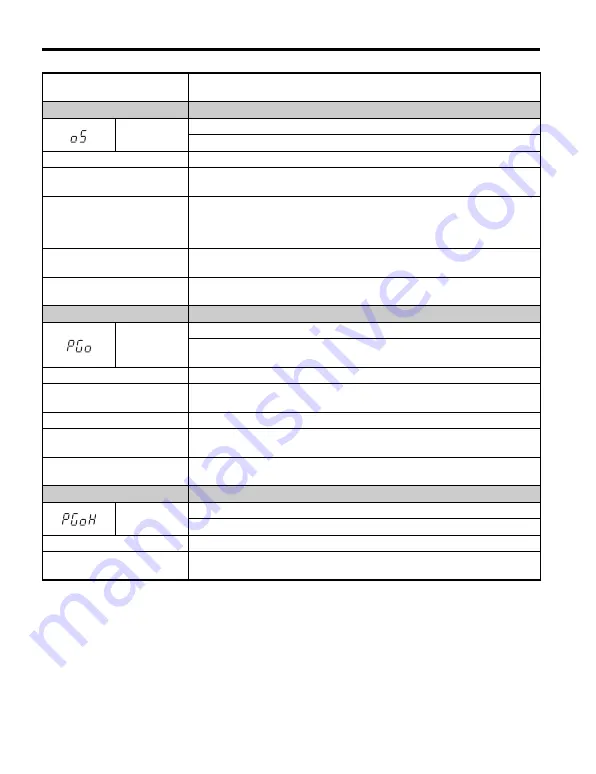
7 Troubleshooting
38
YASKAWA ELECTRIC
TOBP C730600 51F 1000-Series Option PG-F3 Installation Manual
PG-F3 power supply circuit is
damaged.
Replace the option.
Digital Operator Display
Fault Name
oS
Overspeed
The motor speed feedback exceeded the F1-08 setting.
Cause
Possible Solution
Overshoot is occurring.
Increase the settings for C5-01 (Speed Control Proportional Gain 1) and reduce
C5-02 (Speed Control Integral Time 1).
Incorrect speed feedback scaling
when terminal RP is used as
speed feedback input in V/f
control.
• Set H6-02 to the value of the speed feedback signal frequency when the motor
runs at the maximum speed.
• Adjust the input signal using parameters H6-03 through H6-05.
Incorrect PG encoder pulse
number set.
Check and correct parameter F1-01.
Inappropriate parameter settings.
Check the setting for the overspeed detection level and the overspeed detection
time (F1-08 and F1-09).
Digital Operator Display
Fault Name
PGo
PG Encoder Disconnected
Detected when no PG encoder pulses have been received for a time longer than is
set to F1-14.
Cause
Possible Solution
PG encoder cable is
disconnected.
Reconnect the cable.
PG encoder wiring is incorrect.
Correct the wiring.
PG encoder does not have
enough power.
Make sure the correct power supply is properly connected to the PG encoder.
Brake control sequence is
incorrect.
Correct the brake control sequence and verify that the brake has been released.
Digital Operator Display
Fault Name
PGoH
PG Encoder Hardware Fault
PG encoder cable is disconnected.
Cause
Possible Solution
PG encoder cable is
disconnected.
Reconnect the cable.