
tions with stop valves (20 and 22) which are connected
into the main oil pump discharge ahead of the oil filter
(3) and into the oil reservoir (5) for oil charging.
1. The discharge stop valve (24) ahead of the oil filter
(3) should never be closed except while servicing
the auxiliary oil pump or charging oil.
2. During normal operation, the auxiliary oil pump suc-
tion (21) and discharge valves (20) should be open
to permit proper automatic pump operation. The
other pump connection should be closed.
3. The Hand-Automatic Switch should be set at “Au-
tomatic” during operation, except as noted in Add-
ing Oil To Compressor.
Adding Oil To Compressor for a Series Oil Flow
System
1. Maintain the operating oil level of this compressor
at approximately 1/4 inch above the bottom of the
upper sight glass (Figure 2).
2. When the oil level falls so that it is not visible in the
top sight glass, add oil as follows:
The oil capacity is 10 gallons for 26
inch compressors, 35 gallons for 38
inch compressors, and 50 gallons for
55 inch compressors using integral
lube piping systems. When adding or
changing oil, use only YORK Com-
pressor Oil of the proper designation
specified for the application.
A. Close auxiliary oil pump discharge valves (20)
and auxiliary oil pump suction valve (21).
B. Open oil reservoir return valve (22).
To prevent the entrance of air into the
system, be sure the open end of the
charging line is immersed in the con-
tainer of oil and crack open the charg-
ing valve (23). Oil or gas can then
bleed back through the charging line
to displace the air.
C. Submerge the oil charging line in a clean oil
container. Be sure to check the container for
any evidence of contamination.
D. Slowly open valve (23) and bleed oil or gas back
through the line to displace the air and not to
disrupt the normal lubrication system. Close
valve (23) when bleeding is completed.
E. Start the auxiliary oil pump (2) manually.
F. Open valve (23).
The normal pressure differential on
the auxiliary oil pump internal relief
valve is 60 psi (if so equipped).
-
Summary of Contents for Turbomaster M Series
Page 15: ...FORM 220 11 NM2 602 15 YORK INTERNATIONAL FIG 3 TYPICAL PRIMARY COMPRESSOR GAS FLOW LD07318 3 ...
Page 16: ...YORK INTERNATIONAL 16 FORM 220 11 NM2 602 FIG 4A MAJOR COMPONENTS LD07319 Operation ...
Page 31: ...FORM 220 11 NM2 602 31 YORK INTERNATIONAL Operation 3 This page intentionally left blank ...