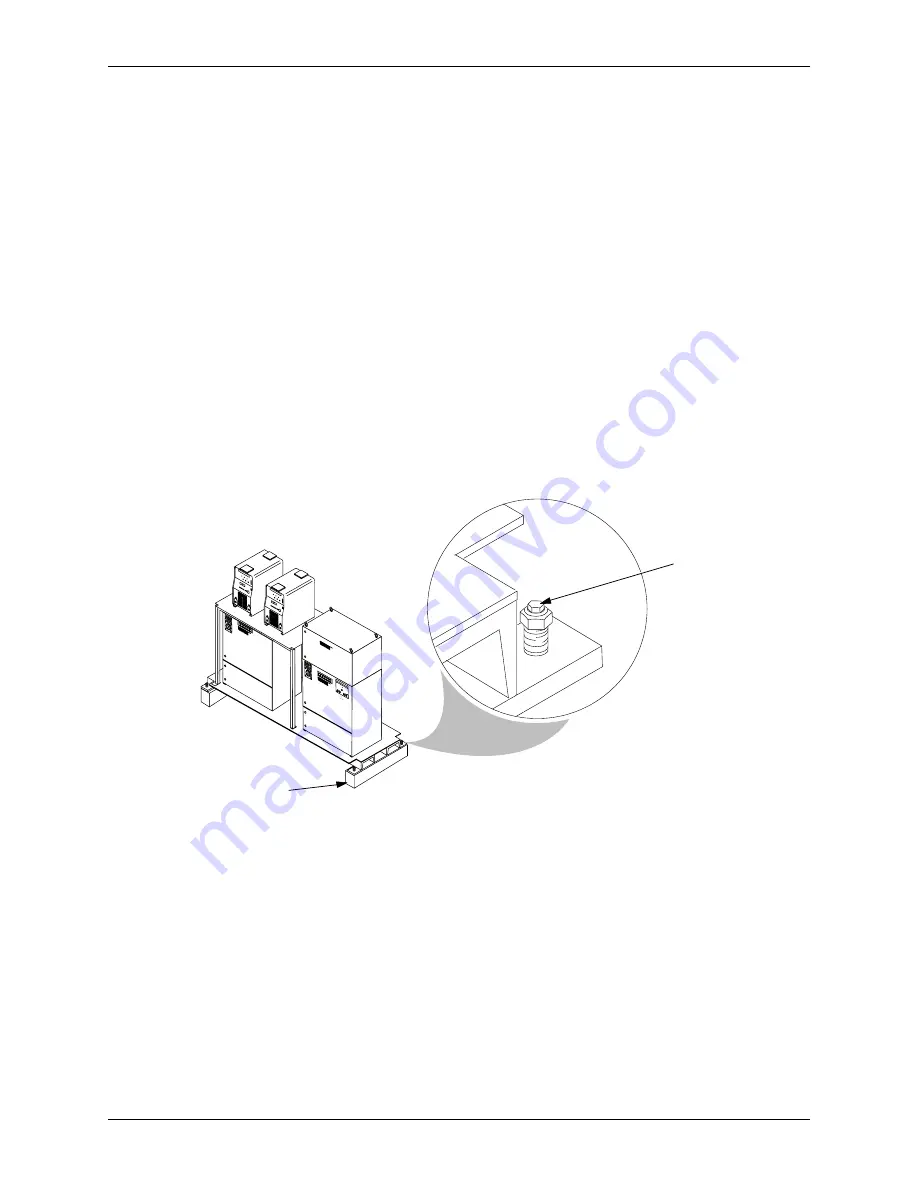
INSTALLATION
MOTO
MAN
4-11
ArcWorld IV-6200 XHD DR2C System Manual
6. Insert a 1/2-inch concrete drill bit through the center of each leveling bolt
(see Figure 4-3) and drill holes (at least four inches deep into concrete) for
anchors.
7. Vacuum concrete dust from holes.
8. Prepare a 1/2-inch anchor (factory-supplied) with accompanying washer and
nut (see Figure 4-4) for each anchored location.
9. Using a hammer, drive an anchor into each drilled hole until the washer stops
at the leveling bolt.
10. Using a 3/4-inch wrench, tighten the nut (clockwise) on each anchor until
tight.
4.9
Installing the Auxiliary Equipment Common Base
The auxiliary equipment common (AEC) base contains two controllers, two
welders, and four service disconnects. The common base may also contain
optional water circulators and Com-Arc seam tracking units. The auxiliary
equipment common base is shipped on wood blocks. To install the AEC base,
proceed as follows:
1. Unbolt the AEC base by removing four shipping bolts using a 3/4-inch
[
Figure 4-11 Unbolting Auxiliary Equipment Common (AEC) Base
SHIPPING BOLT
ON
OP
E
N
/
R
O
F
F
ON
OP
E
N
/
R
O
F
F
SE
RV
O
ON
RE
AD
Y
RE
MO
TE
(O
FF
)
(O
N)
ED
IT
L
OC
K
AL
AR
M
HO
LD
ST
AR
T
WOOD
BLOCK