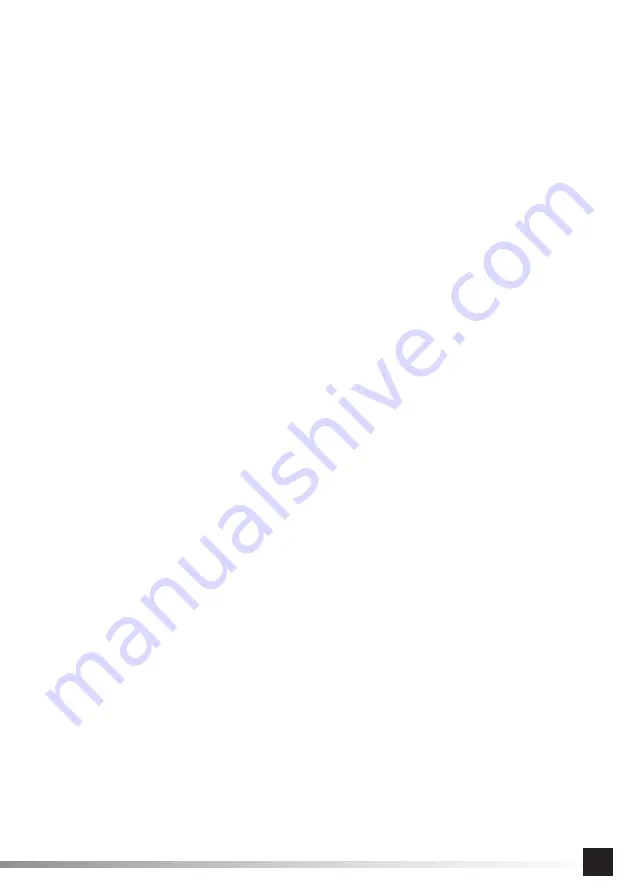
19
O R I G I N A L I N S T R U C T I O N S
GB
sharp edges or tamping tend to jam the rotating accessory in the material being processed and cause loss of control or kickback
towards the operator.
Never install chain saws, wood saws, diamond segmented discs with an edge clearance greater than 10 mm or circular
saws.
Such blades create frequent kickbacks and loss of control.
Never „jam” the disc or apply excessive pressure. Do not attempt to increase the cutting depth.
Excessive overload
increases the load and susceptibility to disc twisting or jamming in the saw cut and increases the probability of the disc kickback
or breaking apart.
If the disc is caught or cutting is interrupted for any reason, turn o
ff
the power tool and keep the cutting head stationary
until the disc stops completely. Never attempt to remove the cutting disc from the saw cut if the disc is in motion, other-
wise it may kick back.
Check and take appropriate action to eliminate the cause of pinching.
Do not restart cutting in the material being processed. Allow the blade to reach its full speed and carefully reinsert it
into the saw cut.
The disc can be seized, ejected or kicked back if the power tool is restarted in the material being processed.
Support any oversized material processed to minimise the risk of disc jamming or kickback.
Large processed materials
tend to bend under their own weight. The supports must be placed under the processed material close to the cutting line and close
to the edge of the material on both sides of the cutting line.
Take special care when cutting indentations in walls or other „blind” areas.
A protruding disc may cut through gas pipes or
water pipes, electric cables, or objects that may cause a kickback.
Never cut with the upper quarter of the cutting disc, especially do not start cutting in such a way.
Cutting with this area can
easily cause the tool to kick back towards the operator.
Do not allow plastics to melt when cutting.
Melted plastics stick to the cutting disc, which can lead to the tool kickback towards
the operator.
Safety warnings related to cuttings discs
Use only discs suitable for use with hand tools, discs for which the tool is not designed cannot be properly guarded and are not
safe. Do not use discs adapted only for stationary tools. Such discs have a less durable design as the disc is less exposed to
lateral tilting when cutting with stationary tools. Use of the disc intended for stationary tools in the manual cutter can cause it to fall
apart during operation, which can cause serious injury.
The guard must be securely attached to the tool and positioned for maximum safety so that the smallest possible area of the disc
is exposed towards the operator or the tool. This guard helps to protect the operator and the tool from broken disc fragments and
prevents accidental contact with the disc.
Inspect the cutting disc thoroughly before each use. Check the disc for signs of any damage. Pay particular attention to the cutting
edge. In the case of any damage, e.g. in the form, cracks, delaminations, defects. Check the shape of the disc for bending or any
imbalance, e.g. whether it rotates evenly. If any disc abnormalities are detected, do not use this disc in the product.
It is recommended to use diamond discs in the product in accordance with EN 13236.
If the disc has a speci
fi
ed direction of rotation, it must be mounted in such a way that the direction speci
fi
ed on the disc corre-
sponds to the direction of rotation of the spindle.
An acoustic inspection of the disc must be carried out prior to installation. While holding the disc in the air, gently hit it with a piece
of wood. If there is no audible noise, the disc is damaged and should not be used.
Do not overload the cutting disc, do not apply too much pressure during cutting. Do not cut into a mitre, the cutter is designed
only for work where the disc rotates vertically. Cutting should only be carried out in a straight line, the cutter is not designed for
cutting in curved lines. Failure to comply with the above recommendations may damage the disc during operation, and its debris
may cause serious injury.
The disc must be used as intended. For example, do not grind with a cutting disc. Discs for cutting are designed for use under
heavy pressure and the lateral forces applied to such a disc may cause it to fall apart.
Do not use wet cutting discs for dry cutting. Do not use water cooling for dry cutting discs only. Do not use any liquids other than
water for cooling. If the type of disc used allows for water cooling, they should always be used. This will reduce the amount of dust
generated during operation, as well as extend the life of the disc.
A diamond disc intended for dry cutting does not require water cooling, but its overload will lead to premature wear and may cause
damage, which may result in injury. It is recommended to remove the disc from the cut every 30 – 60 seconds and allow it to spin
for approx. 10 seconds. This will cool the disc.
Never cut asbestos or materials containing asbestos. Dust from cutting asbestos is particularly hazardous to health and has been
classi
fi
ed as a carcinogen.
Always use undamaged
fi
fl
anges, which are the correct size for the cutting disc. The correct
fi
fl
anges of the abrasive disc
reduce the possibility of damage to the cutting disc.
If the disc is equipped with spacers, use them during the installation of the discs. The thickness of the spacers must not exceed
0.5 mm.
Do not use worn discs from larger tools. A larger diameter disc is not suited for a higher rotational speed of smaller tools and may
break.
Always run up the disc to rated speed before cutting. Do not change the disc speed during cutting. Pay special attention when
restarting the cutting. Run up the disc to rated speed
fi
rst and then carefully insert the disc into the cutting slot.
If the disc is jammed in the material being cut, turn o
ff
the tool immediately and keep it still until the disc stops completely. Never
Summary of Contents for YT-82158
Page 32: ...32 RUS residual current device RCD...
Page 33: ...33 RUS...
Page 34: ...34 RUS 10...
Page 35: ...35 RUS EN 13236 30 60 10 0 5 XVIII XIX II III IV...
Page 36: ...36 RUS VI VII VIII X IX XI XII 80 XIII XIV TEST RESET TEST ON RESET 4 2 30...
Page 37: ...37 RUS X XV XVI XVII 30...
Page 38: ...38 RUS 0 3 XX XXI TOYA SA www toya pl...
Page 40: ...40 UA residual current device RCD...
Page 41: ...41 UA...
Page 42: ...42 UA 10...
Page 43: ...43 UA EN 13236 30 60 10 0 5 XVIII XIX II III IV V...
Page 44: ...44 UA VI VII VIII X IX XI XII 80 XIII XIV TEST RESET TEST ON RESET 4 2 30...
Page 45: ...45 UA X XV XVI XVII 30 0 3...
Page 46: ...46 UA XX XXI TOYA SA www toya pl...
Page 119: ...119 GR RCD RCD...
Page 120: ...120 GR...
Page 121: ...121 GR 10 mm...
Page 122: ...122 GR EN 13236 30 60 10 0 5 mm XVIII XIX...
Page 123: ...123 GR II III IV V VI VII VIII X IX XI XII 80 XIII XIV TEST RESET...
Page 124: ...124 GR TEST ON RESET 4 mm2 30 m X XV XVI XVII...
Page 125: ...125 GR 30 0 3 MPa XX XXI TOYA SA www toya pl...