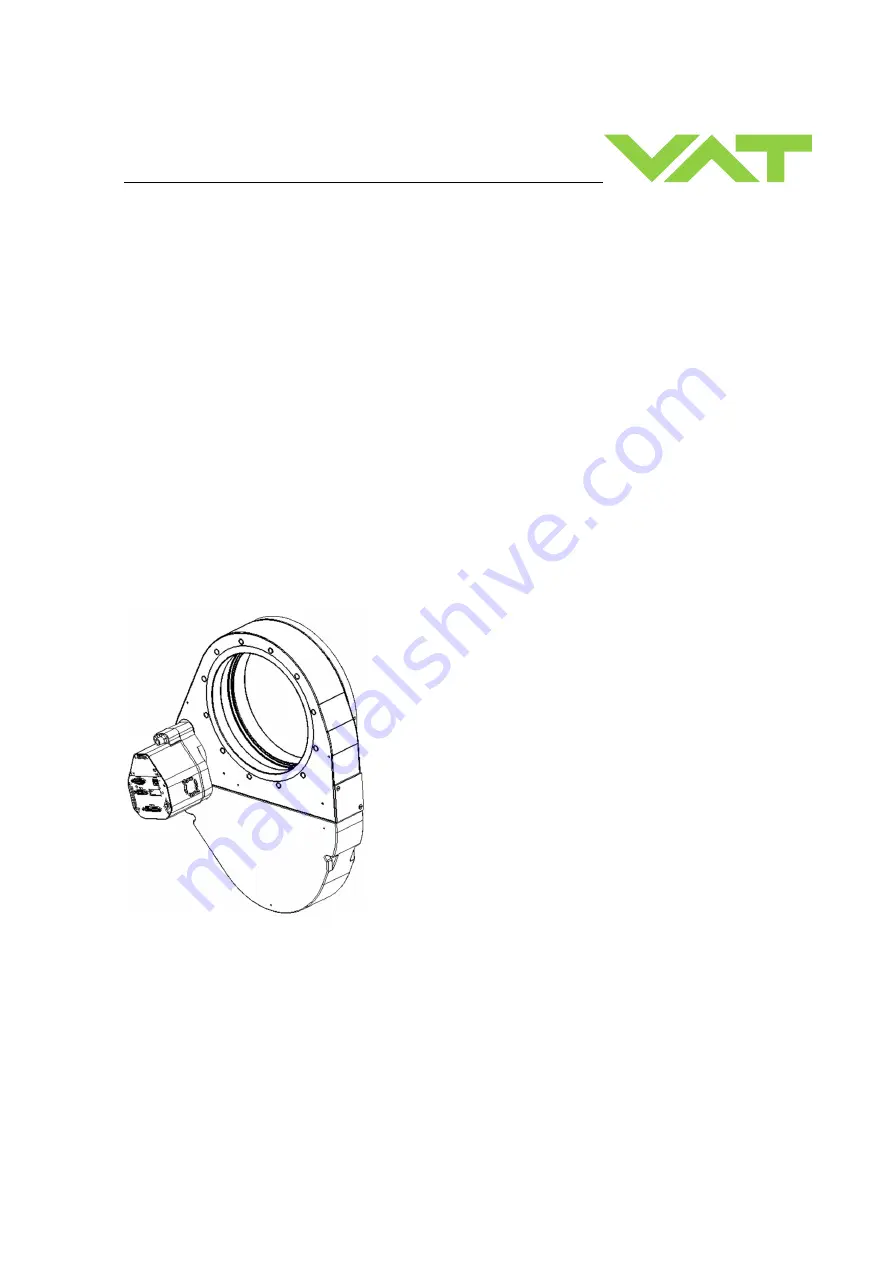
Installation, Operating &
Maintenance Instructions
980029EB
Edition 2019-10-11
Pendulum control & isolation valve
with Logic interface
Series 653
DN 100-250 mm (I.D. 4“ - 10")
This manual is valid for the valve ordering number(s):
653 . . - . .GE - . . . .
(2 sensor inputs / analog outputs)
653 . . - . .AE - . . . .
(2 sensor inputs / analog outputs /
±
15V SPS)
653 . . - . .HE - . . . .
(2 sensor inputs / analog outputs / PFO)
653 . . - . .CE - . . . .
(2 sensor inputs / analog outputs /
±
15V SPS / PFO)
SPS = Sensor Power Supply
PFO = Power Failure Option
configured with firmware : F01.0C.28.xx
Sample picture