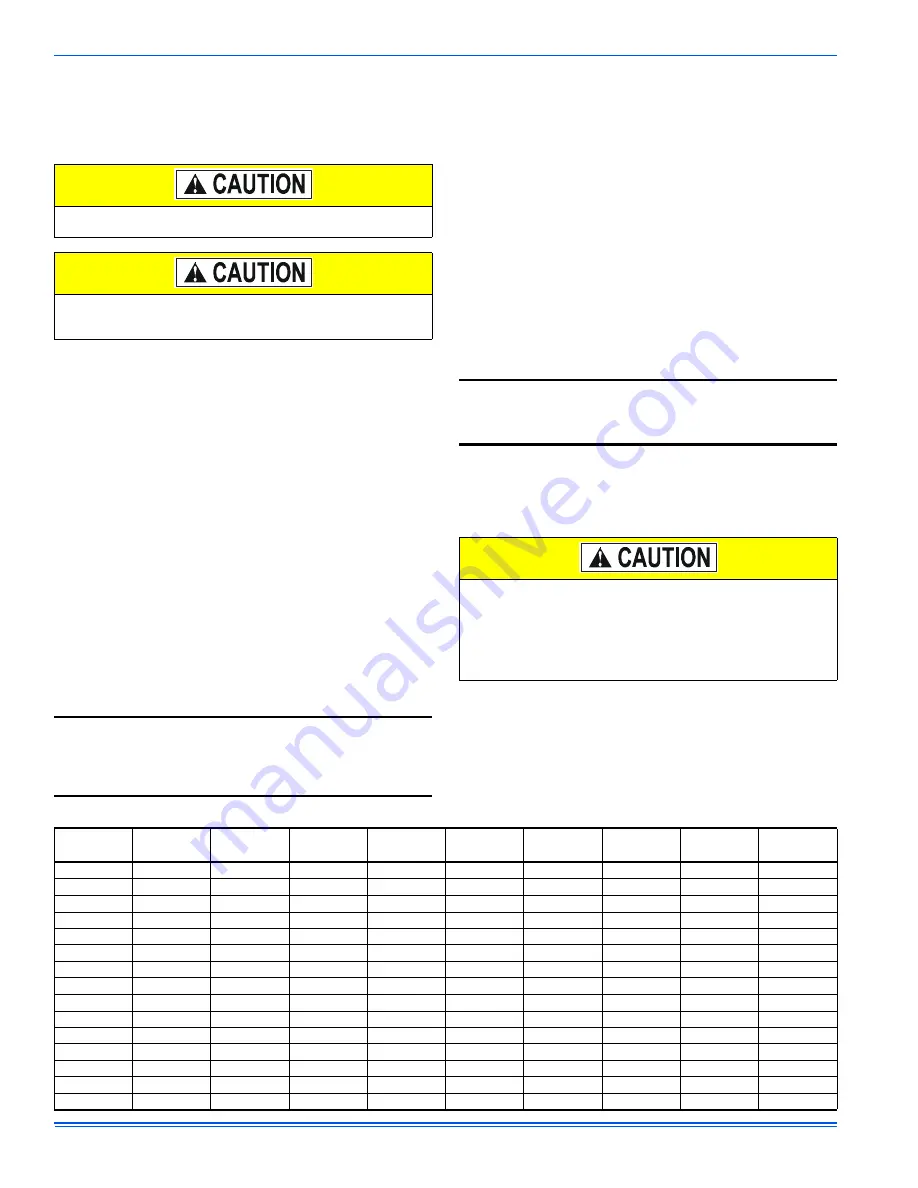
352867-UIM-A-0208
6
Unitary Products Group
4.
Total system charge = item 1 + item 2 + item 3.
5.
Permanently stamp the unit data plate with the total amount of
refrigerant in the system.
Use the following charging method whenever additional refrigerant is
required for the system charge.
If a calibrated charging cylinder or accurate weighing device is avail-
able, add refrigerant accordingly. Otherwise, model-specific charging
charts are provided on the access panel of the unit.
SUPERHEAT CHARGING METHOD -
PISTON INDOOR
1.
Set the system running in cooling mode by setting the thermostat
at least 6°F below the room temperature and operate system for at
least 10 – 15 minutes.
2.
Refer to the technical guide for the recommended airflow and ver-
ify indoor airflow (it should be about 400 SCFM per ton)
3.
Measure and record the outdoor ambient (DB) temperature and
the suction pressure at the suction service valve.
4.
Using the charging chart located on the unit, find the intersection
of the outdoor ambient dry bulb and the suction pressure obtained
in step 3. This is the recommended suction tube temperature at
the service valve.
5.
Measure and record the suction tube temperature at the service
valve and compare to the recommended temperature obtained in
step 4.
6.
Add charge if the measured suction temperature in step 5 is above
the recommended value. Remove / recover refrigerant if the mea-
sured suction temperature is below the recommended value.
SUBCOOLING CHARGING METHOD - TXV INDOOR
For cooling operation, unless otherwise specified, the default subcool-
ing is 10°F.
1.
Set the system running in cooling mode by setting the thermostat
at least 6°F below the room temperature and operate system for at
least 10 – 15 minutes.
2.
Refer to the technical guide for the recommended indoor airflow
and verify it is correct (it should be about 400 SCFM per ton).
3.
Measure and record the indoor wet bulb (WB) and the outdoor
ambient dry bulb (DB) temperature.
4.
Using the charging chart located on the unit, find the intersection
of the indoor wet bulb and the outdoor dry bulb. This is the recom-
mended liquid pressure (and subcooling value).
5.
Measure and record the pressure at the liquid valve pressure port
and compare to the value obtained in step 4.
6.
Add charge if the measured liquid pressure is lower than the rec-
ommended value. Remove / recover charge if the measured liquid
pressure is above the recommended value.
Condenser subcooling is obtained by calculating the difference of the
saturated refrigerant temperature of the pressure measured at the liquid
base valve and the liquid tube temperature as measured at the liquid
base valve.
Subcooling Temp. (TC) = Saturated Temp. (TS) – Liquid Temp. (T)
Refrigerant charging should only be carried out by a qualified air
conditioning contractor.
Compressor damage will occur if system is improperly charged. On
new system installations, charge system per tabular data sheet for
the matched coil and follow guidelines in this instruction.
Example: The suction tube temperature listed on the table at the
intersection of the outdoor DB and the suction pressure is 63°. Tem-
perature of the suction tube at the service valve is 68°. It would be
necessary to add refrigerant to drop the suction tube temperature to
63°.
Example: The liquid pressure listed at the intersection of the indoor
WB and the outdoor DB 320 psig. Pressure at the liquid valve is 305
psig. It would be necessary to add refrigerant to increase the liquid
pressure to 320 psig.
IT IS UNLAWFUL TO KNOWINGLY VENT, RELEASE OR DIS-
CHARGE REFRIGERANT INTO THE OPEN AIR DURING
REPAIR, SERVICE, MAINTENANCE OR THE FINAL DISPOSAL
OF THIS UNIT.
WHEN THE SYSTEM IS FUNCTIONING PROPERLY AND THE
OWNER HAS BEEN FULLY INSTRUCTED, SECURE THE
OWNER’S APPROVAL.
TABLE 2:
R-410A Saturation Properties
TEMP.
°
F
PRESSURE
PSIG
TEMP.
°
F
PRESSURE
PSIG
TEMP.
°
F
PRESSURE
PSIG
TEMP.
°
F
PRESSURE
PSIG
TEMP.
°
F
PRESSURE
PSIG
45
130
60
170
75
217
90
274
105
341
46
132
61
173
76
221
91
278
106
345
47
135
62
176
77
224
92
282
107
350
48
137
63
179
78
228
93
287
108
355
49
140
64
182
79
232
94
291
109
360
50
142
65
185
80
235
95
295
110
365
51
145
66
188
81
239
96
299
111
370
52
147
67
191
82
243
97
304
112
375
53
150
68
194
83
247
98
308
113
380
54
153
69
197
84
250
99
313
114
385
55
156
70
201
85
254
100
317
115
391
56
158
71
204
86
258
101
322
116
396
57
161
72
207
87
262
102
326.
117
401
58
164
73
211
88
266
103
331
118
407
59
167
74
214
89
270
104
336
119
412