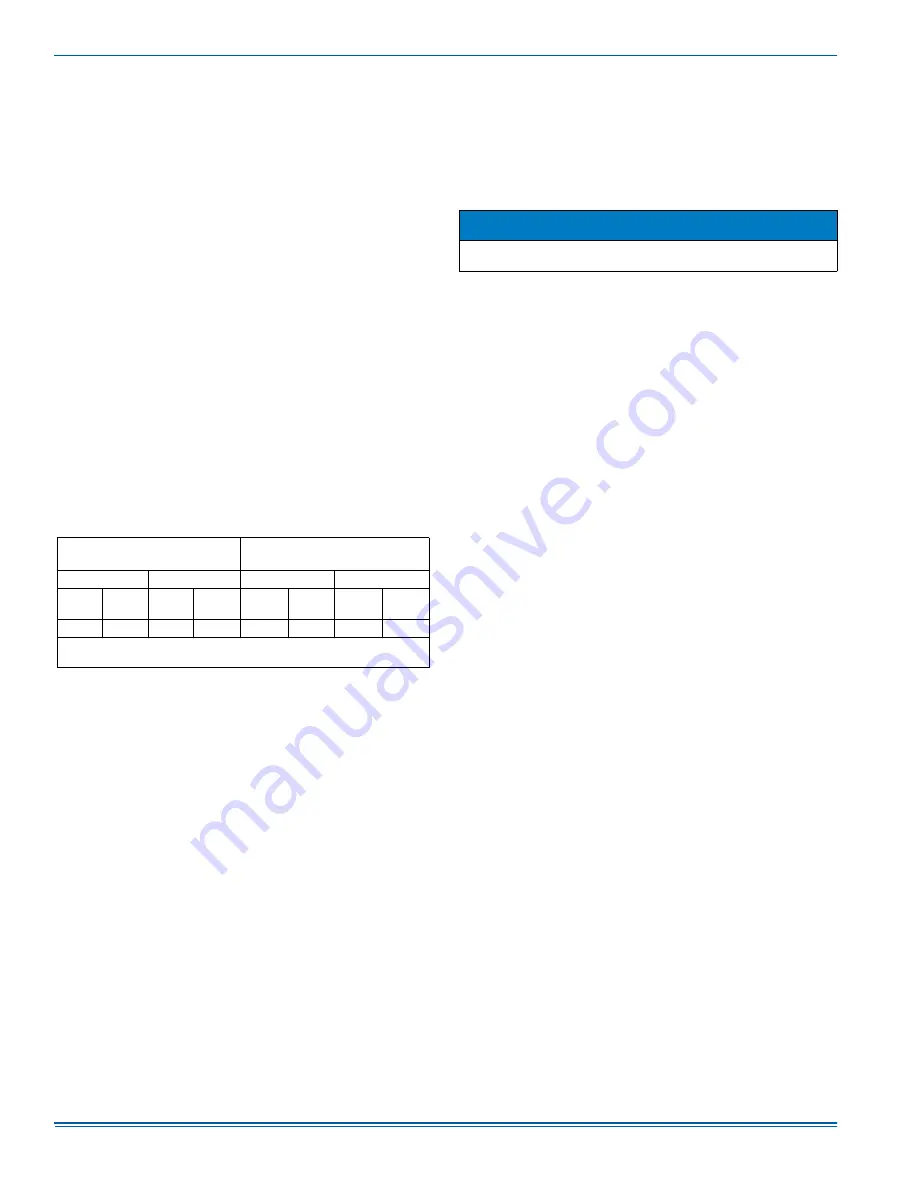
5121495-UIM-D-0516
2
Johnson Controls Unitary Products
INSPECTION
As soon as a unit is received, it should be inspected for possible dam-
age during transit. If damage is evident, the extent of the damage
should be noted on the carrier’s delivery receipt. A separate request for
inspection by the carrier’s agent should be made in writing. See Local
Distributor for more information.
Requirements For Installing/Servicing R-410A Equipment
•
Gauge sets, hoses, refrigerant containers, and recovery system
must be designed to handle the POE type oils, and the higher
pressures of R-410A.
•
Manifold sets should be high side and low side with low side
retard.
•
All hoses must have a 700 psig service pressure rating.
•
Leak detectors should be designed to detect HFC refrigerant.
•
Recovery equipment (including refrigerant recovery containers)
must be specifically designed to handle R-410A.
•
Do not use an R-22 TXV.
LIMITATIONS
The unit should be installed in accordance with all National, State and
Local Safety Codes and the limitations listed below:
1.
Limitations for the indoor unit, coil, and appropriate accessories
must also be observed.
2.
The outdoor unit must not be installed with any duct work in the air
stream. The outdoor fan is the propeller type and is not designed
to operate against any additional external static pressure.
3.
The maximum and minimum conditions for operation must be
observed to ensure a system that will give maximum performance
and service life.
4.
The unit should not be operated in cooling mode at outdoor tem-
peratures below 50°F without an approved low ambient operation
accessory kit installed.
5.
The maximum allowable line length for this product is 80 feet. To
install more than the maximum allowable line length, consult the
Piping Application Guide (P/N 247077).
SECTION III: UNIT INSTALLATION
LOCATION
Before starting the installation, select and check the suitability of the
location for both the indoor and outdoor unit. Observe all limitations and
clearance requirements.
The outdoor unit must have sufficient clearance for air entrance to the
condenser coil, air discharge, and service access. See Figure 1.
If the unit is to be installed on a hot sun exposed roof or a paved ground
area that is seasonally hot, the unit should be raised sufficiently above
the roof or ground to avoid taking the accumulated layer of hot air into
the outdoor unit.
If the system is being installed during seasonally cold weather of 55°F
or below, the preferred method is to weigh in the charge. For charging
or checking the system charge at 55°F or below, refer to the “Optional
Cold Weather Charging” procedures near the end of SECTION VI:
SYSTEM CHARGE. There is an “Optional Cold Weather Charging”
accessory kit to prevent the outdoor unit from taking in cold air below
55°F. The kit part number can be found in the list of accessory kits on
the UPGNET web site.
Provide adequate structural support for the unit.
ADD-ON REPLACEMENT/RETROFIT
When this unit is being used as a replacement for an R-410A unit, it is
required that the outdoor unit, indoor coil, and metering device all be
replaced. The following steps should be performed in order to insure
proper system operation and performance. Line-set change out is also
recommended.
1.
Change-out of the indoor coil to an approved R-410A coil/ con-
densing unit combination with the appropriate metering device.
2.
Change-out of the line-set when replacing an R-22 unit with an
R410-A unit is highly recommended to reduce cross-contamina-
tion of oils and refrigerants.
3.
If change-out of the line set is not practical, then the following pre-
cautions should be taken.
•
Inspect the line set for kinks, sharp bends, or other restrictions,
and for corrosion.
•
Determine if there are any low spots which might be serving as oil
traps.
•
Flush the line set with a commercially available flush kit to
remove as much of the existing oil and contaminants as possible.
•
Install a suction line filter-drier to trap any remaining contami-
nants, and remove after 50 hours of operation.
4.
If the outdoor unit is being replaced due to a compressor burnout,
then installation of a 100% activated alumina suction-line filter
drier in the suction-line is required, in addition to the factory
installed bi-flow liquid-line drier. Operate the system for 10 hours.
Monitor the suction drier pressure drop. If the pressure drop
exceeds 3 psig, replace both the suction-line and liquid-line driers.
After a total of 10 hours run time where the suction-line pressure
drop has not exceeded 3 psig, replace the liquid line drier, and
remove the suction-line drier. Never leave a suction-line drier in
the system longer than 50 hours of run time.
TABLE 1:
Maximum / Minimum Operating Limit Conditions
AIR TEMPERATURE AT
OUTDOOR COIL, °F
AIR TEMPERATURE AT
INDOOR COIL, °F
Min.
Max.
Min.
Max.
DB
Cool
DB
Heat
DB
Cool
DB
Heat
WB
Cool
DB
Heat
WB
Cool
DB
Heat
50° F
-20° F
125° F
75° F
57° F
50° F
72° F
80° F
Operation below this temperature is permissible for a short period of time,
during morning warm-up.
NOTICE
For multiple unit installations, units must be spaced a minimum of
24” (61 cm) apart (coil face to coil face).