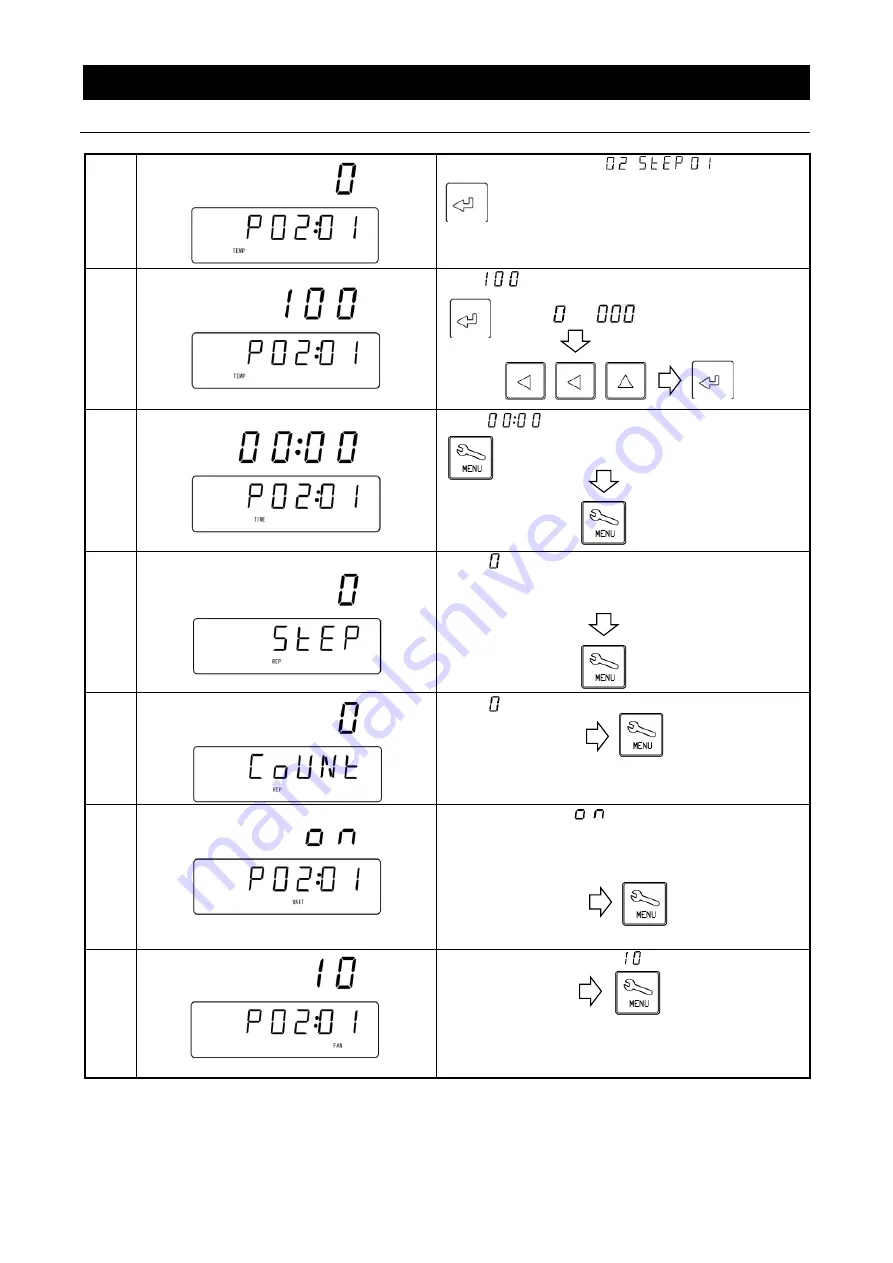
30
4
.
OPERATION PROCEDURE
Programming Procedure
1-2
Enter program pattern
,
.
- TEMP flashes in bottom left of lower
display.
1-3
Enter (°C).
-
Last “ ” in “
” flashes.
1-4
Enter “ ” (0 hours and 0 minutes - default).
- TIME flashes in bottom left of lower
display.
1-5
Enter “ ” (no repeat destination - default).
REP flashes in bottom left of lower display.
1-6
Enter “ ” (no repeats - default).
REP lamp flashes.
1-7
Turn wait function “ ”.
(
“waits” until chamber temp is within -3°C ~ +6°C of
temp setting before beginning time countdown -
default).
WAIT lamp flashes.
1-8
Set variable fan speed to “ ” (Max - default)
FAN lamp flashes.