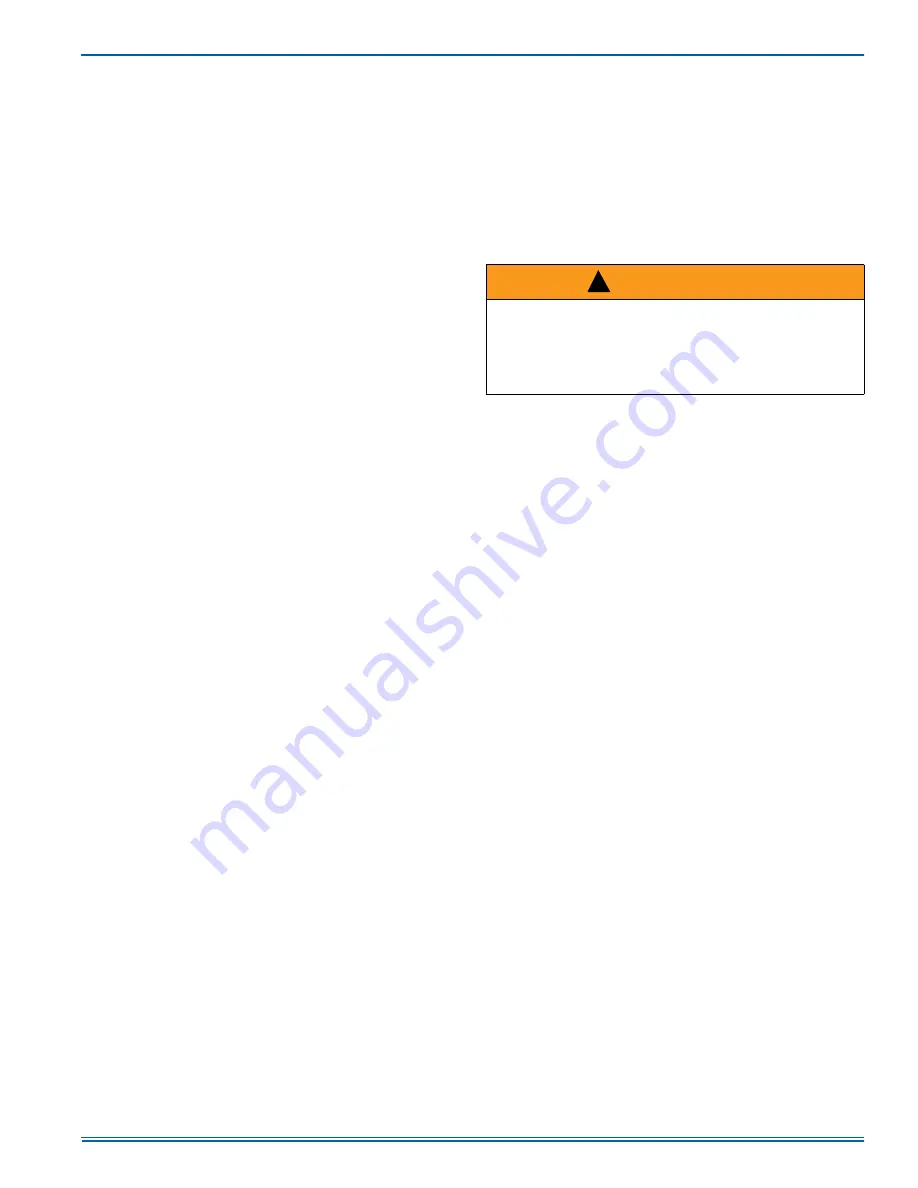
5894307-UIM-B-0920
Johnson Controls Ducted Systems
29
SECTION X: NORMAL OPERATION AND
DIAGNOSTICS
NORMAL OPERATION SEQUENCE
The following describes the sequence of operation of the furnace. Refer
to Owners Manual for component location.
Continuous Blower
Cooling/heating thermostats have a fan switch that has an ON and
AUTO position. In the ON position, the thermostat circuit is completed
between terminals R and G. The motor operates continuously on the
speed tap wire that is connected to the FAN terminal on the furnace
control board. To obtain a different circulating fan (continuous blower)
speed, change the wire connected to the FAN connection with one of
the speed tap wires located on the PARK terminals.
Intermittent Blower - Cooling
Cooling/heating thermostats have a fan switch that has an ON and
AUTO position. In the AUTO position, the thermostat circuit is com-
pleted between terminals R and G when there is a call for cooling. The
motor operates on the speed tap wire that is connected to the COOL
cooling terminal on the control board. The fan off setting is fixed at 60 s
to improve cooling efficiency.
Heating Cycle
When the thermostat switch is set on HEAT and the fan is set on AUTO,
and there is a call for heat, a circuit is completed between terminals R
and W of the thermostat. The induced draft blower starts and runs for
several seconds to bring fresh combustion air into the combustion
chamber. Then the induced draft blower shuts off and the hot surface
igniter glows for about 17 s. After this warm up, the induced draft blower
starts again and the ignition module opens the main gas valve. The
blower motor energizes 30 s after the gas valve opens, if a flame is
detected. Normal furnace operation continues until the thermostat cir-
cuit between R and W is opened, which causes the ignition system and
gas valve to de-energize and the burner flames to be extinguished. The
vent motor operates for 15 s and the blower motor operates for the
amount of time set by the fan-off delay jumper located on the control
board. See Figure 32. The heating cycle is now complete, and ready for
the start of the next heating cycle.
If the flame is not detected within 7 s of the gas valve opening, the gas
valve is shut off and a retry operation begins. Also, if the flame is lost for
2 s during the 10-s stabilization period, the gas valve is shut off and a
retry operation begins. During a retry operation, the vent motor starts a
15-s inter-purge and the ignitor warm-up time is extended to 27 s. If the
flame is established for more than 10 s after ignition during a retry, the
control clears the ignition attempt (retry) counter. If three retries occur
during a call for heat, the furnace shuts down for 1 h. If at the end of the
1-h shut down there is a call for heat, the furnace initiates a normal start
cycle. If the problem has not been corrected, the furnace locks out after
three retries.
A momentary loss of gas supply, a flame blowout, or a faulty flame
probe circuit results in a disruption in the flame and is sensed within
1.0 s. The gas valve de-energizes and the control begins a recycle
operation. A normal ignition sequence begins after a 15-s inter-purge. If
during the five recycles, the gas supply does not return, or the fault con-
dition is not corrected, the ignition control locks out for 60 min.
During burner operation, a momentary loss of power for 50 milliseconds
or longer de-energizes the gas valve. When the power is restored, the
gas valve remains de-energized and the ignition sequence immediately
restarts.
TROUBLESHOOTING
Make the following visual checks before troubleshooting:
1. Check that the power to the furnace and the ignition control module
is ON.
2. Check that the manual shut-off valves in the gas line to the furnace
are open.
3. Make sure all wiring connections are secure.
4. Review the sequence of operation. Start the system by setting the
thermostat above the room temperature. Observe the system’s
response, then use the NORMAL OPERATION SEQUENCE sec-
tion to check the system’s operation.
FURNACE CONTROL DIAGNOSTICS
The furnace has built-in, self-diagnostic capability. A blinking LED light
on the control board can flash red, green, or amber to indicate various
conditions. The control continuously monitors its own operation and the
operation of the system. If a fault occurs, the LED light indicates the
fault code.
The flash codes listed below have the following timing: the LED light
turns on for 1/4 s and turns off for 1/4 s. This pattern is repeated the
number of times equal to the code. There is a 1.5-s pause between
codes. For example, the 6 Red Flashes
code means the LED light
flashes on and off six times and then remains off for 1.5 s. This pattern
repeats as long as the fault condition remains.
Steady on Green:
Indicates normal operation with no thermostat calls.
1 Green Flash:
Indicates normal operation with a thermostat call for
heat.
2 Green Flashes:
Indicates normal operation with a thermostat call for
cooling.
3 Green Flashes:
Indicates normal operation with a thermostat call for
continuous fan.
LED Steady Off:
If the LED light does not flash at all, check for power
to the control board. If the control board is correctly powered, the con-
trol board may need to be replaced.
Steady on Red:
Indicates a control failure. Turn off the power to the fur-
nace and turn on the power to the furnace again. If the fault code
returns, the control board must be replaced. The control board is not
field-repairable.
1 Red Flash:
Indicates system lockout due to too many retries.
2 Red Flashes:
Indicates a pressure switch null error. The pressure
sensor is sensing pressure when there should not be any pressure.
Check for a faulty pressure sensor or miswiring.
3 Red Flashes:
Indicates a pressure switch span error. The pressure
sensor is not sensing the correct pressure. Check for the following:
• Faulty inducer
• Blocked vent pipe
• Broken pressure sensor hose
• Disconnected pressure sensor or inducer wires
• Faulty pressure sensor
WARNING
Never bypass any safety control to allow furnace operation. To
do so will allow furnace to operate under potentially hazardous
conditions.
Do not try to repair controls. Replace defective controls with
OEM Source 1 Parts.
Never adjust pressure switch to allow furnace operation.
!