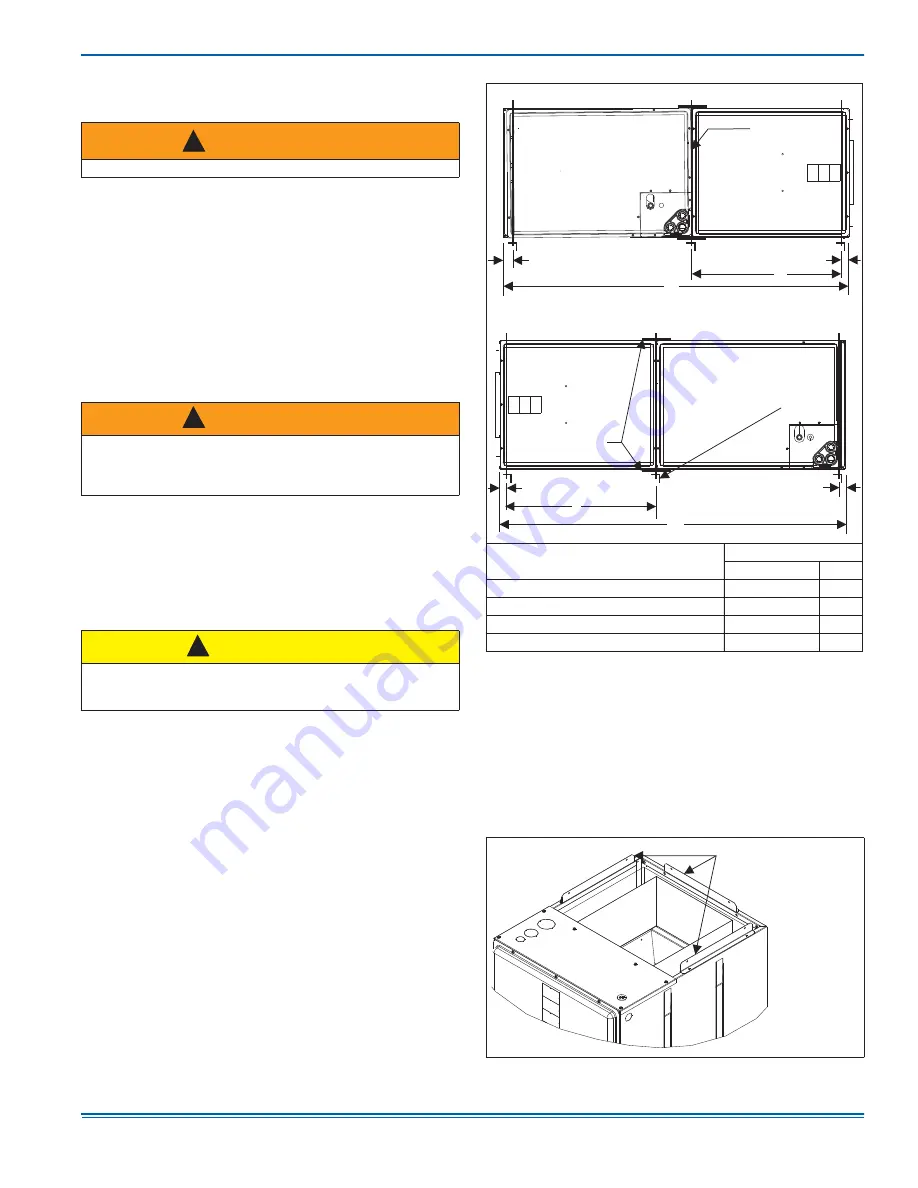
5169034-UIM-B-0216
Johnson Controls Unitary Products
5
SECTION IV: DUCT WORK AND
CONNECTIONS
Air supply and return may be handled in one of several ways best
suited to the installation. Upflow, horizontal or downflow applications
may be used.
The vast majority of problems encountered with heating and cooling
systems can be linked to improperly designed or installed duct systems.
It is therefore highly important to the success of an installation that the
duct system be properly designed and installed.
When installing a central air return grille in or near the living space, it is
advisable to design the duct work so that the grille is not in direct line
with the opening in the unit. One or two elbows and acoustical duct liner
assures a quieter system. Operation where return air duct is short or
where sound may be a problem, acoustical duct liner should be used
inside the duct. Use flexible duct connectors to minimize the
transmission of vibration/noise into the conditioned space.
Insulation of duct work is a must where it runs through an unheated
space during the heating season or through an uncooled space during
the cooling season. The use of a vapor barrier is recommended to
prevent absorption of moisture from the surrounding air into the
insulation.
The supply air duct should be properly sized by use of a transition to
match unit opening. All ducts should be suspended using flexible
hangers and never fastened directly to the structure.
Duct work should be fabricated and installed in accordance with local
and/or national codes. This includes the standards of the National Fire
Protection Association for Installation of Air-Conditioning and
Ventilating Systems, NFPA No. 90B. If electric heat is used, non-
flammable material must be used. Duct systems should be designed in
accordance with the Air Conditioning Contractors of America (ACCA) –
Manual D.
HORIZONTAL SUSPENSION
For suspension of these units in horizontal applications, it is recom-
mended to use angle steel support brackets with threaded rods, sup-
porting the units from the bottom, at the locations shown in Figure 6.
DUCT FLANGES
Three duct flanges are provided to assist in positioning and attaching
duct work to the air handler. These flanges are included in the unit parts
bag. With the screws from the parts bag, install one of the duct flanges.
Duct flanges have holes on both legs with one leg longer than the other.
The longer leg can be used to mate against the air handler so that
different thicknesses of duct board can be made flush with the outer
surface of the air handler. Repeat the procedure for the other two
flanges. Refer to Figure 7. If the flanges are not used, they may be
discarded.
WARNING
Use only 1/2” screws to connect duct work to bottom of unit.
WARNING
Do not bring in return air from a location which could introduce haz-
ardous substances into the airflow.
Use 1/2” screws to connect duct work to cabinet. If pilot holes are
drilled, drill only through field duct and unit flange.
CAUTION
This unit is not designed for non-ducted (freeblow) applications. Do
not operate without duct work attached to unit.
Equipment should never be operated without filters.
!
!
!
(Cabinet Width) Position
Dimensions
H
X
(17-1/2”) Horizontal Left
40-1/2” – 47-1/2”
20”
(21” thru 24-1/2”) Horizontal Left
43-1/2” – 55-1/2”
21”
(17-1/2”) Horizontal Right
40-1/2” – 47-1/2”
20”
(21” thru 24-1/2”) Horizontal Right
43-1/2” – 55-1/2”
21”
FIGURE 6:
Typical Horizontal Installation
FIGURE 7:
Duct Attachment
S
U
S
PEN
S
I
O
N
S
UPP
O
RT L
OC
ATI
O
N
S
F
O
R H
O
RIZ
O
NTAL RIGHT
2”
1
-
1
/2”
M
IN.
1
-
1
/2” x
1
-
1
/2”
A
ng
l
e
R
e
co
mmended
l
engt
h 26”
minimum
w
it
h 2” cl
earan
c
e
o
n
bo
t
h
sides
o
f
A
ir
H
and
l
er
M
IN. 3/8”
THREADED R
O
D
H
1
”
1
-
1
/2”
A
0
348
00
2
X
H
S
U
S
PEN
S
I
O
N
S
UPP
O
RT L
OC
ATI
O
N
S
F
O
R H
O
RIZ
O
NTAL LEFT
X
TIE PLATE
A
0
34
1
-
001
DU
C
T FLANGE
S
(
S
h
i
pp
ed
in
b
ag
w
it
h co
i
l)