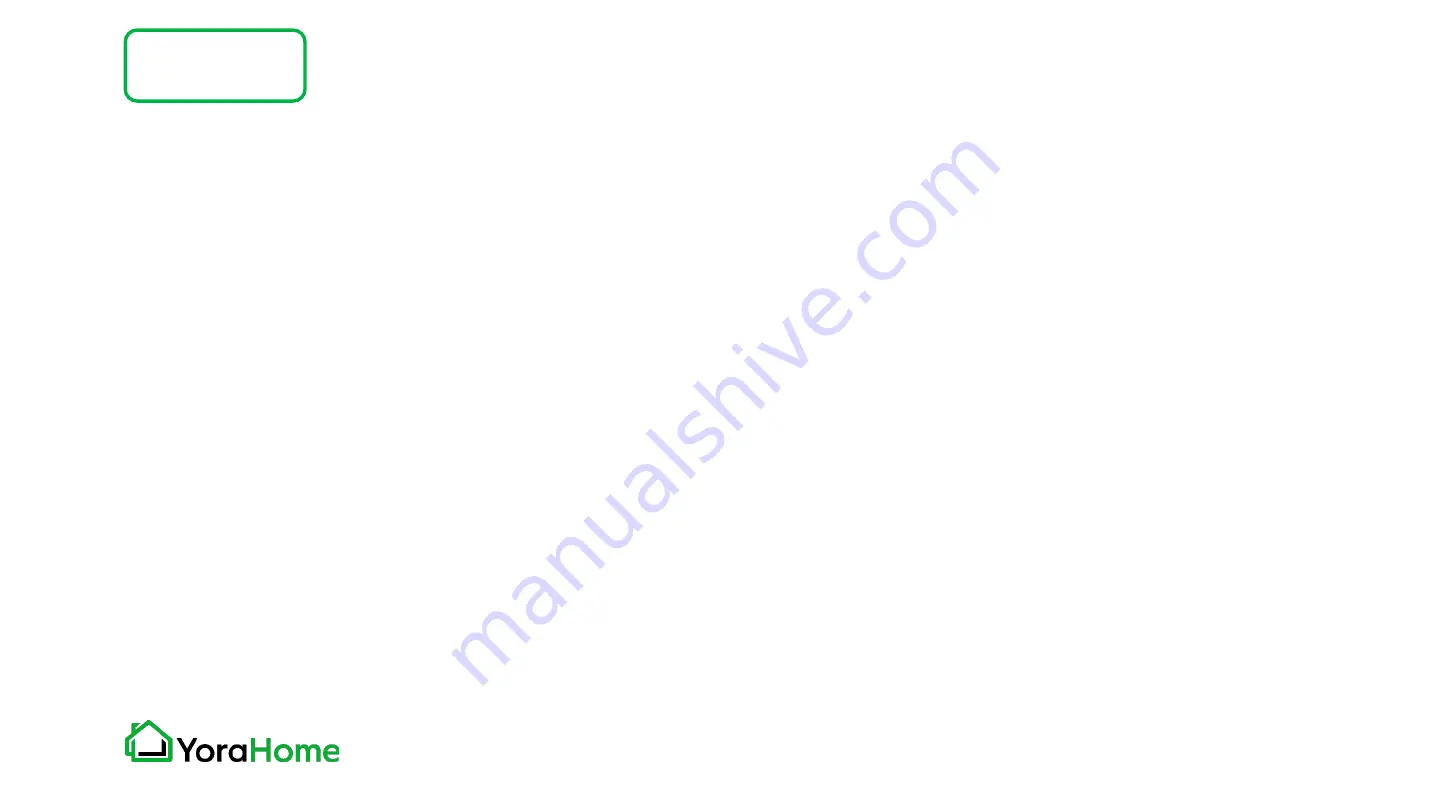
Best Practices For Assembly & Setup
Part 7
Quick Guide
1. Ensure everything is wired and powered correctly per the
manufacturer guidelines.
2. Ensure your axes move freely and don't obviously bind. If you
can't easily tell, try removing your steppers and check if they run
under no load.
3. Ensure your stepper motors and axes linear mechanisms are
all tight and secure. Small set screws on drivetrain components
becoming loose is a very common problem. Re-tighten and try
applying some non-permanent thread locker (Loctite blue) if it
continually loosens.
4. For more difficult issues, try the process of elimination to
quickly isolate the problem. Start by disconnecting everything
from the Arduino (controller board). Test if Grbl is operating ok
by itself. Then, add one thing at a time and test.
5. If your steppers are powered and making a grinding noise
when trying to move, try lowering the '$' acceleration and max
rate settings. This sound is a sign that your steppers are losing
steps and not able to keep up due to too much torque load or
going too fast.
6. Next, you need to make sure your machine is
moving in the correct directions according to a
Cartesian(XYZ) coordinate frame. Check all axes. If
an axis is not moving correctly, alter the $3
direction port mask setting to invert the direction.
Just keep in mind that motions are relative to the
tool. So on a typical CNC gantry router, the tool will
move rather than the fixed table. If the x-axis is
aligned positive to the right, a positive motion
command will move the tool to the right. Whereas,
a moving table with a fixed tool will move the table
to the left for the same command, because the tool
is moving to the right relative to the table.
7. Finally, tune your settings to get close to your
desired or max performance. Start by ensuring your
$100,$101, and $102 axes step/mm settings are
correct for your setup.