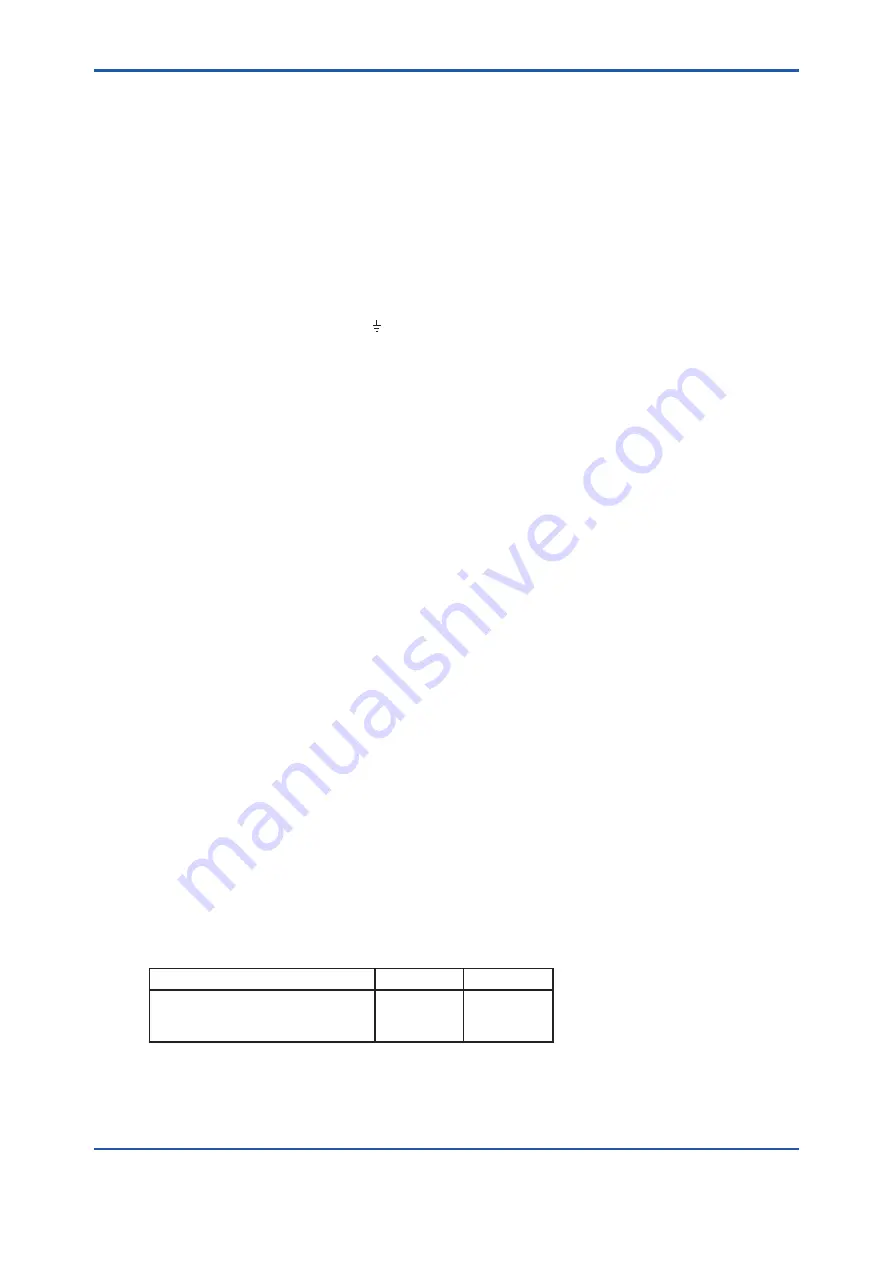
< 3. Installation, Piping and Wiring >
3-5
IM 12F5A1-01E
3.3.1 Power Cable and Grounding Wire
A power cable is used to feed power whose voltage and frequency meet the specifications for the
FC400G free available chlorine analyzer converter and a grounding wire to ground the converter
case.
For the power cable, use a two-core cable with a finished O.D. of 9 to 12 mm to connect the power
supply to converter terminals L1 and L2. The converter has no power switch; it is recommended that a
double-pole single-throw switch be installed in the power line.
Process the end of the cable to be connected to the converter as follows:
(1) Remove insulation covering from the cable for approx. 80 mm from the end of the cable.
(2) Connect crimp-on terminal lugs for M3 screws to the ends of the core conductors.
Install a grounding wire using the " " grounding terminal on the left bottom of the converter
case. The grounding terminal uses an M4 screw. Connect a grounding conductor that is has been
terminated is a lug (so that sufficient continuity is obtained) to this terminal to provide grounding
(grounding resistance of 100 Ω or less).
Note: If grounding using the converter case grounding terminal is difficult, connect the grounding wire
to terminal G (M3 screw) in the converter to make grounding on the power side. This requires
that a three-core or two-core shielded cable be used as a power/grounding cable.
3.3.2 Analog Output Signal Cable
An analog output signal cable is used to transmit an output signal of 1 to 5 V DC or 4 to 20 mA DC
corresponding to the output range to a receiver such as a recorder.
For analog output signals, use a two-core shielded cable with a finished O.D. of 9 to 12 mm.
Process the end of the cable to be connected to the converter as follows:
(1) Remove insulation covering and shield from the cable up to approx. 40 mm from the end of
the cable. Solder a lead wire to the root of the exposed shield and protect the soldered area by
wrapping with insulation tape.
(2) Cut the lead wire to the length of the core conductors and connect a crimp terminal lug for with
M3 screws to the end of this lead wire and the conductors.
(3) Connect the cable to the converter's ter and - the positive side conductor of the cable
must be connected to the " + " of the OUTPUT terminal and the negative side conductor to the "
- " of the OUTPUT. Also, connect the shield lead wire to terminal G.
(Do not attempt to ground the shield on the receiver side.)
3.3.3 Contact Output Cables
These cables are used to output <FAIL> and <MAINT> contact signals from the converter.
For contact output, use cables with a finished O.D. of 9 to 12 mm (select a two- or four-core cable
depending on the number of contact outputs to be used). The contact capacity of contact output relays
is as shown in Table 3.1. Devices to be connected must meet the conditions in Table 3.1.
Table 3.1
Contact Output Relay's Contact Capacity
For DC
For AC
Maximum allowable contact voltage
Maximum allowable contact current
Maximum allowable contact power
220 V
1 A
60 W
250 V
1 A
125 VA
Connect the core conductors of cables to terminals F1 and F2 (<FAIL,> contact output) and to
terminals M1 and M2 (<MAINT> contact output). Before connecting cables, process the ends of the
cables as follows: Remove approx. 40 mm of cable insulation covering from the end to be connected
to the converter and install a crimp terminal lug for an M3 screw on each conductor.
Summary of Contents for FC400G
Page 5: ...Blank Page ...
Page 9: ...Blank Page ...
Page 13: ...Blank Page ...
Page 21: ...Blank Page ...
Page 27: ...Blank Page ...
Page 49: ...Blank Page ...
Page 79: ...Blank Page ...
Page 87: ...Blank Page ...