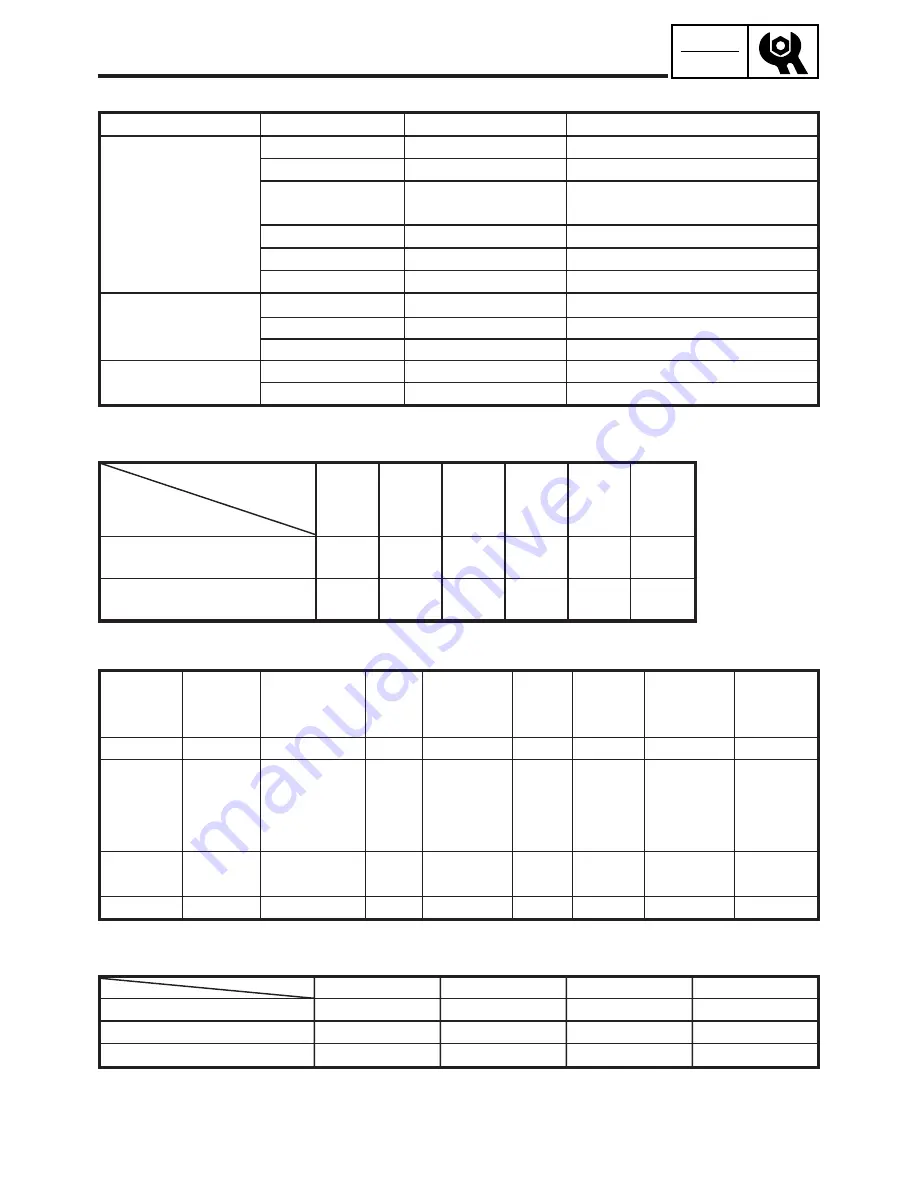
2-54
INSP
ADJ
Ó
Outside
diameter
mm (in)
69.5 (2.736)
69.5 (2.736)
69.5 (2.736)
69.5 (2.736)
Ì
Free
length
mm (in)
75 (2.95)
75 (2.95)
75 (2.95)
75 (2.95)
Ï
No. of
coils
5.19
5.53
5.53
4.86
‰
Wire
gauge
mm (in)
5.0 (0.196)
5.3 (0.209)
5.5 (0.217)
5.5 (0.217)
Î
Color
Brown
Red
Green
Silver
Ç
Spring rate
(compression)
N/mm (kg/mm) (lb/in)
6.2 (0.63), 35.28
7.3 (0.74), 41.44
8.5 (0.87), 48.72
10.21 (1.04), 58.24
ı
Spring rate
(torsion)
N·mm/rad
(kg·mm/rad)
6003 (613)
7147 (729)
8314 (848)
9460 (965)
18 teeth
19 teeth
20 teeth
21 teeth
22 teeth
23 teeth
39 teeth
39 teeth
40 teeth
68 links
70 links
89J-17682-80
89J-17682-91
89J-17682-00
89J-17682-10
89J-17682-20
89J-17682-30
8CW-47587-90
89J-47587-90
89J-47587-00
94860-02068
94860-02070
GEAR SELECTION
1
Chain and sprocket part number
Å
Part name
‰
Drive sprocket
Ï
Driven sprocket
Ì
Chain
ı
Teeth & links
Î
Standard
VT600 for Europe
MM600
SX600
VT600 for U.S.A./Canada
VX600ER
VX600ER/VT600
SX600/MM600
VX600ER/SX600/MM600/VT600
2
Gear ratio
39 teeth
40 teeth
Å
Drive sprocket
19 teeth 20 teeth 21 teeth 22 teeth 23 teeth
2.053
1.950
1.857
1.773
1.696
68 links 68 links 68 links 70 links 70 links
2.105
2.000
1.905
1.818
1.739
68 links 68 links 70 links 70 links 70 links
ı
Driven sprocket
3
Secondary sheave spring
Å
Part no.
90508-500B1
90508-536A9
90508-556A2
90508-556A7
4
Secondary spring twist angle
90508-500B1 (brown) / 90508-536A9 (red) / 90508-556A2 (green) / 90508-556A7 (silver)
0
3
6
9
1
10°
40°
70°
100°
2
20°
50°
80°
110°
3
30°
60°
90°
120°
ı
Sheave
Ç
Part no.
Å
Seat
È
Standard
18 teeth
2.167
68 links
2.222
68 links
VX600ER/
SX600/
MM600
VT600 for
U.S.A/Canada
VT600 for
Europe
Summary of Contents for MM600G
Page 1: ...VX600ERG SX600G MM600G VT600G SERVICE MANUAL LIT 12618 02 20 8EA 28197 10 981059 ...
Page 57: ...2 43 INSP ADJ CARBURETORTUNING Guide for carburetion SEA2720 ...
Page 79: ...2 65 INSP ADJ REAR SUSPENSION ...
Page 220: ...8 21 ELEC CHARGING SYSTEM ...
Page 236: ...8 37 ELEC SIGNAL SYSTEM ...
Page 266: ...9 20 SPEC GENERAL TORQUE SPECIFICATIONS DEFINITION OF UNITS ...
Page 267: ...SPEC 9 21 CABLE ROUTING SEA9010 ...
Page 269: ...SPEC 9 23 CABLE ROUTING SEA9010 ...
Page 271: ...SPEC 9 25 CABLE ROUTING SEA9020 ...
Page 273: ...SPEC 9 27 CABLE ROUTING SEA9030 ...
Page 275: ...SPEC 9 29 CABLE ROUTING SEA9030 ...
Page 277: ...SPEC 9 31 CABLE ROUTING SEA9040 ...
Page 279: ...SPEC 9 33 CABLE ROUTING SEA9050 ...
Page 281: ...SPEC 9 35 CABLE ROUTING SEA9050 ...
Page 283: ...SPEC 9 37 CABLE ROUTING SEA9060 ...
Page 287: ...Printed in USA E CR PRINTED ON RECYCLED PAPER ...