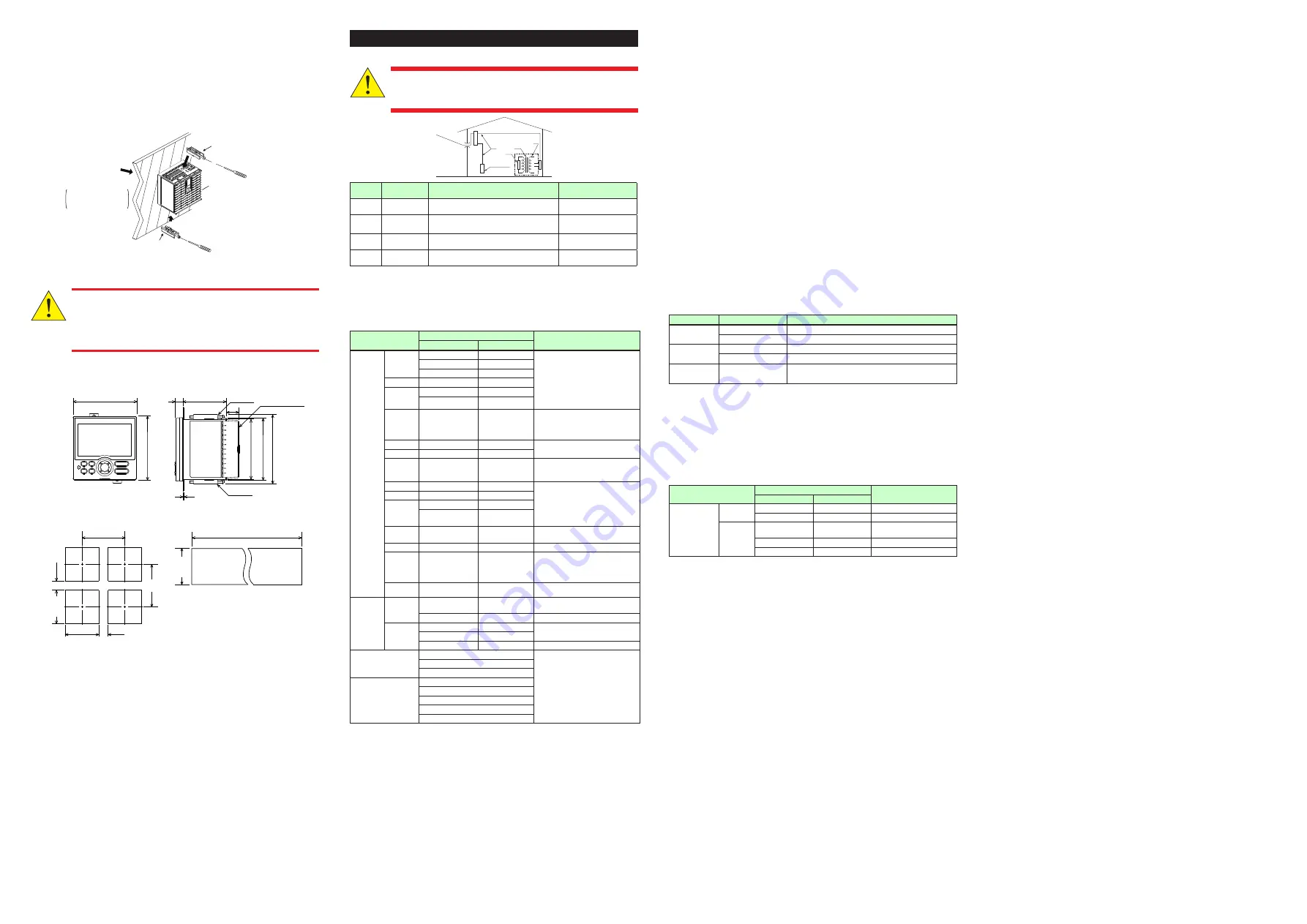
IM 05P02C41-15EN page 2/14
n
Mounting the Instrument Main Unit
Provide an instrumented panel steel sheet of 1 to 10 mm thickness.
After opening the mounting hole on the panel, follow the procedures below to install
the controller:
1) Insert the controller into the opening from the front of the panel so that the
terminal board on the rear is at the far side.
2) Set the brackets in place on the top and bottom of the controller as shown in the
figure below, then tighten the screws of the brackets. Take care not to overtighten
them.
Bracket
(top mounting hardware)
Terminal board
Bracket
(bottom mounting hardware)
Panel
Insert a screwdriver into the
brackets to tighten the screws.
Direction to insert the
controller
Appropriate
tightening torque:
0.25 N
•
m
Insert the controller
into the opening at
the front of the panel.
CAUTION
• Tighten the screws with appropriate tightening torque within 0.25
N•m. Otherwise it may cause the case deformation or the bracket
damage.
• Make sure that foreign materials do not enter the inside of the
instrument through the case’s slit holes.
n
External Dimensions and Panel Cutout Dimensions
(25)
(53) (2.09)
[(N-1)×96+92]
117 (4.61) min.
145 (5.71)
min.
+0.8
0
+0.8
0
92
“N” stands for the number of controllers to be
installed.
However, the measured value applies if N≥5.
65 (2.56)
20 (0.79)
11
(0.43)
UP55A
1 to 10 mm (0.04 to 0.39 inch) (panel thickness)
Bracket
Bracket
94.6 (3.72)
91.6 (3.61)
105.2 (4.14)
Unit: mm (approx. inch)
96 (3.78)
96 (3.78)
• General mounting
• Side-by-side close mounting
Terminal cover
Normal tolerance:
±(value of JIS B 0401-1998 tolerance class IT18)/2
+0.8
0
92
+0.03
0
(3.62 )
(0.98)
+0.03
0
(3.62 )
+0.8
0
92
+0.03
0
(3.62 )
([(N-1)×3.78+3.62] )
+0.03
0
4. Hardware Specifications
WARNING
This instrument is for Measurement Category I (CAT.I). Do not use it
for measurements in locations falling under Measurement Catego-
ries II, III, and IV.
Internal Wiring
Outlet
Entrance IV
Cable
III
T
I
II
Category Measurement
category
Description
Remarks
I
CAT.I
For measurements performed on circuits not
directly connected to MAINS.
-
II
CAT.II
For measurements performed on circuits di
-
rectly connected to the low-voltage installation.
Appliances, portable equip-
ments, etc.
III
CAT.III
For measurements performed in the building
installation.
Distribution board, circuit
breaker, etc.
IV
CAT.IV
For measurements performed at the source of
the low-voltage installation.
Overhead wire, cable
systems, etc.
n
Input Specifications
●Universal Input (Equipped as standard)
• Number of inputs: 1
• Input type, instrument range, and measurement accuracy: See the table below.
Input Type
Instrument Range
Accuracy
ºC
ºF
Thermo-
couple
K
-270.0 to 1370.0ºC -450.0 to 2500.0ºF ±0.1% of instrument range ±1 digit for
0°C or more
±0.2% of instrument range ±1 digit for
less than 0°C
±2% of instrument range ±1 digit for
less than -200.0°C of thermocouple K
±1% of instrument range ±1 digit for
less than -200.0°C of thermocouple T
-270.0 to 1000.0ºC -450.0 to 2300.0ºF
-200.0 to 500.0ºC
-200.0 to 1000.0ºF
J
-200.0 to 1200.0ºC -300.0 to 2300.0ºF
T
-270.0 to 400.0ºC
-450.0 to 750.0ºF
0.0 to 400.0ºC
-200.0 to 750.0ºF
B
0.0 to 1800.0ºC
32 to 3300ºF
±0.15% of instrument range ±1 digit
for 400°C or more
±5% of instrument range ±1 digit for
less than 400°C
S
0.0 to 1700.0ºC
32 to 3100ºF
±0.15% of instrument range ±1 digit
R
0.0 to 1700.0ºC
32 to 3100ºF
N
-200.0 to 1300.0ºC -300.0 to 2400.0ºF
±0.1% of instrument range ±1 digit
±0.25% of instrument range ±1 digit
for less than 0°C
E
-270.0 to 1000.0ºC -450.0 to 1800.0ºF ±0.1% of instrument range ±1 digit for
0°C or more
±0.2% of instrument range ±1 digit for
less than 0°C
±1.5% of instrument range ±1 digit for
less than -200.0°C of thermocouple E.
L
-200.0 to 900.0ºC
-300.0 to 1600.0ºF
U
-200.0 to 400.0ºC
-300.0 to 750.0ºF
0.0 to 400.0ºC
-200.0 to 1000.0ºF
W
0.0 to 2300.0ºC
32 to 4200ºF
±0.2% of instrument range ±1 digit
(Note 2)
Platinel 2
0.0 to 1390.0ºC
32.0 to 2500.0ºF ±0.1% of instrument range ±1 digit
PR20-40
0.0 to 1900.0ºC
32 to 3400ºF
±0.5% of instrument range ±1 digit for
800°C or more
Accuracy is not guaranteed for less
than 800°C.
W97Re3-
W75Re25
0.0 to 2000.0ºC
32 to 3600ºF
±0.2% of instrument range ±1 digit
RTD
JPt100
-200.0 to 500.0ºC
-300.0 to 1000.0ºF ±0.1% of instrument range ±1 digit
(Note 1)
-150.00 to 150.00ºC -200.0 to 300.0ºF ±0.1% of instrument range ±1 digit
Pt100
-200.0 to 850.0ºC
-300.0 to 1560.0ºF ±0.1% of instrument range ±1 digit
(Note 1)
-200.0 to 500.0ºC
-300.0 to 1000.0ºF
-150.00 to 150.00ºC -200.0 to 300.0ºF ±0.1% of instrument range ±1 digit
Standard signal
0.400 to 2.000 V
±0.1% of instrument range ±1 digit
1.000 to 5.000 V
4.00 to 20.00 mA
DC voltage/current
0.000 to 2.000 V
0.00 to 10.00 V
0.00 to 20.00 mA
-10.00 to 20.00 mV
0.0 to 100.0 mV
The accuracy is that in the standard operating conditions: 23±2°C, 55±10%RH, and power
frequency at 50/60 Hz.
Note
1: ±0.3°C ±1 digit in the range between 0 and 100°C, ±0.5°C ±1 digit in the range
between -100 and 200°C.
Note 2: W: W-5% Re/W-26% Re(Hoskins Mfg.Co.). ASTM E988
• Input sampling (control) period: Select from 100 and 200 ms
• Burnout detection:
Functions at TC, RTD, and standard signal.
Upscale, downscale, and off can be specified.
For standard signal, burnout is determined to have occurred if it is 0.1 V or 0.4
mA or less.
• Input bias current: 0.05 µA (for TC or RTD)
• Measured current (RTD): About 0.16 mA
• Input resistance:
TC or mV input: 1 MΩ or more
V input: About 1 MΩ
mA input: About 250 Ω
• Allowable signal source resistance:
TC or mV input: 250 Ω or less
Effects of signal source resistance: 0.1 µV/Ω or less
DC voltage input: 2 kΩ or less
Effects of signal source resistance: About 0.01%/100 Ω
• Allowable wiring resistance:
RTD input: Max. 150 Ω/wire (The conductor resistance between the three wires
shall be equal.)
Wiring resistance effect: ±0.1ºC/10 Ω
• Allowable input voltage/current:
TC, mV, mA and RTD input: ±10 V DC
V input: ±20 V DC
mA input: ±40 mA
• Noise rejection ratio:
Normal mode: 40 dB or more (at 50/60 Hz)
Common mode: 120 dB or more (at 50/60 Hz)
For 100-240 V AC, the power frequency can be set manually.
Automatic detection is also available.
For 24 V AC/DC, the power frequency can be set manually.
• Reference junction compensation error:
±1.0ºC (15 to 35ºC)
±1.5ºC (-10 to 15ºC and 35 to 50ºC)
• Applicable standards: JIS/IEC/DIN (ITS-90) for TC and RTD
●Auxiliary Analog Input
• Use: Remote setpoint setting, external compensating input, auxiliary input for com-
putation, etc.
• Number of inputs: See the table of Model and Suffix Codes.
• Input type, instrument range, and measurement accuracy: See the table below.
Input Type
Instrument Range
Accuracy
Standard signal
0.400 to 2.000 V
±0.2% of instrument range ±1 digit
1.000 to 5.000 V
±0.1% of instrument range ±1 digit
DC voltage
0.000 to 2.000 V
±0.2% of instrument range ±1 digit
0.00 to 10.00 V
±0.1% of instrument range ±1 digit
DC voltage
for high-input
impedance
0.000 to 1.250 V
±0.1% of instrument range ±1 digit
• Input sampling (control) period: Same as universal input
• Input resistance: About 1 MΩ
However, 10 MΩ or more for DC voltage for high-input impedance range
• Burnout detection: Functions at standard signal
Burnout is determined to have occurred if it is 0.1 V or less.
● Universal Input (Optional suffix code: /U1)
• Number of inputs: See the table of Model and Suffix Codes.
• Input type, instrument range, and measurement accuracy: Same as the standard-
equipped universal input except the table below.
Input Type
Instrument Range
Accuracy
°C
°F
4-wire RTD
JPt100
-200.0 to 500.0°C
-300.0 to 1000.0°F ±0.5°C of instrument range ±1 digit
-150.00 to 150.00°C -200.0 to 300.0°F ±0.2°C of instrument range ±1 digit
Pt100
-200.0 to 850.0°C
-300.0 to 1560.0°F ±0.1% of instrument range ±1 digit
(Note 1)
-200.0 to 500.0°C
-300.0 to 1000.0°F ±0.5°C of instrument range ±1 digit
-150.00 to 150.00°C -200.0 to 300.0°F ±0.2°C of instrument range ±1 digit
Note 1
: ±0.5°C ±1 digit in the range between -200.0 and 500.0°C/-300.0 and 1000.0°F.
• Input sampling (control) period: Same as the standard-equipped universal input.
• Burnout detection: Same as the standard-equipped universal input.
n
Analog Output Specifications
• Number of outputs:
Control output: 1
Cooling-side control output of Heating/cooling type: 1
• Output type: Current output or voltage pulse output
• Current output: 4 to 20 mA DC or 0 to 20 mA DC/load resistance of 600 Ω or less
• Current output accuracy: ±0.1% of span (±5% of span for 1 mA or less)
The accuracy is that in the standard operating conditions: 23±2°C, 55±10%RH,
and power frequency at 50/60 Hz.
• Voltage pulse output:
Use: Time proportional output
On-voltage: 12 V or more/load resistance of 600 Ω or more
Off-voltage: 0.1 V DC or less
Time resolution: 10 ms or 0.1% of output, whichever is larger
n
Step Response Time Specifications
Within 500 ms (when the control period is 100 ms)
Within 1 s (when the control period is 200 ms)
(63% of analog output response time when a step change of 10 to 90% of input span
is applied)
n
Triac Output Specifications
• Contact type and number of output: zero cross; 1 point
Load voltage: 75 to 250 VAC
Allowable load current: 0.8 A when the ambient temperature is 20°C, 0.3 A when the
ambient temperature is 50°C.
• Minimum load current: 20 mA (*)
*: Unusable for a small load of 10 mA or less.
*: If there is a risk of surge current, connect a current-limiting reactor, a current-
limiting fuse or a breaker in series to the load power supply.
• Use: Time proportional output, Alarm output
• Time resolution of control output: 1/commercial frequency (s) or 0.1% of output,
whichever is larger.
n
Relay Contact Output Specifications
• Contact type and number of outputs:
Control output: contact point 1c; 1 point
Cooling-side control output of Heating/cooling type: contact point 1c; 1 point
Event output: contact point 1a; 3 points (common is independent)
• Contact rating:
Contact point 1c (control output): 250 V AC, 3 A or 30 V DC, 3A (resistance load)
Contact point 1a (event output): 240 V AC, 1A or 30 V DC, 1 A (resistance load)
• Use: Time proportional output, event output, alarm output, FAIL output, etc.
• Time resolution of control output: 10 ms or 0.1% of output, whichever is larger
Note: This cannot be used for a small load of 10 mA or less.
n
Position Proportional Output Specifications
• Position signal input:
Slide resistance: 100 Ω to 2.5 kΩ of total resistance
100% side and slide line: with disconnection detection
0% side: without disconnection detection
Current input: 4 to 20 mA (with disconnection detection)
• Sampling period: 50 ms
• Measurement resolution: 0.1% of input span
• Position proportional relay output:
Contact point 1a; 2 points, 250 V AC, 3 A or 30 V DC, 3 A (resistance load)
Note: This cannot be used for a small load of 10 mA or less.
n
Retransmission Output Specifications
• Number of outputs: Retransmission output; 1, shared with 15 V DC loop power
supply
• Current output: 4 to 20 mA DC or 0 to 20 mA DC/ load resistance of 600 Ω or less
• Current output accuracy: ±0.1% of span (±5% of span for 1 mA or less)
The accuracy is that in the standard operating conditions: 23±2°C, 55±10%RH,
and power frequency at 50/60 Hz.
n
15 V DC Loop Power Supply Specifications
(Shared with retransmission output)
• Power supply: 14.5 to 18.0 V DC
• Maximum supply current: About 21 mA (with short-circuit current limiting circuit)
n
Contact Input Specifications
• Number of inputs: See the table of Model and Suffix Codes.
• Input type: No-voltage contact input or transistor contact input
• Input contact rating: 12 V DC, 10 mA or more
Use a contact with a minimum on-current of 1 mA or more.
• ON/OFF detection:
No-voltage contact input:
Contact resistance of 1 kΩ or less is determined as “ON” and contact
resistance of 50 kΩ or more as “OFF.”
Transistor contact input:
Input voltage of 2 V or less is determined as “ON” and leakage current must
not exceed 100 µA when “OFF.”
• Minimum status detection hold time: Control 50 ms
• Use: PTNO. switch, operation mode switch, and event input
n
Transistor Contact Output Specifications
• Number of outputs: See the table of Model and Suffix Codes.
• Output type: Open collector (SINK current)
• Output contact rating: Max. 24 V DC, 50 mA
• Output time resolution: Min. 100 ms
n
Heater Break Alarm Specifications
• Number of inputs: 2
• Number of outputs: 2 (transistor contact output)
• Use: Measures the heater current using an external current transformer (CT) and
generates a heater break alarm when the measured value is less than the break
detection value.
• Current transformer input resistance: About 9.4 Ω
• Current transformer input range: 0.0 to 0.1 Arms (0.12 Arms or more cannot be ap-
plied.)
• Heater current setting range: OFF, 0.1 to 300.0 Arms
Heater current measured value display range: 0.0 to 360.0 Arms
Note: The CT ratio can be set. CT ratio setting range: 1 to 3300
• Recommended CT: CT from U.R.D., Ltd.
CTL-6-S-H: CT ratio 800, measurable current range: 0.1 to 80.0 Arms
CTL-12L-30: CT ratio 3000, measurable current range: 0.1 to 180.0 Arms
• Heater current measurement period: 200 ms
• Heater current measurement accuracy: ±5% of current transformer input range
span ± 1digit (CT error is not included.)
• Heater current detection resolution: Within 1/250 of current transformer input range span
• Break detection On-time: Min. 0.2 second (for time proportional output)