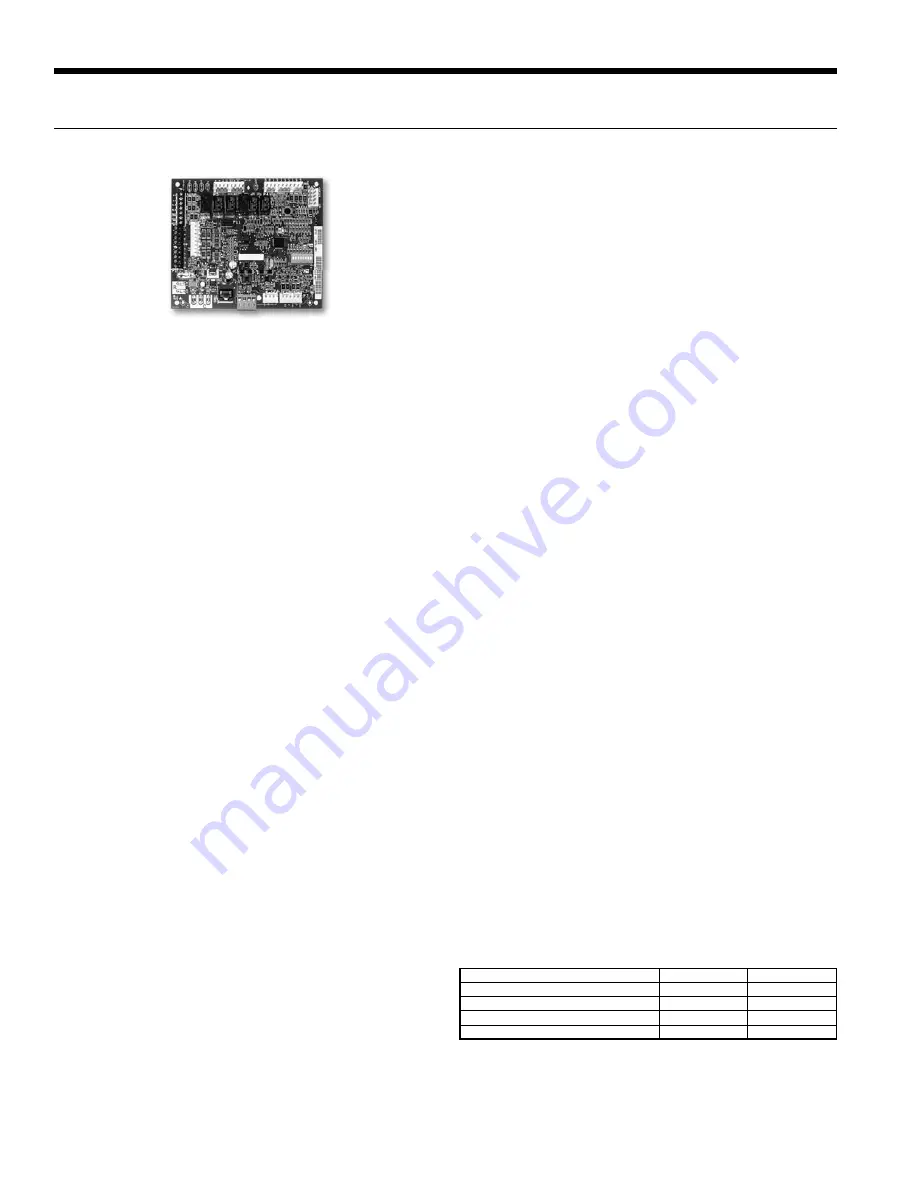
30
Aurora ‘Base’ Control
NOTE:
Refer to the Aurora Base Control Application and
Troubleshooting Guide and the Instruction Guide: Aurora Interface and
Diagnostics (AID) Tool for additional information.
Control Features
Software ABC Standard Version 2.0
Single or Dual Capacity Compressors
Either single or dual capacity compressors can be operated.
ECM Blower Motor Option
An ECM blower motor can be driven directly using the onboard
PWM output. Four blower speeds are available based upon the
G, Y1, Y2, and W input signals to the board. The blower speeds
can be changed either by the ECM manual configurations mode
method or by using the Aurora AID Tool directly. All four blower
speeds can be set to the same speed if desired.
5-Speed ECM Blower Motor Option
A 5-Speed ECM blower motor will be driven directly using the
thermostat connections. Any of the G, Y1, or Y2/W signals can
drive any of the 5 available pre-programmed blower speeds on
the motor.
Other Control Features
• Random start at power up
• Anti-short cycle protection
• High and low pressure cutouts
• Loss of charge
• Water coil freeze detection
• Air coil freeze detection
• Over/under voltage protection
• Condensate overflow sensor
• Load shed
• Dehumidification (where applicable)
• Emergency shutdown
• Hot gas reheat operation (where applicable)
• Diagnostic LED
• Test mode push button switch
• Two auxiliary electric heat outputs
• Alarm output
• Accessory output with N.O. and N.C.
• Modbus communication (master)
• Modbus communication (slave)
Field Selectable Options via Hardware
DIP Switch (SW1)
– Test/Configuration Button (See SW1
Operation Table)
Test Mode
The control is placed in the test mode by holding the push button
switch SW1 for 2 - 5 seconds. In test mode most of the control
timings will be shortened by a factor of sixteen (16). LED3 (green)
will flash at 1 second on and 1 second off. Additionally, when
entering test mode LED1 (red) will flash the last lockout one
time. Test mode will automatically time out after 30 minutes. Test
mode can be exited by pressing and holding the SW1 button for
2 to 5 seconds or by cycling the power.
NOTE:
Test mode will
automatically be exited after 30 minutes.
ECM Configuration Mode
The control is placed in the ECM configuration mode by holding
the pushbutton switch SW1 for 5 to 10 seconds, the high, low,
and “G” ECM speeds can be selected by following the LED
display lights. LED2 (yellow) will fast flash when entering the
ECM configuration. When setting “G” speed LED3 (green) will
be continuously lit, for low speed LED1 (red) will be continuously
lit, and for high speed both LED3 (green) and LED1 (red) will be
continuously lit. During the ECM configuration mode LED2 (yellow)
will flash each of the 12 possible blower speeds 3 times. When
the desired speed is flashed press SW1, LED2 will fast flash until
SW1 is released. “G” speed has now been selected. Next select
low speed, and high speed blower selections following the same
process above. After third selection has been made, the control
will exit the ECM configuration mode. Aux fan speed will remain at
default or current setting and requires the AID Tool for adjustment.
Reset Configuration Mode
The control is placed in reset configuration mode by holding the
push button switch SW1 for 50 to 60 seconds. This will reset
all configuration settings and the EEPROM back to the factory
default settings. LED3 (green) will turn off when entering reset
configuration mode. Once LED3 (green) turns off, release SW1
and the control will reset.
DIP Switch (SW2)
SW2-1
FP1 Selection – Low water coil temperature limit setting
for freeze detection. On = 30°F; Off = 15°F.
SW2-2
FP2 Selection – On = 30°F; Off = N/A
SW2-3
RV – O/B - thermostat type. Heat pump thermostats
with “O” output in cooling or “B” output in Heating can be
selected. On = O; Off = B.
SW2-4
Access Relay Operation (P2)
and 2-5
Access Relay Operation
SW2-4
SW2-5
Cycle with Blower
ON
ON
Cycle with Compressor
OFF
OFF
Water Valve Slow Opening
ON
OFF
Cycle with Comm. T-stat Hum Cmd
OFF
ON
Controls - Aurora Base Control
LX ULTRA SERIES INSTALLATION MANUAL