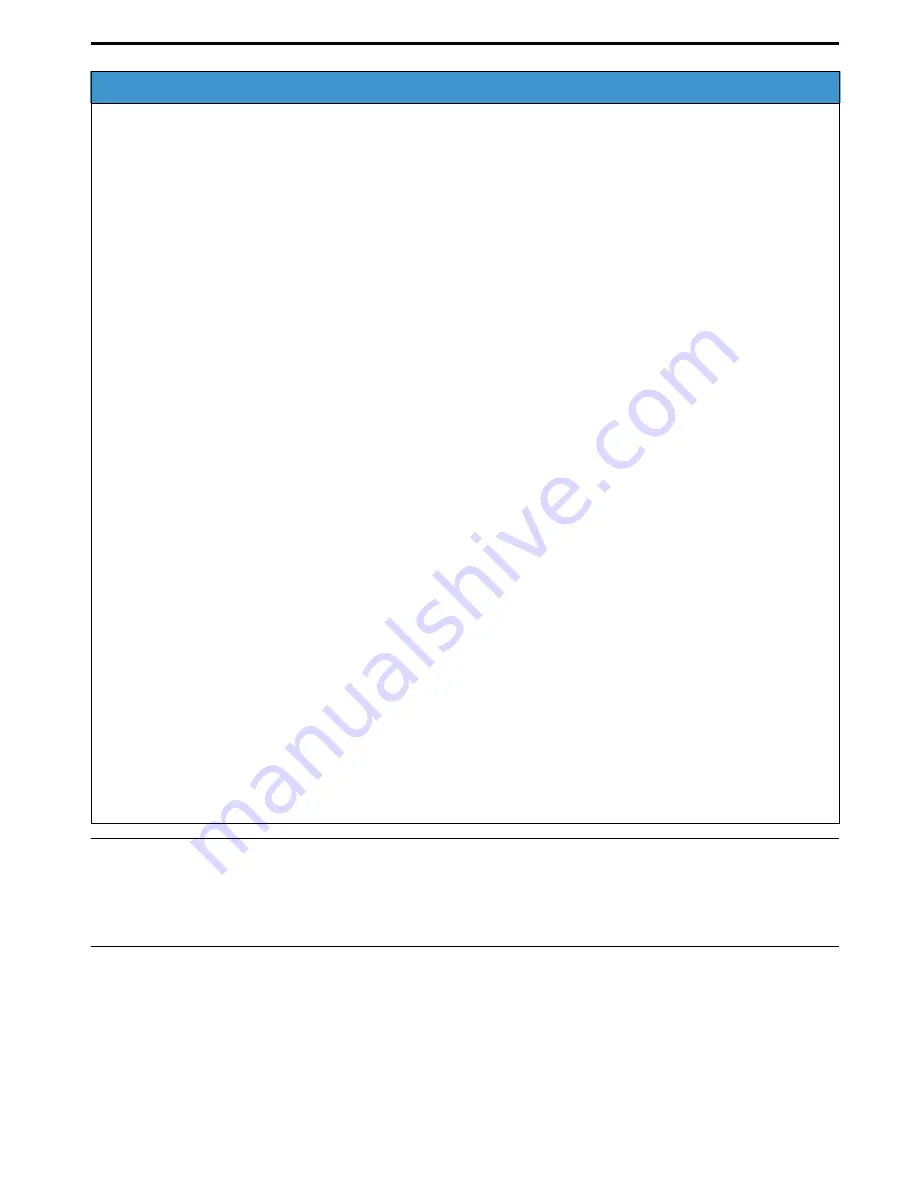
1 General Information and Safety Instructions
YASKAWA Europe
TOEP C710606 75B - AC Drive V1000 IP66 - Quick Start Guide
EN 7
Precautions for CE Low Voltage Directive Compliance
This drive has been tested according to European standard EN61800-5-1, and it fully complies with the Low Voltage Directive. The following
conditions must be met to maintain compliance when combining this drive with other devices:
Do not use drives in areas with pollution higher than severity 2 and over voltage category 3 in accordance with IEC664.
Ground the neutral point of the main power supply for 400 V Class drives.
Precautions for Using the Inputs H1/H2-HC
Same as standard V1000 drives, this drive provides terminals H1/H2 and HC. In the V1000 IP66 drives, described here, these terminals can be used
to disable the drive output, but they can NOT be used to perform safe stop according to EN60204-1 (Function is in preparation. Contact your sales
representative or YASKAWA for details).
NOTICE
Equipment Hazard
Observe proper electrostatic discharge procedures (ESD) when handling the drive and circuit boards.
Failure to comply may result in ESD damage to the drive circuitry.
Never connect or disconnect the motor from the drive while the drive is outputting voltage.
Improper equipment sequencing could result in damage to the drive.
Do not perform a withstand voltage test on any part of the drive.
Failure to comply could result in damage to the sensitive devices within the drive.
Do not operate damaged equipment.
Failure to comply could result in further damage to the equipment.
Do not connect or operate any equipment with visible damage or missing parts.
Prevent moisture and other solvents from entering the drive enclosure.
Failing to do so can damage the drive or considerably shorten its expected performance life.
Install adequate branch circuit short circuit protection per applicable codes.
Failure to comply could result in damage to the drive.
The drive is suitable for circuits capable of delivering not more than 30,000 RMS symmetrical Amperes, 240 Vac maximum (200 V Class) and
480 Vac maximum (400V Class).
Do not use unshielded cable for control wiring.
Failure to comply may cause electrical interference resulting in poor system performance. Use shielded twisted-pair wires and ground the shield
to the ground terminal of the drive.
Do not allow unqualified personnel to use the product.
Failure to comply could result in damage to the drive or braking circuit.
Carefully review the braking option instruction manual when connecting a braking option to the drive.
Do not modify the drive circuitry.
Failure to comply could result in damage to the drive and will void warranty.
YASKAWA is not responsible for modification of the product made by the user. This product must not be modified.
Check all the wiring to ensure that all connections are correct after installing the drive and connecting other devices.
Failure to comply could result in damage to the drive.
Do not connect unapproved LC or RC interference suppression filters, capacitors, or overvoltage protection devices to the output of the
drive.
Using unapproved filters could result in damage to the drive or motor equipment.
Exchange the entire unit including the drive, case, and heatsink in the event that any single part becomes damaged.
The drive, enclosure, and heatsink are constructed as a single piece, and it is therefore not possible to simply return the drive separate from the
protective casing.