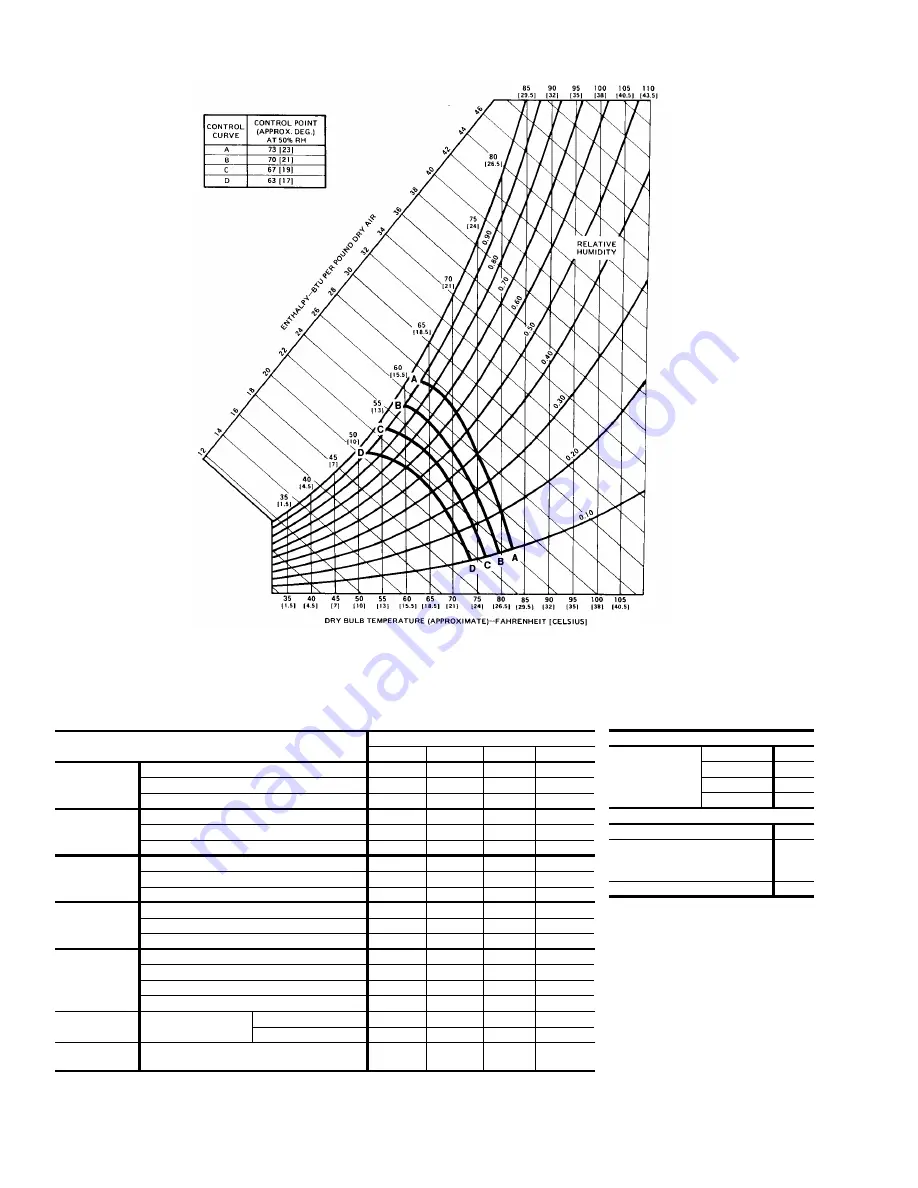
FIG. 8 - ENTHALPY SETPOINT ADJUSTMENT
WEIGHTS (LBS)
BASIC UNIT
7-1/2 Ton
1040
8-1/2 Ton
1125
10 Ton
1180
12-1/2 Ton
1470
ACCESSORIES
Economizer
77
Motorized
Outdoor Air
Damper
97
Roof Mounting Curb
155
MODEL
DCG
090
102
120
150
EVAPORATOR
BLOWER
CENTRIFUGAL BLOWER (Dia. x Wd. in.) 12 x 12
12 x 12
15 X 12
15 x 12
FAN MOTOR HP (STANDARD)
2
2
2
3
FAN MOTOR HP (ALTERNATE)
-
3
3
5
EVAPORATOR
COIL
ROWS DEEP
4
4
4
4
FINS PER INCH
15
15
15
15
FACE AREA (Sq. Ft.)
7.8
9.1
10.9
13.4
OUTDOOR
FAN
(Two Per Unit)
PROPELLER DIA. (in.)
24 ea.
24 ea.
24 ea.
24 ea.
FAN MOTOR HP
1/2 ea.
1/2 ea.
1/2 ea.
3/4 ea.
NOM. CFM TOTAL
2900 ea. 3200 ea. 3600 ea. 4400 ea.
CONDENSER
COIL
ROWS DEEP
2
2
2
2
FINS PER INCH
13
13
13
13
FACE AREA (Sq. Ft.)
16.7
20.0
24.0
29.3
AIR
FILTERS
(SEE NOTE)
QUANTITY PER UNIT (12" X 24" X 2")
2
2
-
-
QUANTITY PER UNIT (16" X 24" X 2")
2
2
2
3
QUANTITY PER UNIT (18" X 24" X 2")
-
-
2
2
TOTAL FACE AREA (sq. ft.)
9.3
9.3
11.3
14.0
CHARGE
REFRIGERANT 22
(lbs./oz.)
SYSTEM NO. 1
6/8
7/4
8/0*
10/4
SYSTEM NO. 2
6/8
7/11
8/12*
10/8
COMPRESSOR
QTY.
HERMETIC
2
2
2
2
NOTE: Filter racks are adapted for 1" or 2" thick filters.
* D4CG120 charge is 8 lbs. 0 ozs. in system 1 & 2.
TABLE 4 - PHYSICAL DATA
530.18-N10Y
8
Unitary Products Group