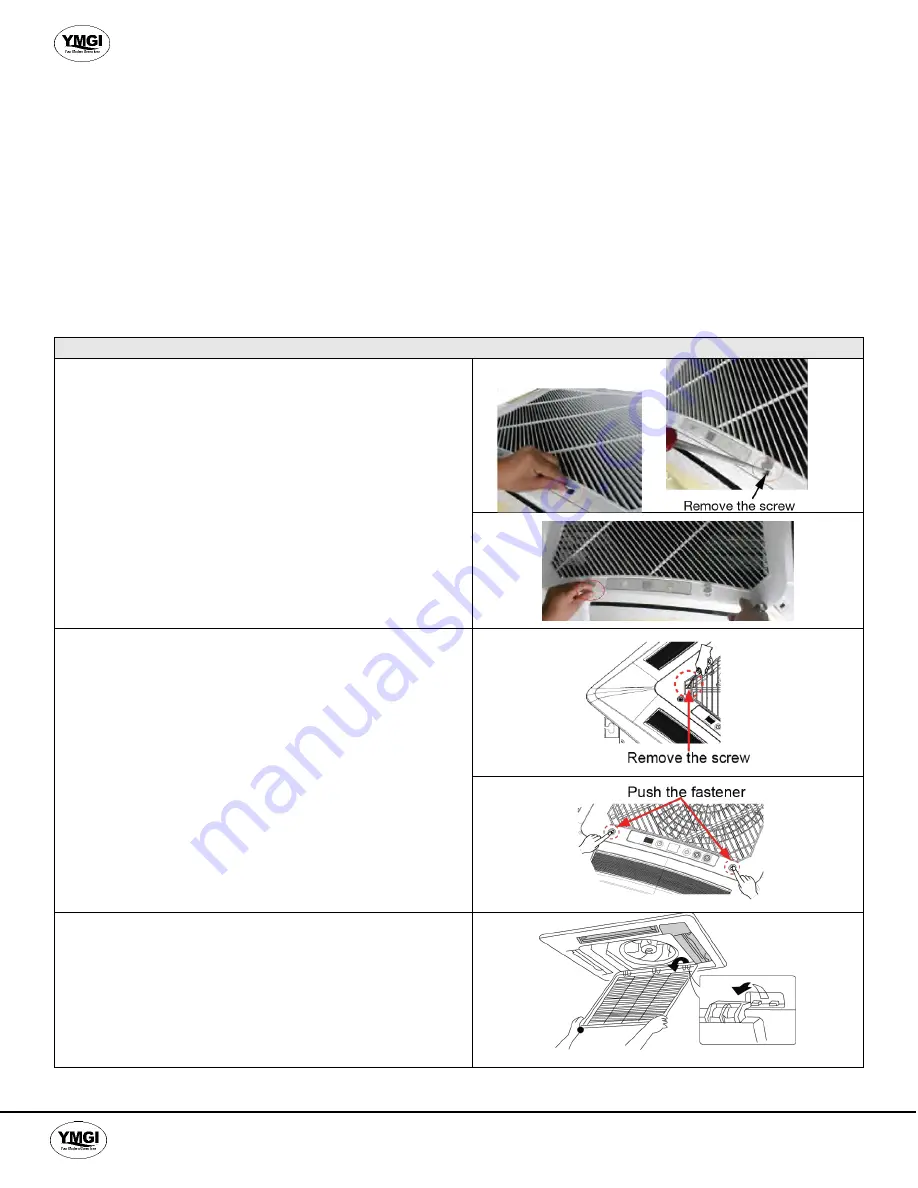
YMGI: Your Modern Green Idea
YMGI, Engineered Comfort Products for A Sustainable and Efficient Green World!
37
Routine Maintenance
Only qualified service persons should perform maintenance.
Before accessing to terminal devices, all power supply circuits should be disconnected.
Do not expose to water, or air that is 122°F (50°C) or warmer for cleaning air filters or outside panels.
Notes:
1. Do not operate the air conditioner with the filter uninstalled, otherwise dust would come into the unit.
2. Do not remove the air filter except for cleaning. Unnecessary handling may damage the filter.
3. Do not clean the unit with anything than contains: acetone, gasoline, benzene, thinner, polishing powder or liquid
insecticide. These can discolor and warp the unit.
4. Do not get components of the indoor unit wet. This can cause electric shock or fire hazard.
5. Increase the frequency of cleaning if the unit is installed in a room where the air is excessively dusty. (As a
general rule, we recommend cleaning the filters once every six months.
6. If dirt becomes impossible to clean, replace the air filter.
How to clean the air filter
1. Open the air inlet grille
How to open the panel grille of the
24k cassette type unit
a. Push the buckle as shown in the figure.
b. Remove the screws under buckles using a
screwdriver.
c. Push the fastener and open the panel grille
How to open the panel grille of the
12k / 18k cassette type unit
a. Remove the screws using a screwdriver as shown
in the illustration.
b. Push the two fasteners to open the panel grille.
2. Disassemble the air inlet grille
a. Open the air inlet grille at 45° angle, lift the pegs to
remove the grille.