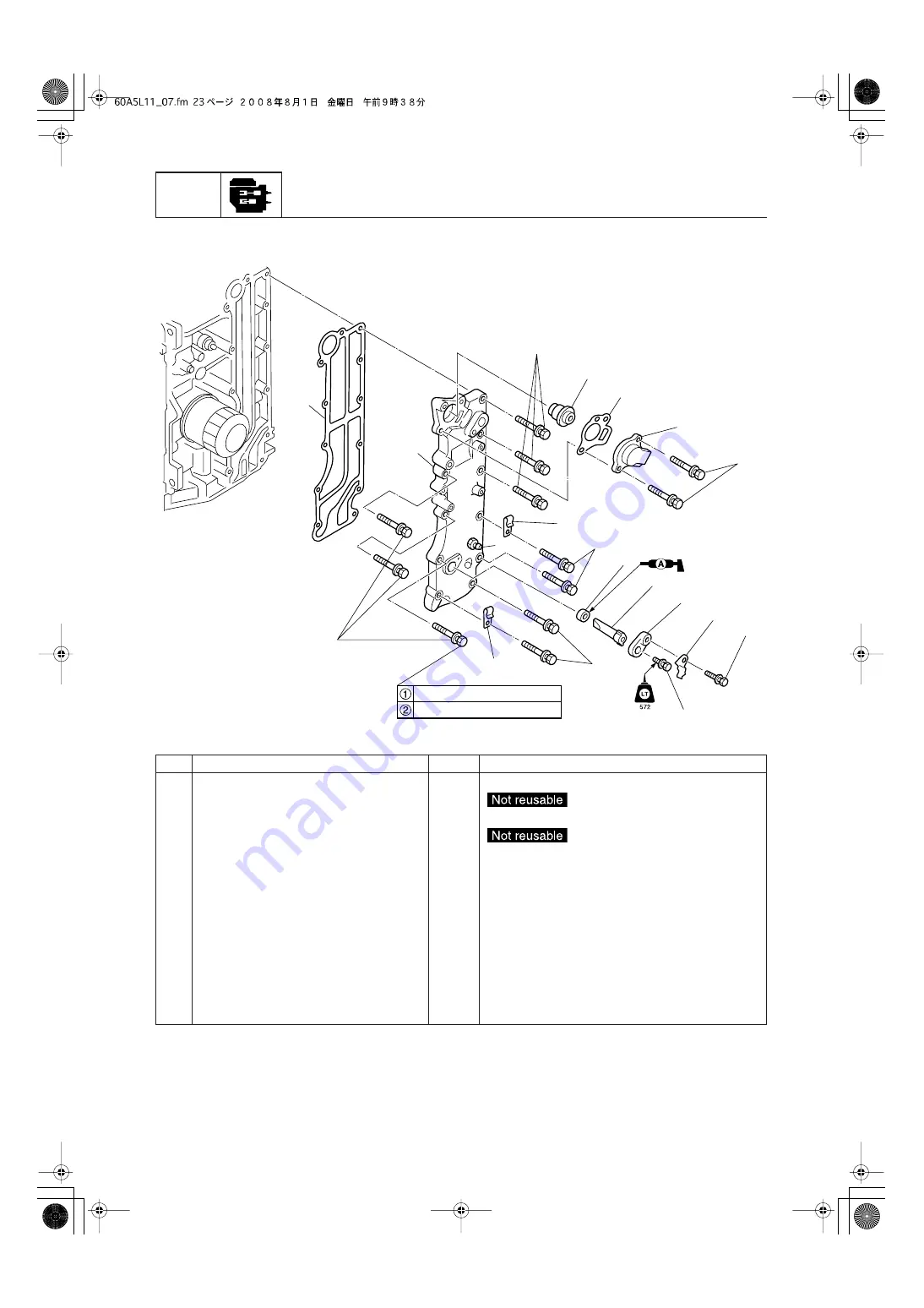
Power unit
7-23
POWR
Exhaust cover
1
2
3
4
5
6
7
14
7
6
8
9
10
11
12
6
13
6
6
6 N·m (0.6 kgf·m, 4.4 ft·lb)
12 N·m (1.2 kgf·m, 8.9 ft·lb)
No
Part name
Q’ty
Remarks
1
Exhaust cover
1
2
Gasket
1
3
Thermostat
1
4
Gasket
1
5
Cover
1
6
Bolt
12
M6
×
35 mm
7
Clamp
2
8
Grommet
1
9
Anode
1
10
Cover
1
11
Plate
1
12
Bolt
1
M6
×
20 mm
13
Bolt
1
M5
×
12 mm
14
Joint
1
Summary of Contents for F50D
Page 4: ......
Page 20: ...General information 0 15 GEN INFO MEMO ...
Page 38: ...Specification 1 17 SPEC MEMO ...
Page 56: ...Technical features and description 2 17 TECH FEA MEMO ...
Page 88: ...Troubleshooting 4 9 TRBL SHTG MEMO ...
Page 120: ...Electrical system 5 31 ELEC MEMO ...
Page 226: ...Lower unit 8 27 LOWR Shim location T2 T1 T3 ...
Page 269: ...8 70 0 1 2 3 4 5 6 7 8 9 10 A Shim location T1 T3 Shimming FT50C ...
Page 334: ...Bracket unit 9 55 BRKT MEMO ...
Page 364: ......
Page 372: ......