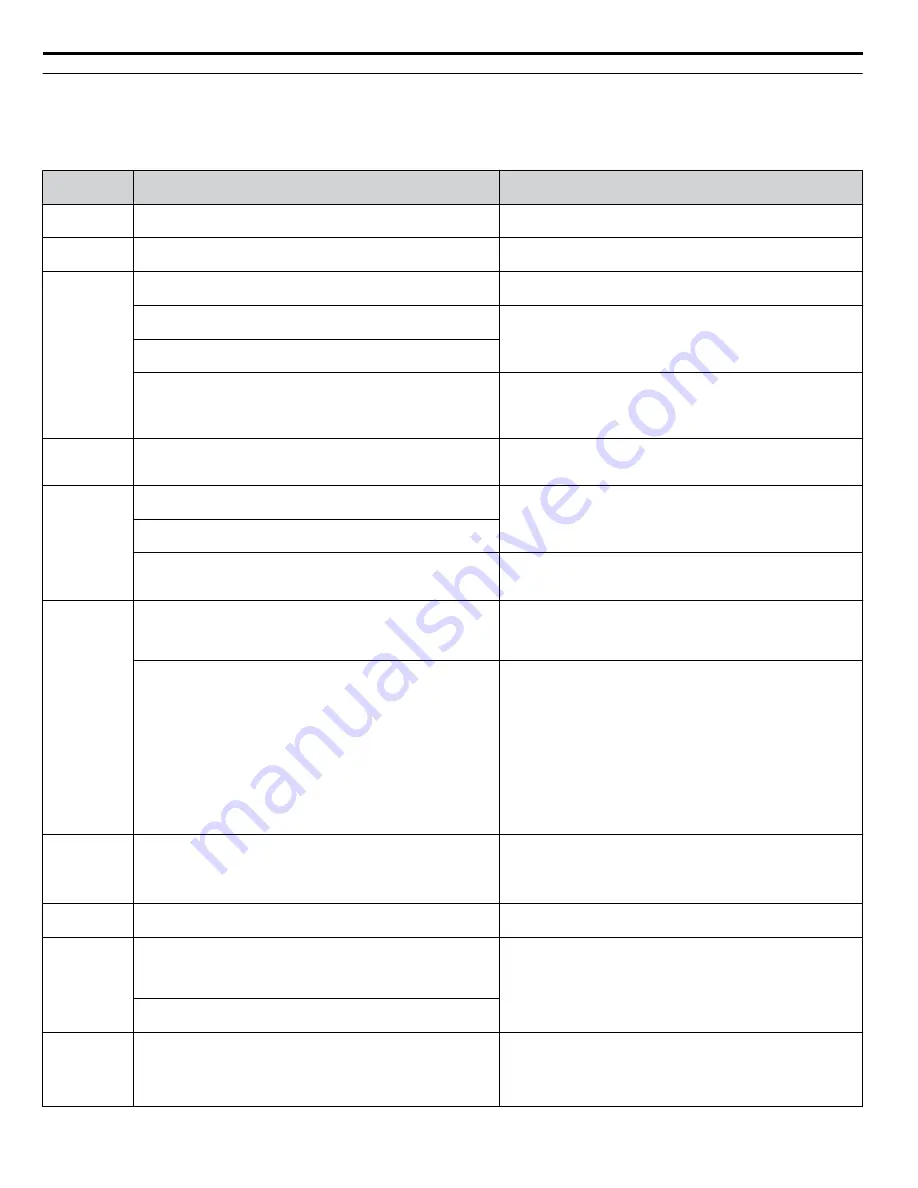
u
Operator Programing Errors
An Operator Programming Error (oPE) occurs when an inapplicable parameter is set or an individual parameter setting is
inappropriate. When an oPE error is displayed, press the ENTER button to display U1-18 (oPE fault constant) and show the
parameter causing the oPE error.
Digital
Operator
Cause
Possible Solution
oPE01
The drive model selection (o2-04) and the actual capacity of the
drive are not the same.
Correct the value set to o2-04.
oPE02
Parameters were set outside the possible setting range.
Use U1-18 to find parameters set outside the range. and set
parameters to the proper values.
oPE03
A contradictory setting is assigned to multi-function contact inputs
H1-01 to H1-08 (Excludes “Not used” and “External Fault.”)
Ensure all multi-function inputs are assigned to different functions.
The Up command was set but the Down command was not, or vice
versa (settings 10 vs. 11).
Properly set the functions that required for use in combination with
other functions.
The Up 2 command was set but the Down 2 command was not, or
vice versa (settings 75 vs. 76).
• Run/Stop command for a 2-wire sequence was set (H1-
oo
=
42), but Forward/Reverse command (H1-
oo
= 43) was not.
• “Drive Enable” is set to multi-function input S1 or S2 (H1-01 =
6A or H1-02 = 6A).
Properly set the functions that required for use in combination with
other functions.
oPE04
The drive, control board, or terminal board have been replaced and
the parameter settings between the control board and the terminal
board no longer match.
Set A1-03 to 5550 to load the parameter settings stored in the
terminal board to the drive. Initialize parameters after drive
replacement by setting A1-03 to 1110 or 2220.
oPE05
Frequency reference is assigned to an option card (b1-01 = 3) and
an input option card is not connected to the drive.
Reconnect the input option card to the drive.
The Run command is assigned to an option card (b1-02 = 3) and an
input option card is not connected to the drive.
Frequency reference is assigned to the pulse train input (b1-01 = 4)
and terminal RP is not set for frequency reference input (H6-01 >
0)
Set H6-01 to 0.
oPE07
At least two analog input terminals are set to the same function (i.e.,
at least two of these parameters have the same setting: H3-02,
H3-10, or H3-06).
Change the settings to H3-02, H3-10, and H3-06 so that functions
no longer conflict.
Note:
Both 0 (Frequency Reference Bias) and F (Not Used) can be
set to H3-02, H3-10, or H3-06 simultaneously.
The following simultaneous contradictory settings:
• H3-02, H3-10, or H3-06 = B (PID Feedback) while H6-01
(Pulse Train Input) = 1 (PID Feedback)
• H3-02, H3-10, or H3-06 = C (PID Target Value) while H6-01 =
2
(pulse train input sets the PID target value)
• H3-02, H3-10, or H3-06 = C (PID Target Value) while b5-18 =
1
(enables b5-19 as the target PID value)
• H6-01 = 2 (PID target) while b5-18 = 1
(enables b5-19 as the target PID value)
Disable one of the PID selections.
oPE09
The following simultaneous contradictory settings have occurred:
• b5-15 is not set to 0.0 (PID Sleep Function Operation Level)
• The stopping method is set to either DC Injection Braking or coast
to stop with a timer (b1-03 = 2 or 3).
• Set b5-15 to a value other than 0.0.
• Set the stopping method to coast to stop or ramp to stop (b1-03
= 0 or 1).
oPE10
V/f pattern setting error.
E1-09
≤
E1-07 < E1-06
≤
E1-11
≤
E1-04
Correct the settings for E1-04, E1-06, E1-07, E1-09, and E1-11.
oPE11
The following simultaneous contradictory settings have occurred:
C6-05 > 6 and C6-04 > C6-03 (carrier frequency lower limit is
greater than the upper limit).
If C6-05
≤
6, the drive operates at C6-03.
Correct the parameter settings.
The upper and lower limits between C6-02 and C6-05 are
contradictory.
oPE28
• S2-01 > S2-02
• S2-06 > S2-07
• S2-11 > S2-12
• S2-16 > S2-17
Correct the parameter settings.
i.7 Troubleshooting
58
YASKAWA ELECTRIC TOEP YAIP1U 03B YASKAWA AC Drive – P1000 Safety Precautions
Summary of Contents for P1000
Page 73: ......