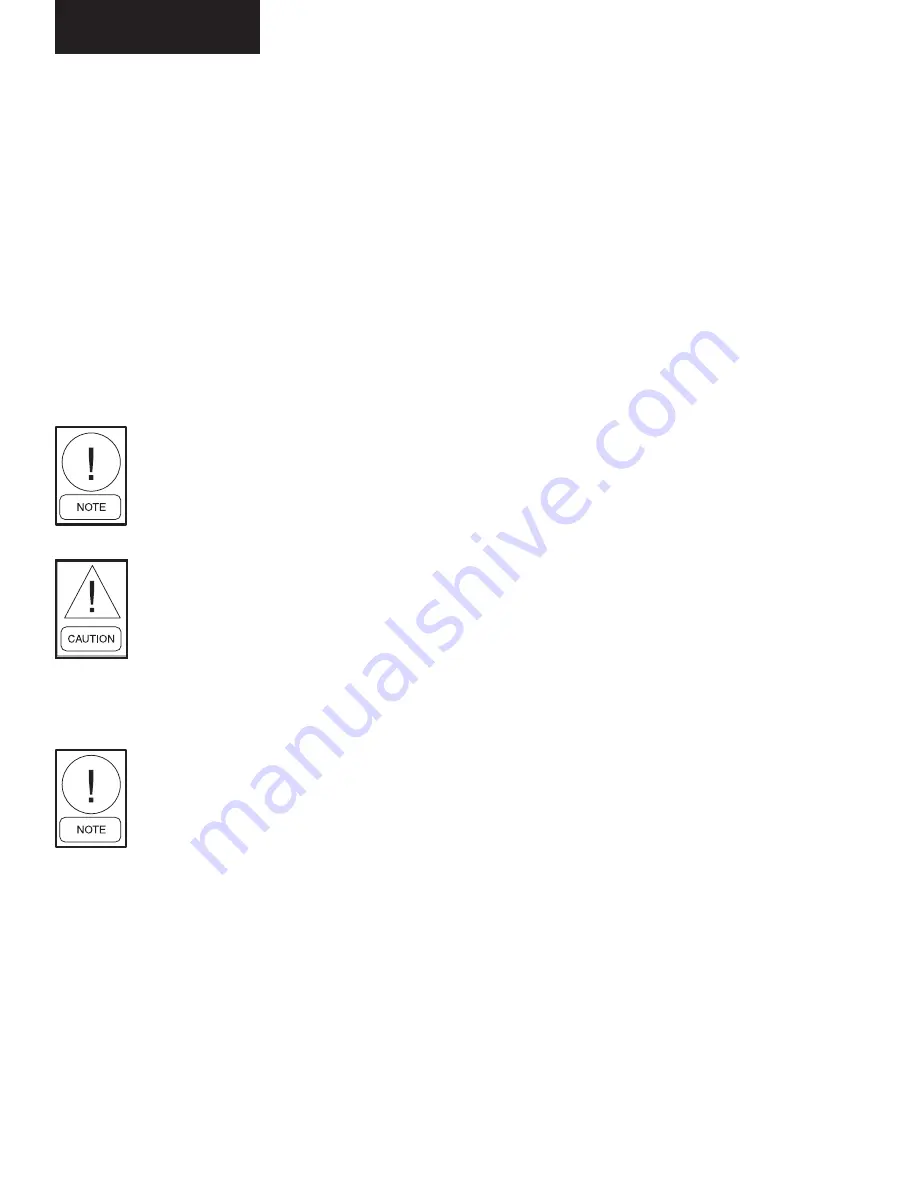
14
YORK INTERNATIONAL
FORM 201.18-NM1 (102)
Current Overload
The 2ACE module design uses one integral current trans-
former per phase to provide protection against rapid
current overload conditions. The module responds to
changes in current and must be calibrated using DIP
switches located on the module. Integral trip curves al-
low for in-rush currents during Wye-Delta, part wind,
or ACL starts without nuisance tripping.
To check the factory setting of the 2ACE module cur-
rent overload trip value, see Table 1 (pages 15 - 18).
For the location of the dip switches and determining the
ON side of the switches, refer to Figure 47, page 108.
As indicated, to place a switch in the ON position re-
quires pushing the switch to the left.
A switch must be pushed to the left to
place the switch in the ON position.
It is recommended that a YORK Ser-
vice Technician or the YORK factory
be consulted before changing these
settings for any reason, since damage
to the compressor could result.
Changes should never be made unless
it is verified that the settings are in-
correct.
Anytime a dip switch change is made,
power must be cycled off and on to the
module to reprogram the module to the
new valve.
Thermal Overload
Three PTC (positive temperature coefficient) ther-
mistors in the motor windings of each phase provides
thermal protection. The sensor resistance stays rela-
tively constant at 1k
Ω
until a temperature of 266°F
(130°C) is sensed. The sensor experiences a rapid rise
in resistance beyond this temperature. Whenever the
resistance of one of the sensors reaches 13k
Ω
, the 2ACE
module trips, which ultimately de-energizes the motor’s
pilot circuit. Reset is manual after the motor cools and
the sensor resistance drops to 3.25k
Ω
.
Current Imbalance (Loaded & Unloaded)/
Loss of Phase
A 2-second delay at start-up allows for any imbalances
resulting during normal starting conditions. After this
initial delay, the 2ACE module compares the “Operat-
ing Current” to the measured half-line current. The “Op-
erating Current” is given by 0.65 X factory overload
current setting.
An unloaded compressor condition occurs when any
measured half-line current is less than the “Operating
Current.” A current imbalance exceeding an unloaded
level of 25% will result in the motor pilot circuit being
de-energized.
A loaded compressor condition occurs when any mea-
sured half-line current is greater than or equal to the
“Operating Current.” A current imbalance exceeding a
loaded level of 17% will result in the motor pilot cir-
cuit being de-energized.
Imbalance is defined as
(High Phase - Low Phase)/High Phase
Improper Phase Sequence
The 2ACE module calculates the phase sequence at
start-up using the three current transformers to deter-
mine whether the three-phase sequence on the load side
of the main contactor is miswired. Upon detection of a
miswired motor load, the module will de-energize the
main contactor pilot circuit within 50 millisecond re-
sponse time.
Product Description
Summary of Contents for MILLENNIUM YCAS0230
Page 45: ...45 YORK INTERNATIONAL FORM 201 18 NM1 102 This page intentionally left blank 7 ...
Page 70: ...70 YORK INTERNATIONAL FORM 201 18 NM1 102 Technical Data FIG 30 DETAIL B LD03285 ...
Page 166: ...166 YORK INTERNATIONAL FORM 201 18 NM1 102 ...