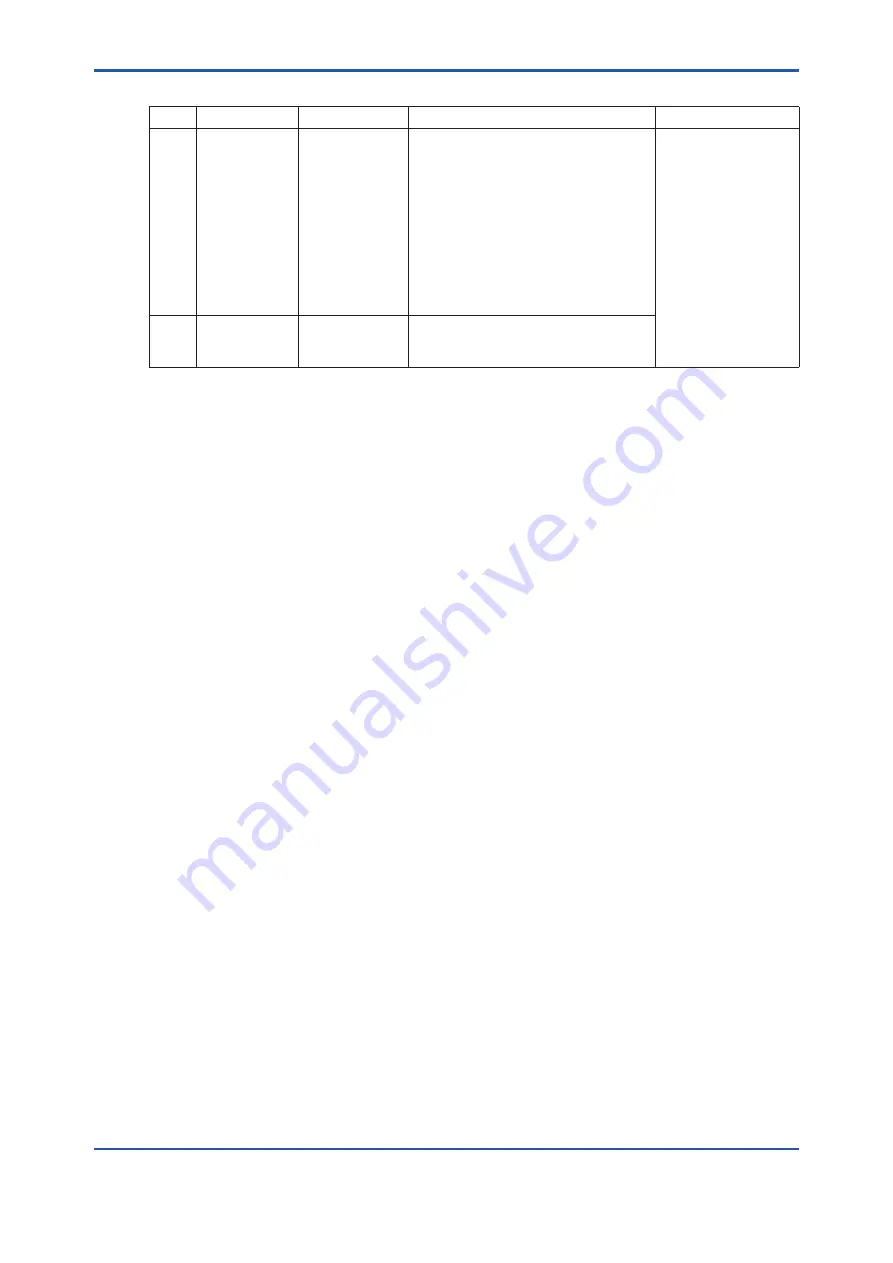
<6. TROUBLESHOOTING>
6-3
IM 12E01A06-02E
Table 6.1
Error Code List (3/3)
No.
Error
Occurrence
Problem
Return
E351
Analog output
range setting
failure
During
parameter
setting in
RANGE mode or
CODE 30.
Either of:
(1) Zero point ≥ span point, or
(2) Span point - zero point < 20% of
span point or 0.20, whichever is greater
(for turbidity) or ( span point - zero point
< 5.00 (for color).
When automatic range is selected in
CODE 30, also possible:
(3) At each span point, Range A ≥ Range
B, or
(4) at each span point, Range B ≥
Range C
When [YES]/[NO] key
is pressed, error code
display disappears
and error is removed.
E352 Parameter
setting failure
During
parameter
setting
Value outside the setting range is set in
setting other than AO range setting.
Refer to the user’s manual IM 12E01A06-01E for details.
Summary of Contents for TB750G
Page 7: ...Blank Page ...
Page 29: ...Blank Page ...
Page 35: ...Blank Page ...
Page 37: ...Blank Page ...