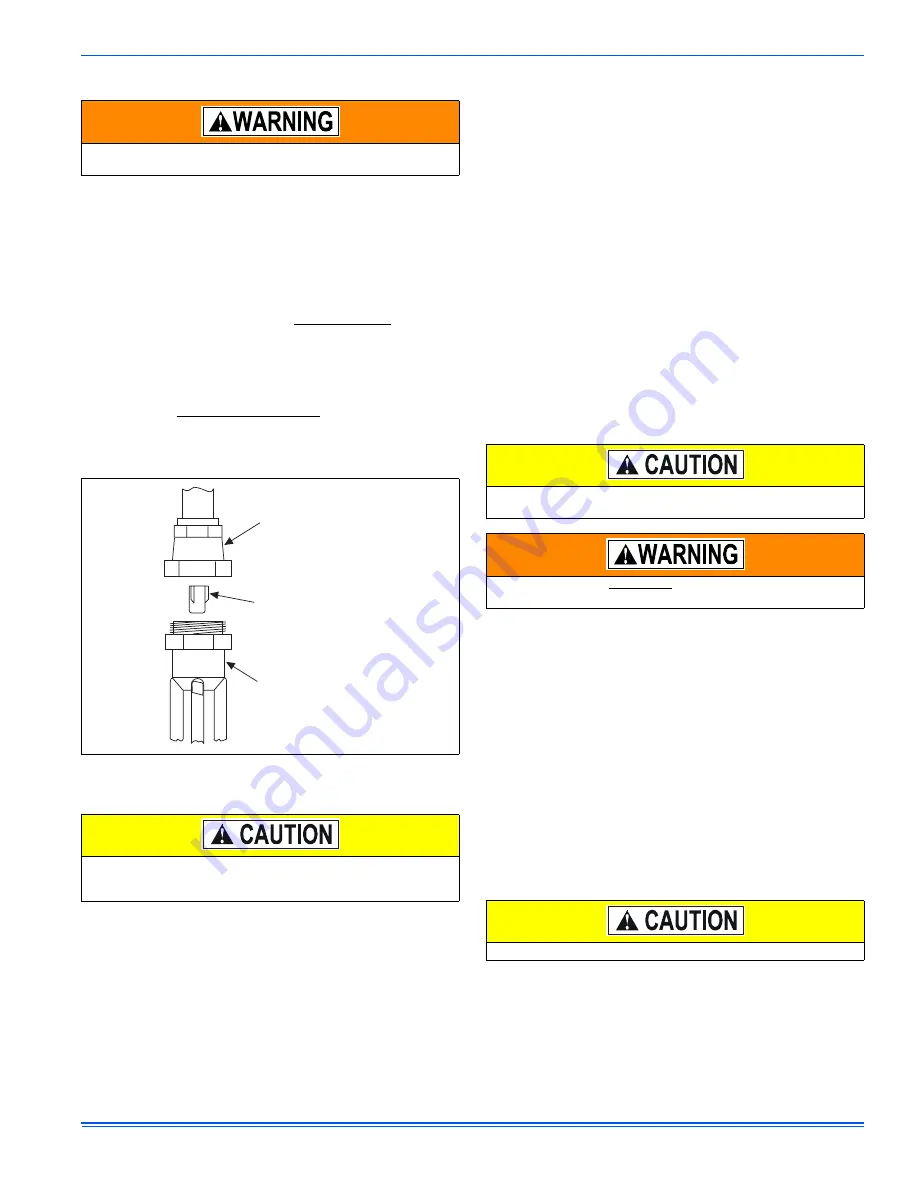
352867-UIM-A-0208
Unitary Products Group
5
SECTION IV: ORIFICE INSTALLATION
Install Schrader Valve Core and Orifice as follows:
1.
Slide indoor coil out of cabinet far enough to gain access to equal-
izer fitting on the suction line.
2.
After holding charge is completely discharged remove black plas-
tic cap on equalizer fitting.
3.
Install Schrader Valve Core supplied with the outdoor unit into
equalizer fitting using a valve core tool.
4.
Loosen and remove the liquid line fitting from the orifice distributor
assembly. Note that the fitting has right hand threads.
5.
Install proper size orifice supplied with outdoor unit. Refer to sup-
plied Tabular Data Sheet for specific orifice size and indoor coil
match up.
6.
After orifice is installed reinstall the liquid line to the top of the ori-
fice distributor assembly. Hand tighten and turn an additional 1/8
turn to seal. Do not over tighten fittings.
7.
Leak test system.
8.
Replace black plastic cap on equalizer fitting.
9.
Slide indoor coil back into cabinet.
SECTION V: TXV INSTALLATION
The following are the basic steps for installation. For detailed instruc-
tions, refer to the Installation Instructions accompanying the TXV kit.
Install TXV kit as follows:
IMPORTANT:
Only 1TVM900 series valves are to be used on this prod-
uct.
1.
Relieve the holding charge by pulling off the rubber cap plug on
the suction manifold line of the coil.
2.
After holding charge is completely discharged, loosen and remove
the schraeder cap seal.
3.
Loosen and remove distributor cap seal.
4.
Install the thermal expansion valve to the orifice distributor assem-
bly with supplied fittings. Hand tighten and turn an additional 1/4
turn to seal. Do not overtighten fittings.
5.
Install the liquid line to the top of the thermal expansion valve with
fitting supplied with the liquid line. Hand modify the liquid line to
align with casing opening. Hand tighten the liquid line and an addi-
tional 1/4 turn to seal.
6.
Install the TXV equalizer line into the vapor line as follows:
a.
Hand tighten the 1/4” SAE nut to the schraeder fitting and an
additional 1/3 turn to seal.
7.
Install the TXV bulb to the vapor line near the equalizer line, using
the bulb clamp(s) furnished with the TXV assembly. Ensure the
bulb is making maximum contact.
a.
Bulb should be installed on a horizontal run of the vapor line if
possible. The bulb should be installed on top of the line.
b.
If bulb installation is made on a vertical run, the bulb should
be located at least 16 inches from any bend, and on the tub-
ing sides opposite the plane of the bend. The bulb should be
positioned with the bulb tail at the top, so that the bulb acts as
a reservoir.
c.
Bulb should be insulated using thermal insulation provided to
protect it from the effect of the surrounding ambient tempera-
ture. Cover completely to insulate from air-stream.
SECTION VI: EVACUATION
It will be necessary to evacuate the system to 500 microns or less. If a
leak is suspected, leak test with dry nitrogen to locate the leak. Repair
the leak and test again.
To verify that the system has no leaks, simply close the valve to the vac-
uum pump suction to isolate the pump and hold the system under vac-
uum. Watch the micron gauge for a few minutes. If the micron gauge
indicates a steady and continuous rise, it’s an indication of a leak. If the
gauge shows a rise, then levels off after a few minutes and remains
fairly constant, it’s an indication that the system is leak free but still con-
tains moisture and may require further evacuation if the reading is
above 500 microns.
SECTION VII: SYSTEM CHARGE
The factory charge in the outdoor unit includes enough charge for the
unit, a 15 ft. line set, and the smallest indoor coil match-up. Some
indoor coil matches may require additional charge. See tabular data
sheet provided in unit literature packet for charge requirements.
The “TOTAL SYSTEM CHARGE” must be permanently stamped on the
unit data plate.
Total system charge is determined as follows:
1.
Determine outdoor unit charge from tabular data sheet.
2.
Determine indoor coil adjustment from tabular data sheet.
3.
Calculate the line charge using the tabular data sheet if line length
is greater than 15 feet.
Failure to install Schrader Valve Core on orifice applications could
result in total refrigerant loss of the system!
FIGURE 5:
Orifice Installation
When using a TXV, 13 SEER models 12-48 require a hard start kit.
Models 12-48 with a “H” on the end of the model number have a
factory installed hard start.
LIQUID LINE
SWIVEL COUPLING
(This fitting is a right-hand thread,
turn counter-clockwise to remove)
ORIFICE
DISTRIBUTOR
In all cases, mount the TXV bulb after vapor line is brazed and has
had sufficient time to cool.
Schrader valve core MUST NOT be installed with TXV installation.
Poor system performance or system failure could result.
Do not leave the system open to the atmosphere.