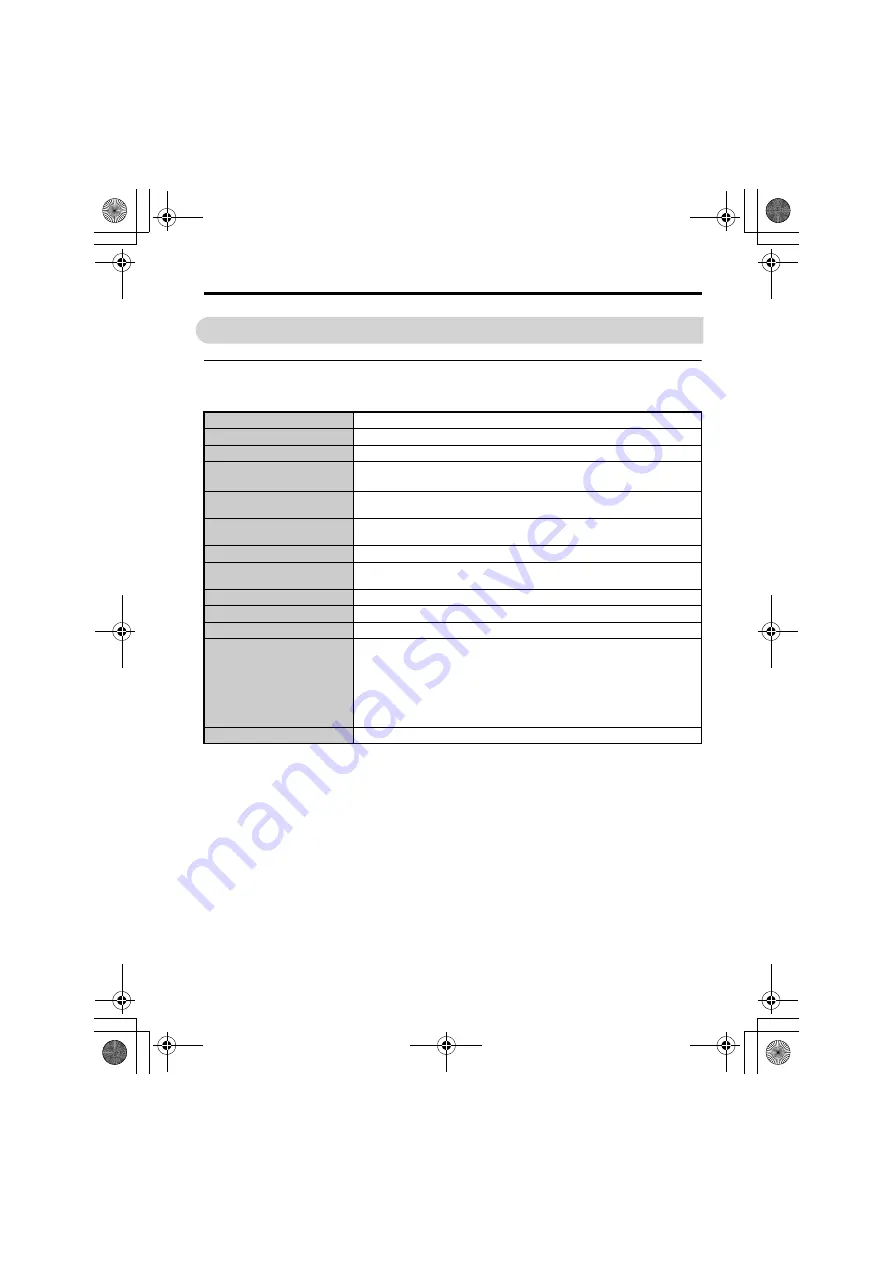
YASKAWA ELECTRIC
TOBP C730600 86F YASKAWA AC Drive Option SI-T3 Installation Manual
43
9 Specifications
9
Specifications
u
Specifications
Table 8 Option Specifications
Model
<1> For MECHATROLINK-I, a cycle is 2 ms. For MECHATROLINK-II, a cycle is 1 ms to 8 ms for a 32-byte data
transmission, and 500
μ
s to 8 ms for a 17-byte data transmission.
<2> For MECHATROLINK-I, a cycle is 2 ms.
<3> At the maximum transmission distance of 50 m (1969.0 in), the maximum number of stations is 15.
<4> For MECHATROLINK-I, only a 17-byte data transmission can be selected.
<5> The maximum number of connectable slave stations changes depending on the types and settings of the host
master, baud rate, or communications cycle. For details, refer to the manuals of your master.
Communications cycle: Integral multiple of transmission cycles (depending on the host master settings).
SI-T3
Access mode
Start-stop synchronization, master/slave method
Communication Speed
10 Mbps (MECHATROLINK-II), 4 Mbps (MECHATROLINK-I)
Transmission cycle
When installed to drives: 500
μ
s to 8 ms
When installed to energy-saving unit: 250
μ
s to 8 ms
Maximum transmission
distance
50 m (1969.0 in)
Minimum wiring distance
between stations
0.5 m (19.7 in)
Data length
17-byte data transmission or 32-byte data transmission
Maximum number of slave
stations
Ambient Temperature
-10
°
C to +50
°
C (14
°
F to 122
°
F)
Humidity
up to 95% RH (no condensation)
Storage Temperature
-20
°
C to +60
°
C (-4
°
F to 140
°
F) (allowed for short-term transport of the product)
Area of Use
Indoors and free from:
• Oil mist, corrosive gas, flammable gas, and dust
• Radioactive materials or flammable materials, including wood
• Harmful gas or fluids
• Salt
• Direct sunlight
• Falling foreign objects
Altitude
Up to 1000 m (3280 ft)
TOBP_C730600_86F_7_0_E.fm 43 ページ 2018年12月20日 木曜日 午後6時16分