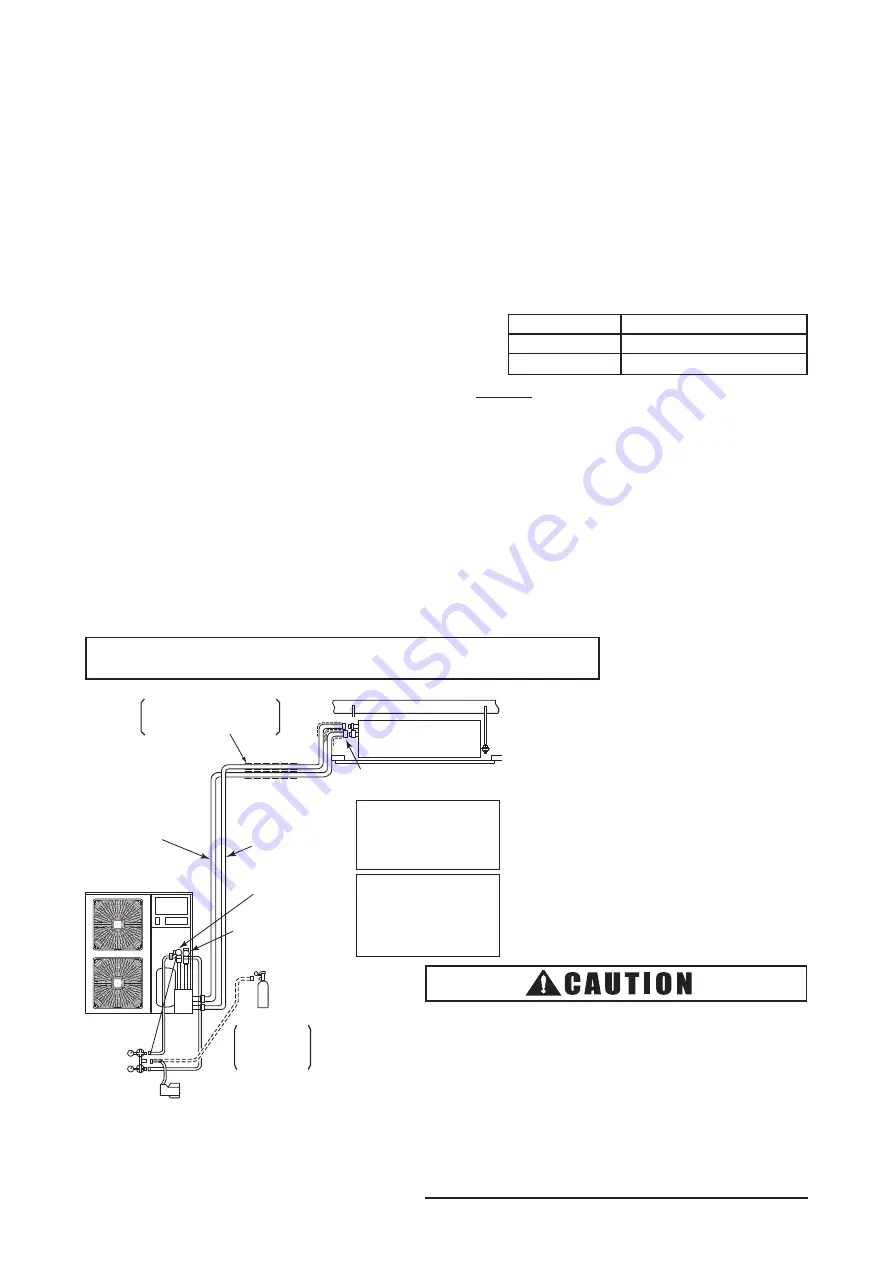
16
(5) Connect the gauge mani-fold using
charging hoses with a nitrogen cylinder to
the check joints of the liquid line and the
gas line stop valves.
Perform the air-tight test.
Do not open the stop valves. Apply
nitrogen gas pressure of 4.15MPa.
(6) Check for any gas leakage at the flare nut
connections, or brazed parts by gas leak
detector or foaming agent.
(7) After the air tight test, release nitorogen
gas.
5.5
Vacuum Pumping
(1) Connect a mani-fold gauge to the check
joints at the both sides.
Continue vacuum pumping work until the
pressure reaches -756mmHg or lower for
one to two hours.
(2) After vacuum pumping work, stop the
mani-fold valve’s valve, stop the vacuum
pump and leave it for one hour. Check to
ensure that the pressure in the mani-fold
gauge does not increase.
(3) Fully open the gas valve and liquid valve.
Foaming Agent
Manufacturer
SNOOP
NUPRO (U.S.A.)
Gupoflex
YOKOGAWA & CO., LTD
NOTES:
1. When the spindle cap for stop valve is
removed, the gas accumulated at O-ring or
screws is released and may make sound. This
phenomenon is NOT a gas leakage.
2. This unit is only for the refrigerant R410A. The
manifold gauge and the charging hose should
be exclusive use for R410A.
3. If vacuum degree of -0.1MPa (-756mmHg) is
not available, it is considered of gas leakage or
entering moisture. Check for any gas leakage
once again. If no leakage exists, operate the
vacuum pump for more than one to two hours.
Liquid Line
Gas Line
Liquid Line Stop Valve
Gas Line Stop Valve
Nitrogen Tank
for Air Tight Test
and
Nitrogen Blow
during Brazing
Vacuum Pump
Manifold
Gauge
Wind tape from outside of
thermal insulation of gas piping
and liquid piping.
Indoor Unit
Thermal Insulation Finishing Work
Cover the flare nut and union of the
piping connection with thermal insulation.
Cover the liquid line
with thermal insulation.
Insulate the liquid pipe for
prevention of the capacity
decrease according to the
ambient air conditions and
the dewing on the pipe surface
by the low pressure.
Check to ensure that there is
no gas leakage. When large
amount of the refrigerant leaks,
the troubles as follows may occur;
1. Oxygen Deficiency
2. Generation of Harmful Gas
Due to Chemical Reaction
with
Fire.
(4) This system is not necessary to charge
refrigeration less than 30m of the actual
piping length. If the total piping length is
more than 30m, it is necessary additional
refrigerant charge.
(5) Check for any gas leakage by gas leak
detector or forming agent. Use the
foaming agent which does not generate the
ammonia (NH
3
) by chemical reaction. The
recommended forming agent are as shown
below. Do not use general household
detergent for checking.
At the test run, fully open the spindle.
If not fully opened, the devices will be damaged.
An excess or a shortage of refrigerant is the main
cause of trouble to the units.
Charge the correct refrigerant quantity according
to the description of label at the inside of service
cover.
Check for refrigerant leakage in detail. If a large
refrigerant leakage occurs, it will cause difficulty
with breathing or harmful gases would occur if a
fire was being used in the room.
Never use the refrigerant charged in the outdoor unit for air purging.
Insufficient refrigerant will lead to failure.
Summary of Contents for JDOH Series
Page 2: ......
Page 19: ...JE 102SN JE 162SN ...