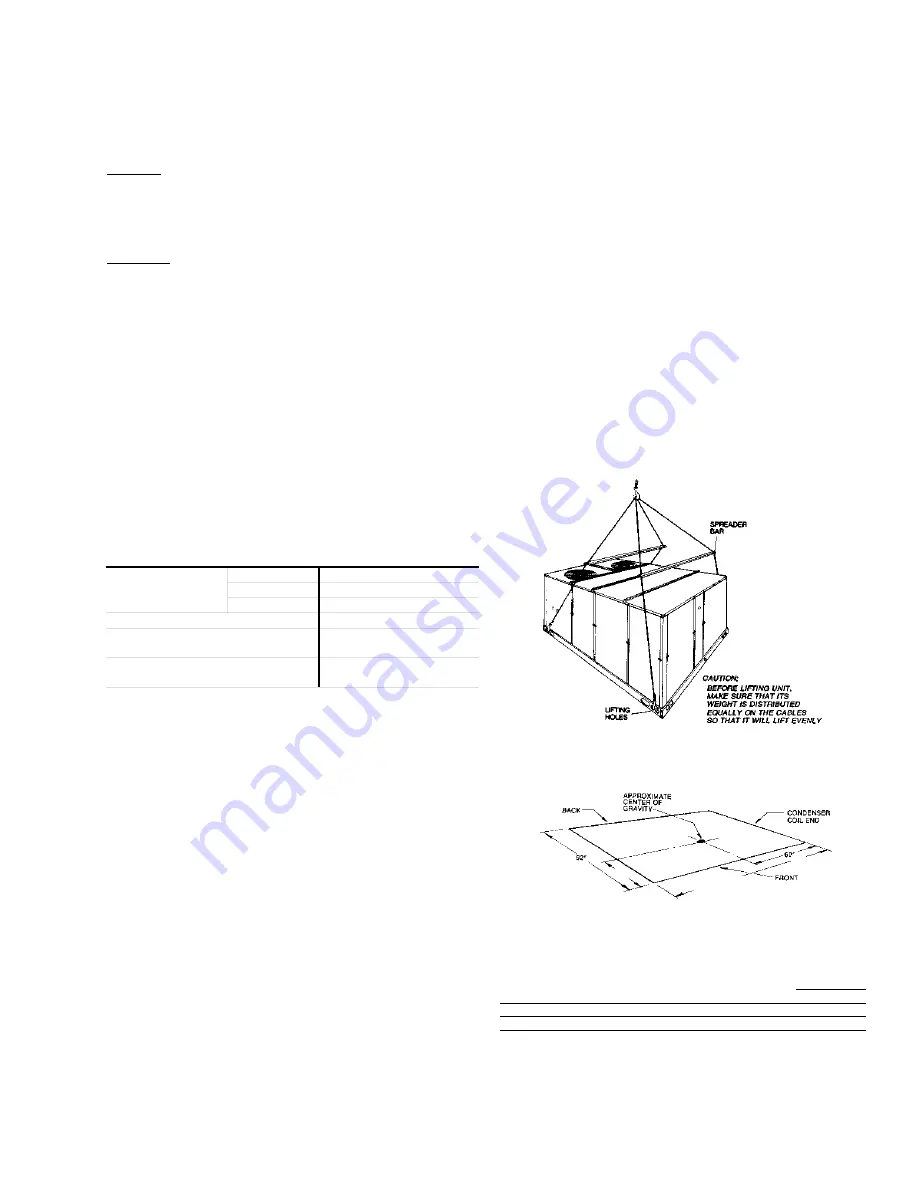
LIMITATIONS
These units must be installed in accordance with the following
applicable national and local safety codes:
In U.S.A.:
1. National Electrical Code ANSI/NFPA No. 70.
2. National Fuel Gas Code Z223.1.
3. Gas-Fired Central Furnace Standard ANSI Z21.47a.
4. Local gas and electric utility requirements.
In Canada:
1. Current Canadian Electrical Code C22.1.
2. Current Gas Installation Codes CAN/CGA-B149.1 and .2
3. Local plumbing and waste water codes.
4. Other applicable local codes.
Refer to Table 1 for Unit Application Data and to Table 2 for Gas
Heat Application Data.
After installation, units with gas heat must be adjusted to obtain
a temperature rise within the range specified on the unit rating
plate.
If components are to be added to a unit to meet local codes,
they are to be installed at the dealer’s and/or the customer’s
expense.
Size of unit for proposed installation should be based on heat
loss/heat gain calculation made according to the methods of
the Air Conditioning Contractors of America (ACCA).
This furnace is not to be used for temporary heating of buildings
or structures under construction.
LOCATION
Use the following guidelines to select a suitable location for
these units.
1. Unit is designed for outdoor installation only.
2. Condenser coils must have an unlimited supply of air.
Where a choice of location is possible, position the unit on
either north or east side of building.
3. For ground level installation, use a level concrete slab with
a minimum thickness of 4 inches. The length and width
should be at least 6 inches greater than the unit base rails.
Do not tie slab to the building foundation.
WARNING: E x c e s s i v e e x p o s ur e o f t h i s f u r na c e t o
contaminated combustion air may result in
equipment damage or personal injury. Typical
contaminates include: permanent wave solutions,
chlorinated waxes and cleaners, chlorine based
sw immin g pool chemica ls, water softening
chemicals, carbon tetrachloride, Halogen type
r e f r i g e ra n t s, c l e an i n g s ol v e nt s ( e .g .
perchloroethylene), printing inks, paint removers,
varnishes, hydrochloric acid, cements and glues,
antistatic fabric softeners for clothes dryers,
masonry acid washing materials.
4. Roof structures must be able to support the weight of the
unit and its options and/or accessories. Unit must be
installed on a solid level roof curb or appropriate angle iron
frame.
CAUTION: If a unit is to be installed on a roof curb or
special frame other than a YORK roof curb,
gasketing must be applied to all surfaces that
come in contact with the unit underside.
5. Maintain level tolerance to 1/2" maximum across the entire
length or width of the unit.
RIGGING AND HANDLING
Exercise care when moving the unit. Do not remove any
packaging until the unit is near the place of installation. Rig the
unit by attaching chain or cable slings to the round lifting holes
provided in the base rails. Spreaders, whose length exceeds
the largest dimension across the unit, MUST be used across
the top of the unit. Refer to Figure 1.
Units may also be moved or lifted with a forklift, from the front
or rear only, providing that an accessory skid is used.
LENGTH OF FORKS MUST BE A MINIMUM OF 90".
CAUTION: On gas heating units, an adhesive backed label is
provided over the outside of the combustion air
inlet opening to prevent moisture from entering the
unit which could cause damage to electrical
components. Allow this closure label to remain in
place until the combustion air hood is to be installed
(refer to Figure 8).
Refer to Table 4 for unit weights and to Figure 2 for approximate
center of gravity.
CLEARANCES
All units require certain clearances for proper operation and
ser vice. Installer must make provisions for adequate
combustion and ventilation air in accordance with Section 5.3,
Air for Combustion and Ventilation of the National Fuel Gas
Code, ANSI Z223.1 (in U.S.A.) or Sections 7.2, 7.3 or 7.4 of
Gas Installation Codes CAN/CGA-B149.1 and .2 (in Canada)
and/or applicable provisions of the local building codes. Refer
to Figure 10 for the clearances required for combustible
construction, servicing, and proper unit operation.
WARNING: Do not permit overhanging structures or shrubs to
obstruct outdoor air discharge outlet, combustion
air inlet or vent outlets.
INSTALLATION
Voltage Variation,
Min. / Max.
1
208/230-3-60
187 / 253
460-3-60
414 / 506
575-3-60
518 / 630
Supply Air CFM, Min. / Max.
8,000 / 12,000
Wet Bulb Temperature (
°
F) of Air on
Evaporator Coil, Min. / Max.
57 / 72
Dry Bulb Temperature (
°
F) of Air on
Condenser Coil, Min.
2
/ Max.
25 / 120
1
Utilization range “A” in accordance with ARI Standard 110.
2
A low ambient accessory is available for applications down to 0
°
F.
TABLE 1 - UNIT APPLICATION DATA
FIG. 1 - TYPICAL RIGGING
136-1/4"
4
5
FIG. 2 - CENTER OF GRAVITY
530.18-N11Y
Unitary Products Group
3