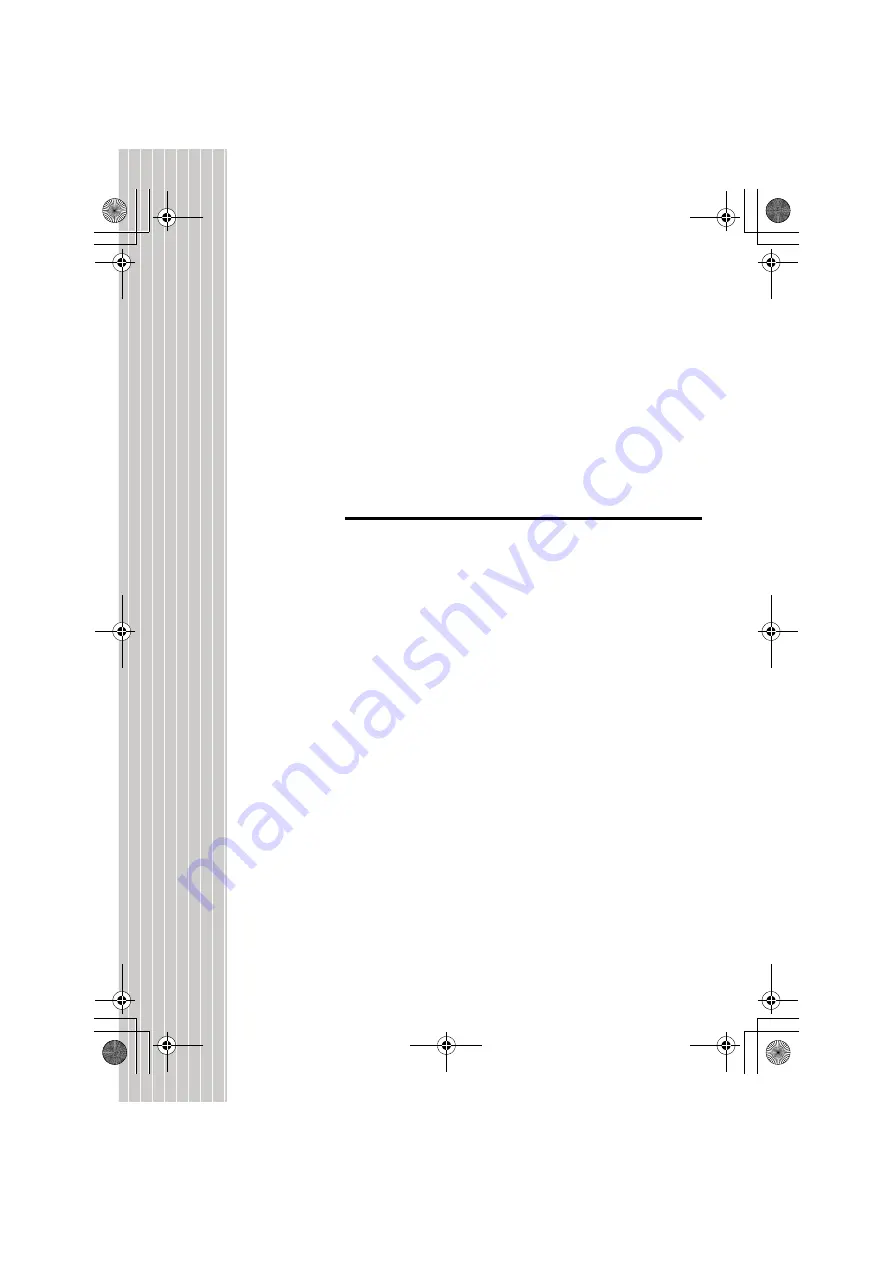
YASKAWA ELECTRIC
TOBP C730600 63C V1000 Option SI-ET3/V Installation Manual
3
Table of Contents
1 PREFACE AND SAFETY . . . . . . . . . . . . . . . . . . . . . . . . . . . 4
2 OVERVIEW . . . . . . . . . . . . . . . . . . . . . . . . . . . . . . . . . . . . . 10
3 RECEIVING. . . . . . . . . . . . . . . . . . . . . . . . . . . . . . . . . . . . . 11
4 OPTION COMPONENTS . . . . . . . . . . . . . . . . . . . . . . . . . . 12
5 INSTALLATION PROCEDURE . . . . . . . . . . . . . . . . . . . . . 16
6 RELATED DRIVE PARAMETERS . . . . . . . . . . . . . . . . . . . 31
7 TROUBLESHOOTING . . . . . . . . . . . . . . . . . . . . . . . . . . . . 33
8 EUROPEAN STANDARDS. . . . . . . . . . . . . . . . . . . . . . . . . 37
9 SPECIFICATIONS . . . . . . . . . . . . . . . . . . . . . . . . . . . . . . . 39
GEM_M-III_IM_E_conditional.fm 3 ページ 2017年7月7日 金曜日 午後5時9分