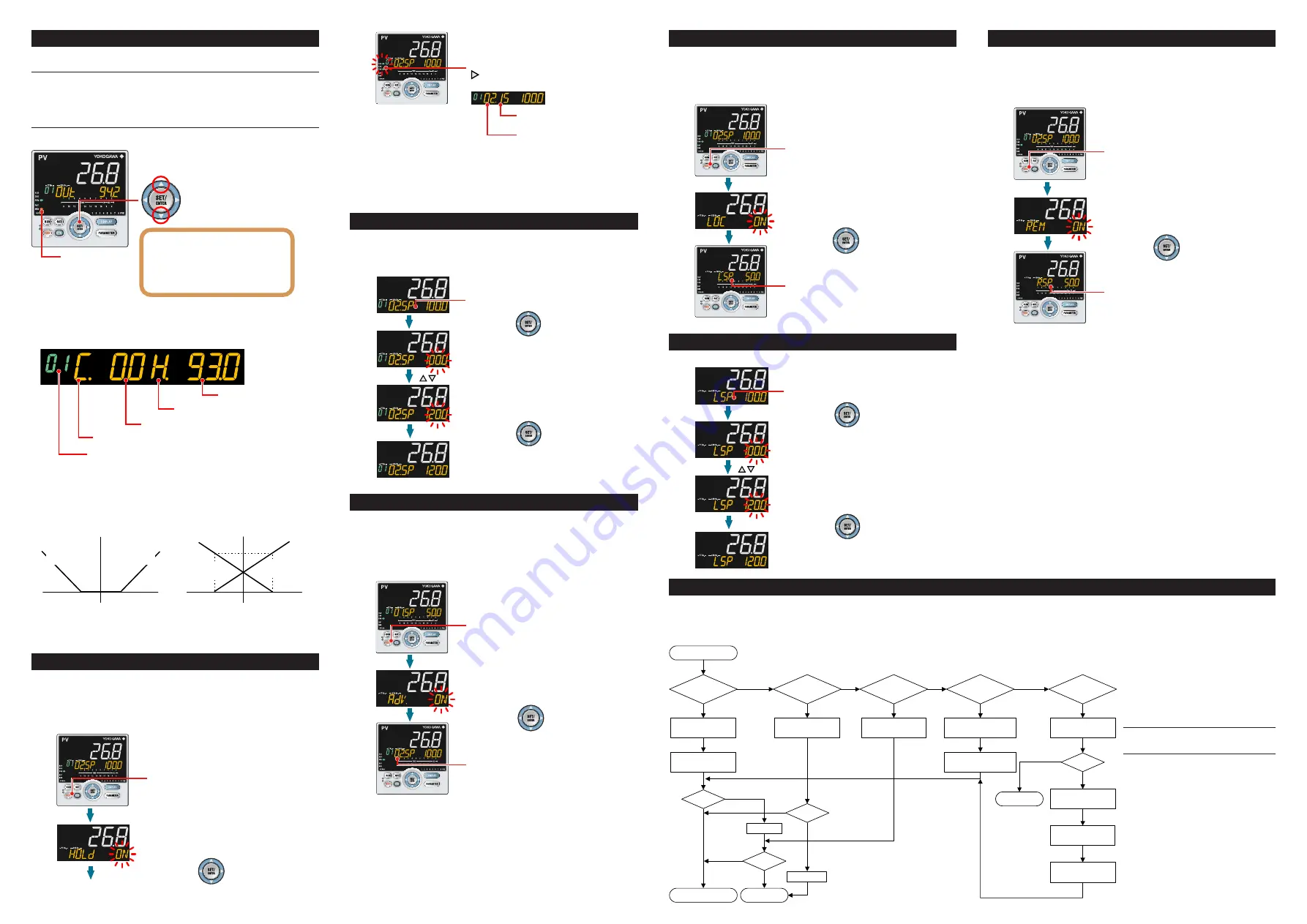
IM 05P02C41-15EN page 10/14
6. Manipulating Control Output in Manual Mode
NOTE
In manual mode, control output is manipulated by operating the keys (the value is
changed using the Up/Down arrow keys, then outputted as it is).
Even if the SET/ENTER key is not pressed, the control output value changes ac-
cording to the displayed value.
In stop mode (when the RST lamp is lit), control output cannot be manipulated.
MAN lamp is lit.
Up arrow key: increases control output.
Down arrow key: decreases control output.
In Position proportional control:
Up arrow key; opens the valve.
Down arrow key; closes the valve.
Output; only while pressing a key.
OUT; valve opening (0-100%)
Output manipulation in Position proportional control
is not restricted from output limiters (OH, OL).
Manual operation in Heating/cooling control
Symbol of cooling side
Program pattern (PTNO.) number
Symbol of heating side
Heating-side control output
Cooling-side control output
Up arrow key: concurrently decreases cooling-side control output and increases
heating-side control output.
Down arrow key: concurrently increases cooling-side control output and decreases
heating-side control output.
(Either none of the heating-side and cooling-side outputs are presented, or both of
them are presented according to the dead band setting.)
Actual output (%)
DB=24.8
Dead band: Operation parameter DB
Control computation output
Control computation output
12.4
0
-12.4
Manipulated output change
when a dead band is positive (+)
Actual output (%)
100
DB= -24.8
12.4
0
-12.4
Manipulated output change
when a dead band is negative (-)
100
Cooling-side
manipulated output
Heating-side
manipulated output
Heating-side
manipulated output
Cooling-side
manipulated output
7. Enabling/Disabling Hold Mode of Program Operation
Enabling/disabling hold mode of program operation can be performed during pro-
gram operation using any of the following: (1) MODE key, (2) Parameter, (3) Contact
input, and (4) Communication.
The following shows an example of switching using the MODE key.
1.
2.
3.
4.
Show the Operation Display.
Press the MODE key.
The number of segments included
in the selected program pattern.
The segment number for which
operation is in progress.
The figure below is displayed while the right
arrow key hold down.
Displays ”HOLD ON” in PROG mode.
Displays ”HOLD OFF” in HOLD mode.
HLD lamp is lit in HOLD mode.
Press the SET/ENTER key.
The parameter HOLD (Pause/cancel release
of program operation) is displayed (during
program operation.)
1.
2.
3.
4.
Show the Operation Display.
Press the MODE key.
The number of segments included
in the selected program pattern.
The segment number for which
operation is in progress.
The figure below is displayed while the right
arrow key hold down.
Displays ”HOLD ON” in PROG mode.
Displays ”HOLD OFF” in HOLD mode.
HLD lamp is lit in HOLD mode.
Press the SET/ENTER key.
The parameter HOLD (Pause/cancel release
of program operation) is displayed (during
program operation.)
Other operating procedures for disabling the hold mode:
(1) Press the RUN key for 1 second during hold-mode operation. In this case, the
controller resumes program operation.
(2) Execute the “Advance“ function during hold-mode operation. In this case, the
segment is advanced.
. Changing Program Setpoints when in Hold Mode
The following operating procedures changes a program setpoint of soak segment
during Hold-mode operation.
The program operation is started when releasing the Hold after changing the pro-
gram setpoint.
1.
2.
Set program operation in hold mode.
3.
4.
Blinks during the change.
Blinks during the change.
Press the SET/ENTER key.
Press the SET/ENTER key.
Press the Up/Down arrow keys to display the required setpoint.
9. Executing “Advance” Function
“Advance” can be performed during program operation using any of the following: (1)
MODE key, (2) Parameter, (3) Contact input, and (4) Communication.
The following shows an example of switching using the MODE key.
When executing the “Advance” function during hold-mode operation, the hold mode
is disabled.
1.
2.
3.
4.
The segment is advanced.
Press the SET/ENTER key.
Show the Operation Display.
Press the MODE key.
The ADV (Advance of segment) is displayed (during
program operation.)
10. Switching to Local-mode (LOCAL) Operation
Switching to local-mode can be performed using any of the following:
(1) MODE key (user function key), (2) Parameter, (3) Contact input, and (4) Commu-
nication.
The following shows an example of switching using the MODE key.
1.
2.
3.
4.
“LSP” is displayed when in
local-mode operation.
Press the SET/ENTER key.
Show the Operation Display.
Press the MODE key several times.
The LOC (local operation) is displayed.
11. Changing Setpoints during Local-mode Operation
The following operating procedures changes setpoints during local-mode operation.
1.
2.
3.
4.
“LSP” is displayed when in local-mode operation.
Press the SET/ENTER key.
Press the SET/ENTER key.
Blinks during the change.
Blinks during the change.
Press the Up/Down arrow keys to display the required setpoint.
13. Troubleshooting
■
Remedies if Power Failure Occurs
during Operations
• Instantaneous power failure within 20 ms.
A power failure is not detected. Normal
operation continues.
• Power failure for less than about 5 seconds,
or for about 5 seconds or more.
Affects the "settings" and "operation sta-
tus."
For details, see User's Manual.
NOTE
Write down the settings of parameters for a
repair request.
■ For the Errors at Power On
and the Errors during Op-
eration, see “Installation”
in this manual.
12. Switching to Remote-mode (REM) Operation
Switching to remote-mode can be performed using any of the following:
(1) MODE key (user function key), (2) Parameter, (3) Contact input, and (4) Commu-
nication.
The following shows an example of switching using the MODE key.
1.
2.
3.
4.
“R.SP” is displayed when in
remote-mode operation.
Press the SET/ENTER key.
Show the Operation Display.
Press the MODE key several times.
The REM (remote operation) is displayed.
■ Troubleshooting Flow
If the Operation Display does not appear after turning on the controller’s power, check the procedures in the following flowchart.
If a problem appears to be complicated, contact our sales representatives.
Is the controller
defective?
Contact us for repair. Problem solved.
No communication
capability
Completely
inactive?
Yes
Yes
Yes
No
No
No
Key
operation
failure?
Yes
No
Yes
Check wiring of the
power terminals.
Check the key lock
setting.
Display
failure?
*
Yes
No
Turn off power, and
then turn it on again.
I/O signal
failure?
Yes
No
Check the
supply voltage.
Check the
specifications and polarity
of connected devices .
Check the communication-
related parameters.
Check the specifications
of communication
devices.
Check the
communication wiring.
Communication
failure?
No
With
communi-
cation?
Yes
Yes
Normal?
Is the
key locked?
Check the specifications
of the controller.
Yes
No
Correct?
Correct the error(s).
Cancel the setting.
Check the I/O specifications
of the controller.
* The LCD (a liquid crystal display) is used for
a display portion of this product.
The LCD has a characteristic that the display action
becomes late at the low temperature.
Additionally, the luminance and contrast degradation
are caused due to aged deterioration.
However, the control function is not affected.