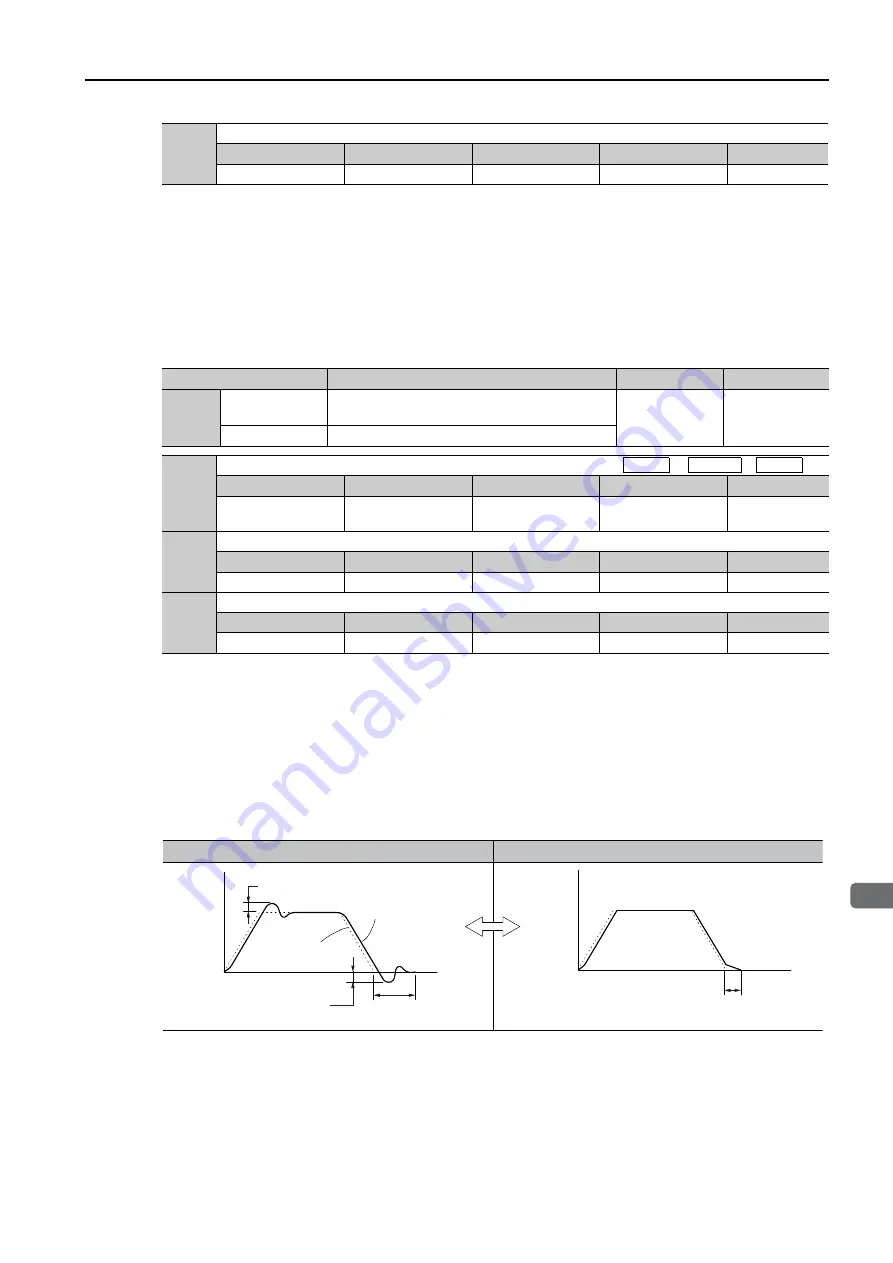
8.12 Manual Tuning
8.12.2 Compatible Adjustment Functions
8-79
8
T
uning
Note: 1. Overshooting will occur if you set the torque feedforward too high. Set the optimum value while monitoring
the response.
2. You cannot use the torque feedforward function together with torque limiting with an analog voltage refer-
ence.
Speed Feedforward
You set the speed feedforward function with the position control option (Pn207 = n.
X
)
and the speed reference input gain (Pn300).
The default setting of Pn300 is 600. Therefore, if the speed feedforward value is
±
6 V, then it
will indicate the rated speed.
Note: Overshooting will occur if you set the feedforward too high. Set the optimum value while monitoring the
response.
Mode Switching (Changing between Proportional and PI
Control)
You can use mode switching to automatically change between proportional control and PI con-
trol.
Overshooting caused by acceleration and deceleration can be suppressed and the settling time
can be reduced by setting the switching condition and switching levels.
Pn426
Torque feedforward average movement time
Setting Range
Setting Unit
Default Setting
When Enabled
Classification
0 to 5,100
0.1 ms
0
Immediately
Setup
Parameter
Meaning
When Enabled
Classification
Pn207
n.
0
(default setting)
Do not use V-REF.
After restart
Setup
n.
1
Use V-REF as a speed feedback input.
Pn300
Speed Reference Input Gain
Setting Range
Setting Unit
Default Setting
When Enabled
Classification
150 to 3,000
0.01 V/Rated
motor speed
600
Immediately
Setup
Pn307
Speed Reference Filter Time Constant
Setting Range
Setting Unit
Default Setting
When Enabled
Classification
0 to 65,535
0.01 ms
40
Immediately
Setup
Pn30C
Speed Feedforward Average Movement Time
Setting Range
Setting Unit
Default Setting
When Enabled
Classification
0 to 5,100
0.1 ms
0
Immediately
Setup
Speed
Position
Torque
Without Mode
S
witching
With Mode
S
witching
Motor
s
peed
Over
s
hooting
Actual
S
ervomotor
operation
Reference
Time
S
ettling time
Over
s
hooting
Motor
s
peed
S
ettling time
Time