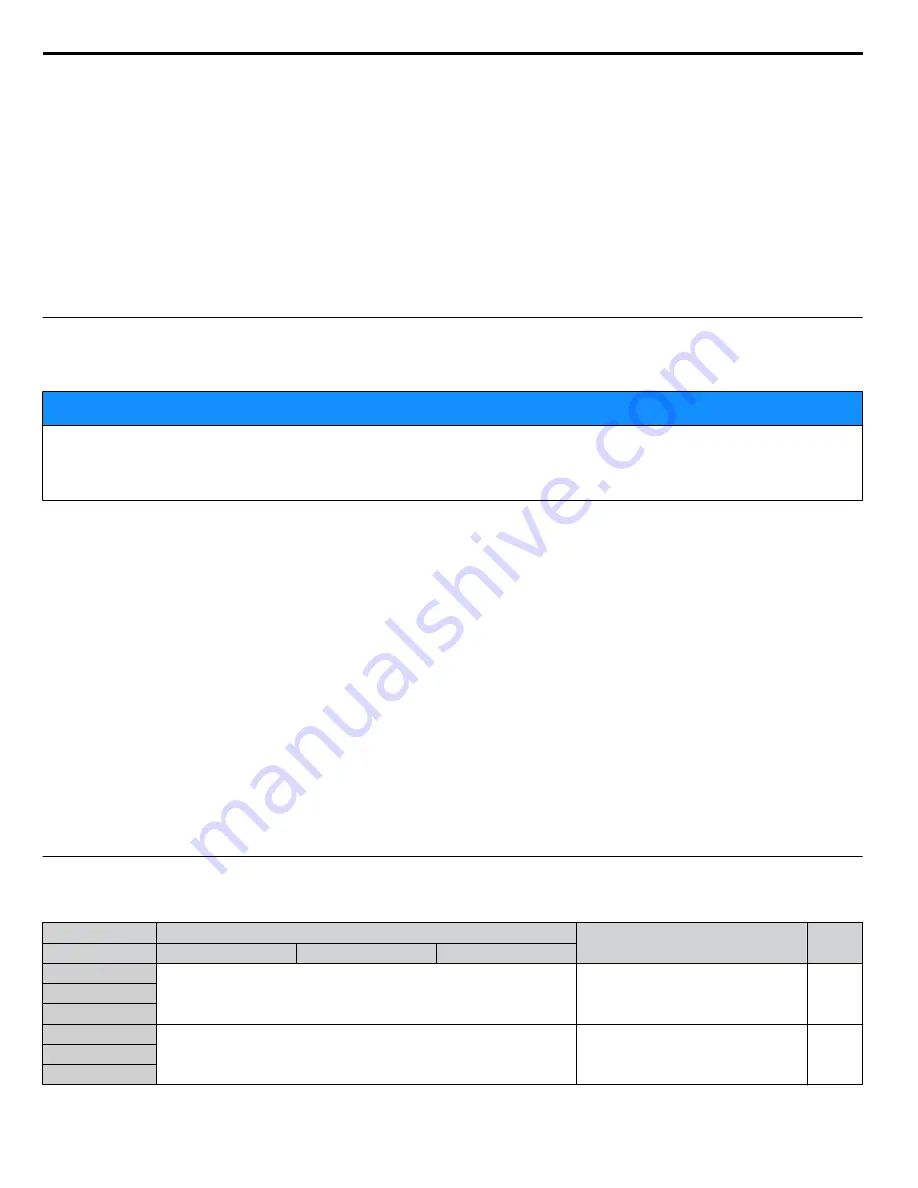
<4> This figure illustrates an example of a sequence input to S1 through S7 using a non-powered relay or an NPN transistor. Install
the wire link between terminals SC-SP for Sink mode, between SC-SN for Source mode, or leave the link out for external power
supply. Never short terminals SP and SN, as it will damage the drive.
<5> This voltage source supplies a maximum current of 150 mA.
<6> The maximum output current capacity for the +V terminal on the control circuit is 20 mA. Never short terV and AC, as
it can cause erroneous operation or damage the drive.
<7> Set jumper S1 to select between a voltage or current input signal to terminal A2. The default setting is for voltage input.
<8> Set DIP switch S2 to the ON position to enable the termination resistor in the last drive in a MEMOBUS/Modbus network.
<9> Monitor outputs work with devices such as analog frequency meters, ammeters, voltmeters, and wattmeters. They are not
intended for use as a feedback-type signal.
<10> Use jumper S5 to select between voltage or current output signals at terminals AM and FM. Set parameters H4-07 and H4-08
accordingly.
<11> Self-cooling motors do not require the same wiring necessary for motors with cooling fans.
u
Main Circuit Wiring
WARNING! Electrical Shock Hazard. Do not connect the AC power line to the drive output terminals U/T1, V/T2, and W/T3 . Failure to
comply could result in death or serious injury by fire as a result of drive damage from line voltage application to output terminals.
NOTICE
Refer to the Z1000 User Manual (600 V models) TOEPYAIZ1U03 for complete product instructions necessary for proper
installation, set-up, troubleshooting and maintenance.
To obtain instruction manuals for Yaskawa products access : http://www.yaskawa.com
NOTICE: Route motor leads U/T1, V/T2, and W/T3 separate from all other leads to reduce possible interference related issues. Failure to
comply may result in abnormal operation of drive and nearby equipment.
NOTICE: Do not use the negative DC bus terminal “–” as a ground terminal. This terminal is at high DC voltage potential. Improper wiring
connections could damage the drive.
NOTICE: Do not solder the ends of wire connections to the drive. Soldered wiring connections can loosen over time. Improper wiring practices
could result in drive malfunction due to loose terminal connections.
NOTICE: Do not switch the drive input to start or stop the motor. Frequently switching the drive on and off shortens the life of the DC bus
charge circuit and the DC bus capacitors, and can cause premature drive failures. For the full performance life, refrain from switching the
drive on and off more than once every 30 minutes.
NOTICE: When connecting the motor to the drive output terminals U/T1, V/T2, and W/T3, the phase order for the drive and motor should
match. Failure to comply with proper wiring practices may cause the motor to run in reverse if the phase order is backward.
NOTICE: Do not connect phase-advancing capacitors or LC/RC noise filters to the output circuits. Failure to comply could result in damage
to the drive, phase-advancing capacitors, LC/RC noise filters or ground fault circuit interrupters.
Note:
Wire gauge recommendations based on drive continuous current ratings (ND) using 75 °C 600 Vac vinyl-sheathed wire assuming ambient
temperature within 40 °C and wiring distance less than 100 m.
Yaskawa recommends using closed-loop crimp terminals on all drive models. To maintain UL/cUL approval, UL Listed
closed-loop crimp terminals are specifically required when wiring the drive main circuit terminals on models 5A0041 to
5A0242. Use only the tools recommended by the terminal manufacturer for crimping.
u
Main Circuit Terminal Functions
Table i.3 Main Circuit Terminal Functions
Terminal
Type
Function
Page
Drive Model
5A0003 to 5A0032
5A0041, 5A0052
5A0062 to 5A0242
R/L1
Main circuit power supply input
Connects line power to the drive
17
S/L2
T/L3
U/T1
Drive output
Connects to the motor
17
V/T2
W/T3
i.4 Standard Connection Diagram
18
YASKAWA TOEP YAIZ1U 02B YASKAWA AC Drive – Z1000 Quick Start Guide