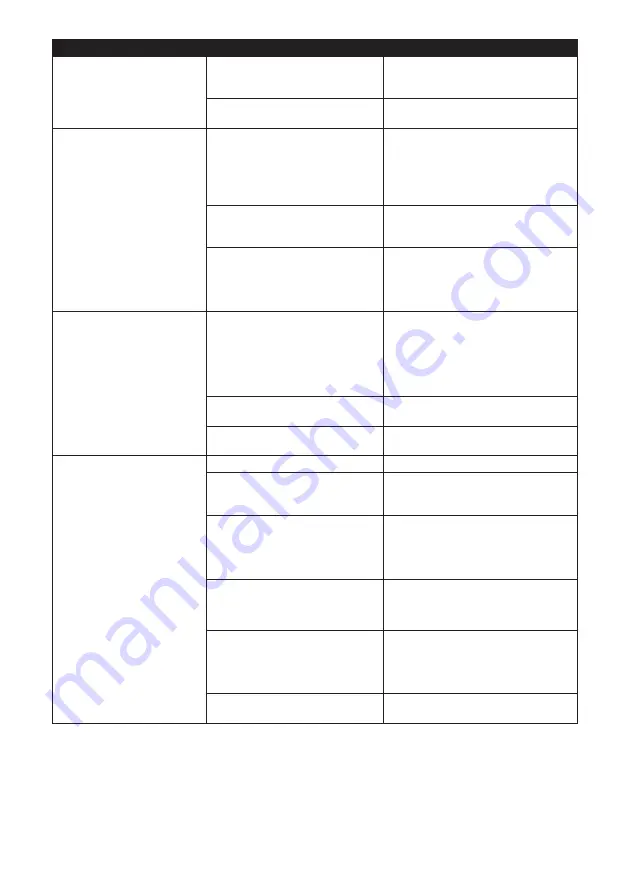
Use .023"(0.6mm) or .035"(0.9mm) contact
tip with the corresponding wire. Replace
contact tip if worn.
Have a qualified electrician verify the voltage
at your outlet. If the voltage is appropriate,
verify that the circuit wiring is sufficient for
the circuit breaker size.
Decrease stick-out (the amount the wire
extends past the contact tip).
Adjust welding parameters.
Use .023"(0.6mm)~.035"(0.9mm) wire. See
“Welding Wire Selection”, (page 14).
Reposition clamp and check cable to clamp
connection. Check connection of ground
cable, gun, and Wire Polarity Drive Lead.
Allow welder to cool at least 10 minutes with
machine ON (observe and maintain proper
duty cycle).
Check for obstructions blocking air flow and
ensure that there are 12 inches of clearance
between any obstacles and the vents on all
sides of the machine.
Make sure the machine is plugged in. Check
the status of your INPUT VOLTAGE
INDICATOR LED. It should be illuminated.
Check the voltage of your outlet. If it is 10%
more or less than optimal, call a qualified
electrician.
Turn the ON/OFF SWITCH to the ON
position.
Make sure the circuit breaker has been reset.
Exceeded duty cycle; thermal protector
engaged.
Insufficient air flow causing machine to
overheat before reaching duty cycle.
No voltage or incorrect voltage supplied
to welder.
ON/OFF SWITCH is in the OFF position.
Circuit breaker has been tripped.
Weld parameters too low.
Wrong type or size wire.
Poor ground connection or gun
connection.
Wrong size or worn contact tip.
Input power too low.
Stick-out too long.
Pull the trigger while in contact with the
workpiece. The machine does not arc unless
the trigger is pulled. Depress the trigger ALL
THE WAY until the trigger stops moving into
the gun.
Gun trigger is not being pulled or is not
making contact.
Adjust the drive pressure. See “Installing The
Welding Wire”, page 10.
Check if wire is in place and replace if
necessary.
No pressure on the drive roller;
insufficient or excessive pressure on the
drive roller.
Wire spool is empty.
Arc works but not feeding wire.
No arc or wire feed. Fan operates
normally (can be heard).
No arc or wire feed. Fan does
NOT operate (cannot be heard).
Low output or non-penetrating
weld.
PROBLEM
POSSIBLE CAUSE
POSSIBLE SOLUTION
- 21 -
Summary of Contents for MIG-205DS
Page 2: ......
Page 26: ...WIRING DIAGRAM 23...
Page 27: ......
Page 28: ...www yeswelder com WE ALWAYS STAND BEHIND IT Toll Free 855 937 4567...