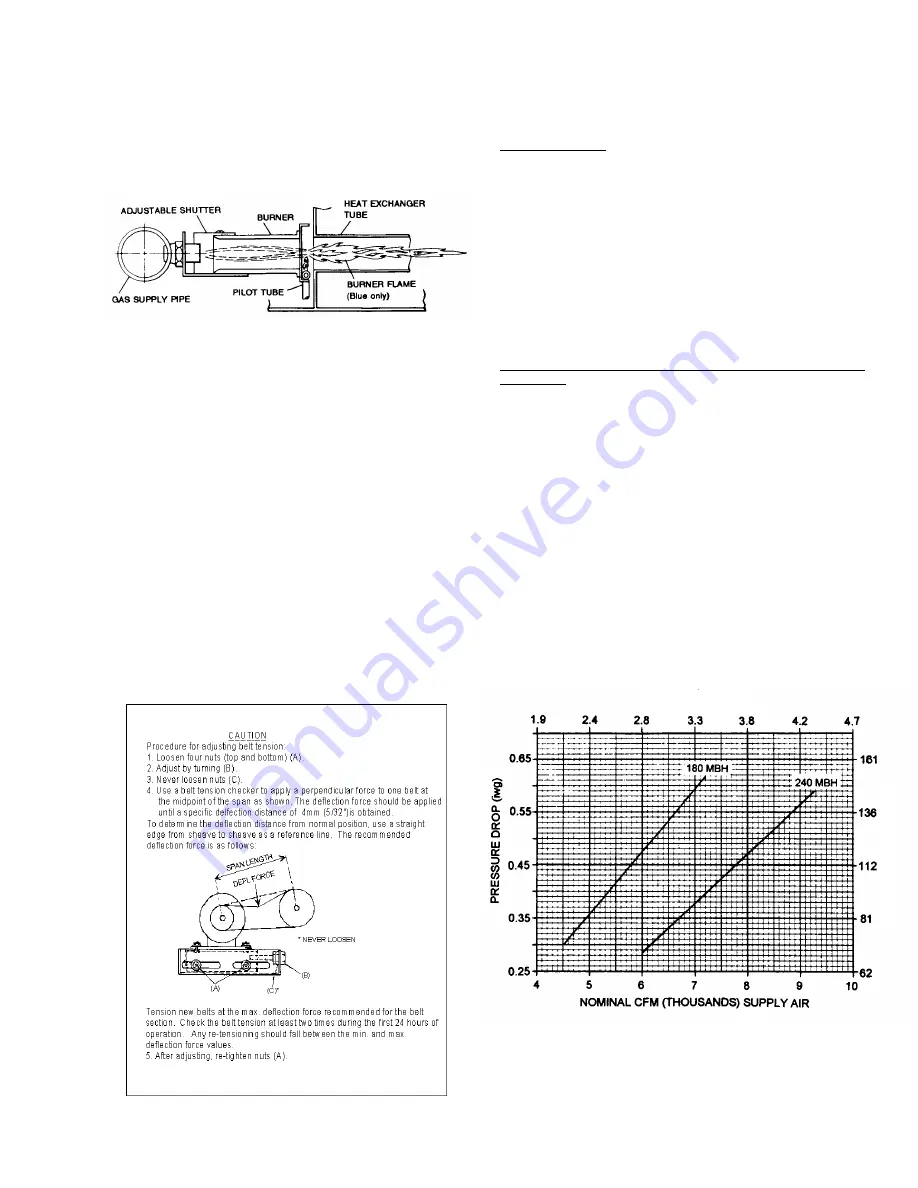
3. Remove the gas piping closure panel.
4. Disconnect wiring to the gas valves and spark ignitors.
Remove the manifold-burner gas valve assembly by lifting
up and pulling back.
Burners are now accessible for service.
Reverse the above procedure to replace the assemblies. Make
sure that burners are level and seat at the rear of the heat
exchanger.
BURNER AIR SHUTTER ADJUSTMENT
Adjust burner shutters so no yellow flame is observed in the
heat exchanger tubes.
CHECKING SUPPLY AIR CFM
The RPM of the supply air blower will depend on the required CFM,
the unit accessories or options and the static resistances of both
the supply and the return air duct systems. With this information,
the RPM for the supply air blower and the motor pulley adjustment
(turns open) can be determined from the Blower Performance
Data Tables.
High speed drive accessories (containing a smaller blower
pulley and a shorter belt) are available for applications requiring
the supply air blower to produce higher CFM’s and/or higher
static pressures. Use Model 1LD0416 for 15 ton units and
Model 1LD0417 for 20 ton units. Refer to the Blower Motor and
Drive Data Table.
Note the following:
1. The supply air CFM must be within the limitations shown in
the Applications Data Table.
2. Pulleys can be adjusted in half turn increments.
3. The tension on the belt should be adjusted as shown in the
Belt Adjustment figure.
Start the supply air blower motor. Adjust the resistances in both
the supply and the return air duct systems to balance the air
distribution throughout the conditioned space. The job
specifications may require that this balancing be done by
someone other than the equipment installer.
To check the supply air CFM after the initial balancing has been
completed:
1. Remove the two 5/16 inch dot plugs from the blower motor and the
filter access panels shown in the Dimensions and Clearances figure.
2. Insert at least 8 inches of 1/4 inch tubing into each of these
holes for sufficient penetration into the air flow on both sides
of the indoor coil.
NOTE: The tubes must be inserted and held in a position
perpendicular to the air flow so that velocity pres-
sure will not affect the static pressure readings.
3. Using an inclined manometer, determine the pressure drop
across a dry evaporator coil. Since the moisture on an
evaporator coil may vary greatly, measuring the pressure
drop across a wet coil under field conditions would be
FIG. 16 - TYPICAL FLAME APPEARANCE
FIG.17 - BELT ADJUSTMENT
FIG. 18 - PRESSURE DROP ACROSS A DRY INDOOR
COIL VS SUPPLY AIR CFM
530.18-N6Y
Unitary Products Group
19