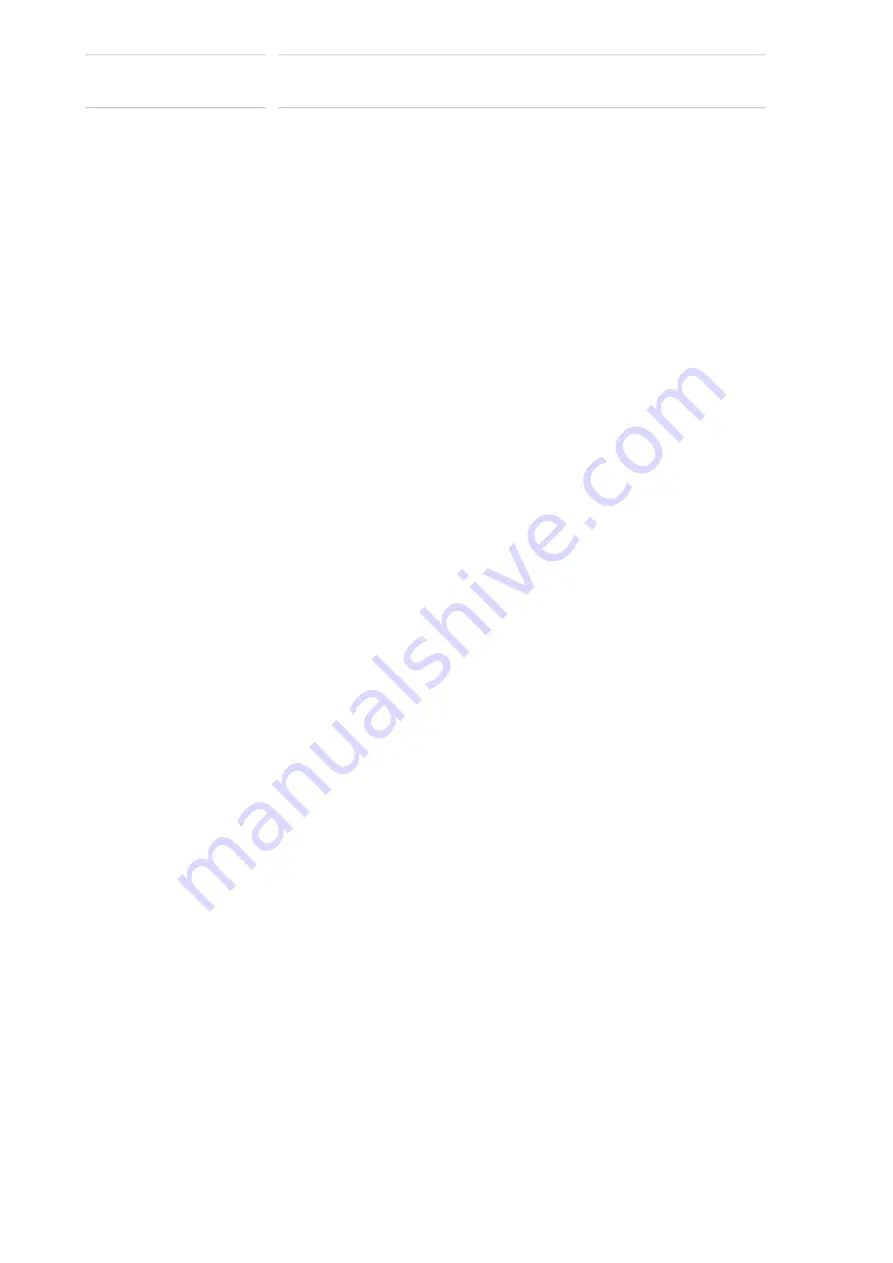
B-5
183574-1CD
183574-1CD
Appendix B
B.1 Glossary
ArcWorld 50/50S/52/52S
Collaborative Robot
Term used to describe a robot system designed to operate in one or more
of the four collaborative modes.
"Speed and Separation Monitoring"
"Power and Force Limiting (PFL)"
Command Interpreter
A module or set of modules that determines what the received command
means. The command is broken down into parts (parsed) and processed.
Command Position
The endpoint position of a robot motion that the Controller is trying to
achieve.
Compliance
Displacement of a Robot in response to a force or torque. A high
compliance means the Robot moves a good bit when it is stressed. This is
called spongy or springy. Low compliance would be a stiff system when
stressed.
Compliant Robot
A robot that performs tasks, with respect to external forces, by modifying
its motions in a manner that minimizes those forces. The indicated or
allowed motion is accomplished through lateral (horizontal), axial (vertical)
or rotational compliance.
Configuration
The arrangement of links created by a particular set of joint positions on
the robot. Note that there may be several configurations resulting in the
same endpoint position.
Contact Sensor
A device that detects the presence of an object or measures the amount
of applied force or torque applied on the object through physical contact
with it. Contact sensing can be used to determine location, identity, and
orientation of work pieces.
Continuous Path
Describes the process where by a robot is controlled over the entire path
traversed, as opposed to a point-to-point method of traversal. This is used
when the trajectory of the end-effector is most important to provide a
smooth movement, such as in spray painting etc. See
Control Algorithm
A monitor used to detect trajectory deviations in which sensors detect
such deviations and torque applications are computed for the actuators.
Control Command
An instruction fed to the robot by means of the human-to-machine input
device. See Pendant (Teaching). This command is received by the
Controller system and is interpreted. Then, the proper instruction is fed to
the robot's actuators, which enable it to react to the initial command. Many
times, the command must be interpreted with the use of logic units and
specific algorithms. See
.
102 of 126