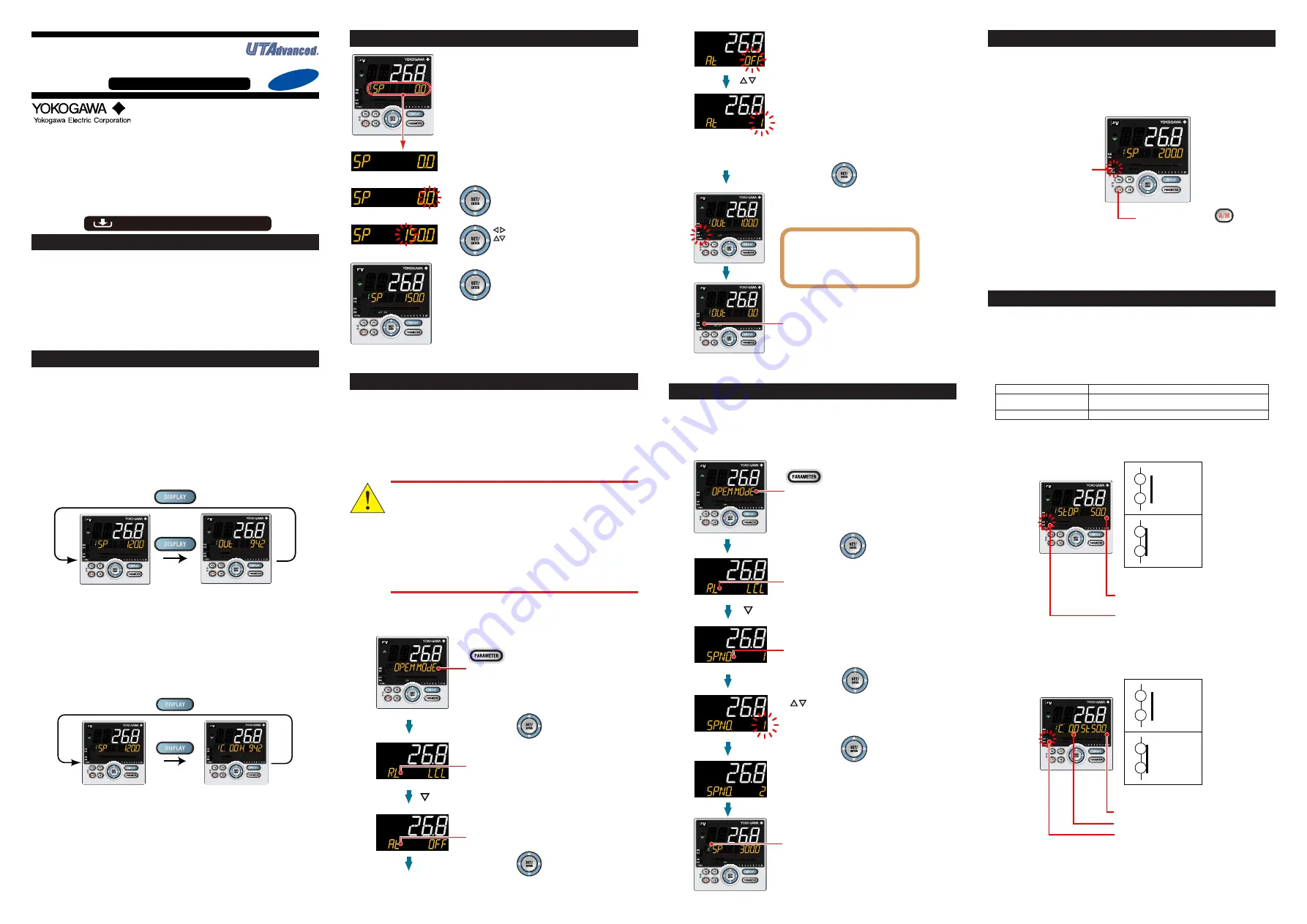
IM 05P01C31-15EN page 7/12
Contents
1. Monitoring-purpose Operation Displays Available during Operation
2. Setting Target Setpoint (SP)
3. Performing/Canceling Auto-tuning
4. Selecting Target Setpoint Numbers (SPNO.)
5. Switching between AUTO and MAN
6. Switching between RUN and STOP
7. Switching between REM (Remote) and LCL (Local)
8. Manipulating Control Output in Manual Mode
9. Troubleshooting
1. Monitoring-purpose Operation Displays Available during Operation
■
Operation Display Switching Diagram for Standard and Posi-
tion Proportional Types
• SP Display
Displays the measured input value on PV display.
Displays the target setpoint (SP) on Setpoint display (SP can be changed).
• OUT Display
Displays the measured input value on PV display.
Displays the control output value (OUT) on Setpoint display (OUT can be changed
in manual mode).
Displays the valve’s feedback input value (at 0 to 100% valve opening) in Position
proportional control.
SP Display
(SP can be changed.)
OUT Display
(OUT can be changed.)
■
Operation Display Switching Diagram for Heating/Cooling Type
• SP Display
Displays the measured input value on PV display.
Displays the target setpoint (SP) on Setpoint display (SP can be changed).
• OUT Display
Displays the measured input value on PV display.
Displays the control output values (C.H.) of heating and cooling sides on Setpoint
display (C.H. can be changed in manual mode).
SP Display
(SP can be changed.)
Heating/cooling OUT Display
(OUT can be changed.)
After showing the OUT Display, press the DISPLAY key or DISP key to show the fol-
lowing displays conditionally. For details, see User’s Manual (IM 05P01C31-01EN).
Standard, Position Proportional, and Heating/Cooling Types
• SELECT Displays 1 to 5 (which appear when registered)
• Analog Input Display (display only) (factory default: non-display)
•
Position Proportional Computation Output Display (display only) (factory default: non-display)
• PID Number Display (display only) (factory default: non-display)
•
Heater Break Alarm-1 Current Display (display only) (for heater break alarm option only)
•
Heater Break Alarm-2 Current Display (display only) (for heater break alarm option only)
2. Setting Target Setpoint (SP)
When the required value is displayed,
press the SET/ENTER key to register
the setpoint.
Show the SP Display (Operation Display).
(This is an example of setting the target
setpoint to 150.0).
Press the SET/ENTER key to start the
last digit of the setpoint blinking.
Blinking allows you to change the value.
To set the setpoint, use the
Left/Right arrow keys to move
between digits and the Up/Down
arrow keys to increase and
decrease the value.
1.
2.
3.
4.
3. Performing/Canceling Auto-tuning
Auto-tuning should be performed after setting a target setpoint.
Make sure that the controller is in automatic mode (AUTO) and in run mode (RUN)
before auto-tuning. For setting to AUTO, see “5. Switching between AUTO and
MAN,” and for setting to RUN, see “6. Switching between RUN and STOP.”
If the setpoint is known in advance or auto-tuning does not find any appropriate PID
constants, set the PID manually. For setting the PID manually, see User’s Manual (IM
05P01C31-01EN).
CAUTION
Do not perform auto-tuning for the following processes.
Tune PID manually.
• Processes with fast response such as flow rate control and pres-
sure control.
• Processes which do not allow the output to be turned on and off
even temporarily.
• Processes which prohibit severe output changes at control
valves (or other actuators).
• Processes in which product quality can be adversely affected if
PV values fluctuate beyond their allowable ranges.
Show the Operation Display.
Hold down the PARAMETER key or PARA key for
3 seconds to display MODE menu.
Press the SET/ENTER key.
Press the SET/ENTER key.
Press the Down arrow key until the parameter AT appears.
The parameter AT (auto-tuning switch) is displayed.
1.
2.
3.
4.
The parameter R.L (REMOTE/LOCAL switch)
is displayed.
Press the SET/ENTER key.
During auto-tuning,
• The MAN lamp blinks.
• The OUT symbol appears.
• The output values at 100.0% and
0% appear alternately.
OFF blinks.
Press the Up/Down arrow keys to display the required setpoint.
Blinks during the change.
The setpoint has been registered.
This starts auto-tuning.
The limiter can be set to the output during auto-tuning.
For details, see User’s Manual (IM 05P01C31-01EN).
The MAN lamp goes off, which means that
the auto-tuning completed normally.
5.
6.
7.
8.
The setting range is 1 to 8 (represent group numbers) or R.
To perform auto-tuning for the PID of group 1, set the parameter AT to 1.
To quit the auto-tuning, set the parameter to OFF.
4. Selecting Target Setpoint Numbers (SPNO.)
The following operating procedure shows an example of changing the target setpoint
number (SPNO.) from 1 to 2. Each SP has its PID group. The PID group set for the
parameter PIDN (PID number selection) is used.
Show the Operation Display.
Hold down the PARAMETER key or PARA key for
3 seconds to display MODE menu.
Press the SET/ENTER key.
SPNO. has been changed to 2.
Blinks during the change.
The setpoint has been registered.
Press the DISPLAY key or DISP key once
to return to the Operation Display.
Change the setpoint using
the Up/Down arrow keys.
Press the Down arrow key until the parameter SPNO.
appears.
Press the SET/ENTER key.
Press the SET/ENTER key.
1.
2.
3.
4.
5.
6.
7.
The parameter R.L (REMOTE/LOCAL switch) is
displayed.
The parameter SPNO. (SP number selection)
is displayed.
Operation
Guide
UT55A, UT52A
Digital Indicating Controller
(Panel Mounting Type)
Operation Guide for Single-loop Control
This operation guide describes key entries for operating the UT55A and UT52A.
Although the display of UT55A is used in this guide, UT52A can be operated similarly.
For operations using external contact inputs, see “DI” of “6. Terminal Wiring Diagrams”
in “Installation and Wiring.”
If you cannot remember how to carry out an operation during setting, press the
DISPLAY key or DISP key once. This brings you to the display (Operation Display) that
appears at power-on.
The scrolling guide is displayed on PV display in the Parameter Setting Display.
This guide can be turned on/off with the Fn key.
Operations
For details of the each function, refer to the electronic manual. Manuals can be
downloaded or viewed at the following URL.
Functional
Enhancement
http://www.yokogawa.com/ns/ut/im/
«Detailed Code Model»
5. Switching between AUTO and MAN
AUTO and MAN switching can be performed using any of the following: (1) A/M key,
(2) Contact input, (3) Communication, and (4) User function key.
The figure below shows a direct operation using the A/M key.
When AUTO and MAN switching function is assigned to the contact input, and the
contact input is ON, the switching by key operation cannot be performed.
For details, see User’s Manual (IM 05P01C31-01EN).
MAN lamp is lit in MAN mode.
Each time you press the key,
AUTO and MAN is switched alternately.
When AUTO is switched into MAN, the control output value in AUTO mode is held.
The controller can be operated manually from the hold value.
If the manual preset output is set (MPON parameter ≠ OFF), the controller can be
operated manually from the arbitrary output value (MPO1 to MPO5 parameters).
6. Switching between RUN and STOP
RUN and STOP switching can be performed using any of the following: (1) Contact
input, (2) Parameter, (3) Communication, and (4) User function key.
The following shows an example of switching using the contact input.
(The switching function is assigned to DI2 contact for the factory default.)
For details of other switching methods and the display appearing when the operation
is started, see User’s Manual (IM 05P01C31-01EN).
When the controller is stopped, input and outputs are as follows:
PV input
Displays the PV value.
Control output
Displays the preset output value.
The preset output value is set for each PID group.
Alarm output
Turns the output on in case of an alarm.
Display in STOP mode
“STOP” is displayed on Symbol display and "preset output value" is displayed on
Data display.
OFF: Operation RUN
Display in STOP mode
210
212
ON: Operation STOP
210
212
Preset output (PO)
Valve opening (0-100%) for
Position proportional type
STOP lamp is lit.
DI2
DI2
Display in STOP mode in Heating/cooling control
“Cooling-side preset output value” is displayed on the left side of the “ST” symbol,
and “Heating-side preset output value” is on the right side.
OFF: Operation RUN
Display in STOP mode
210
212
ON: Operation STOP
210
212
Heating-side preset output (PO)
STOP lamp is lit
Cooling-side preset output (POc)
.
DI2
DI2