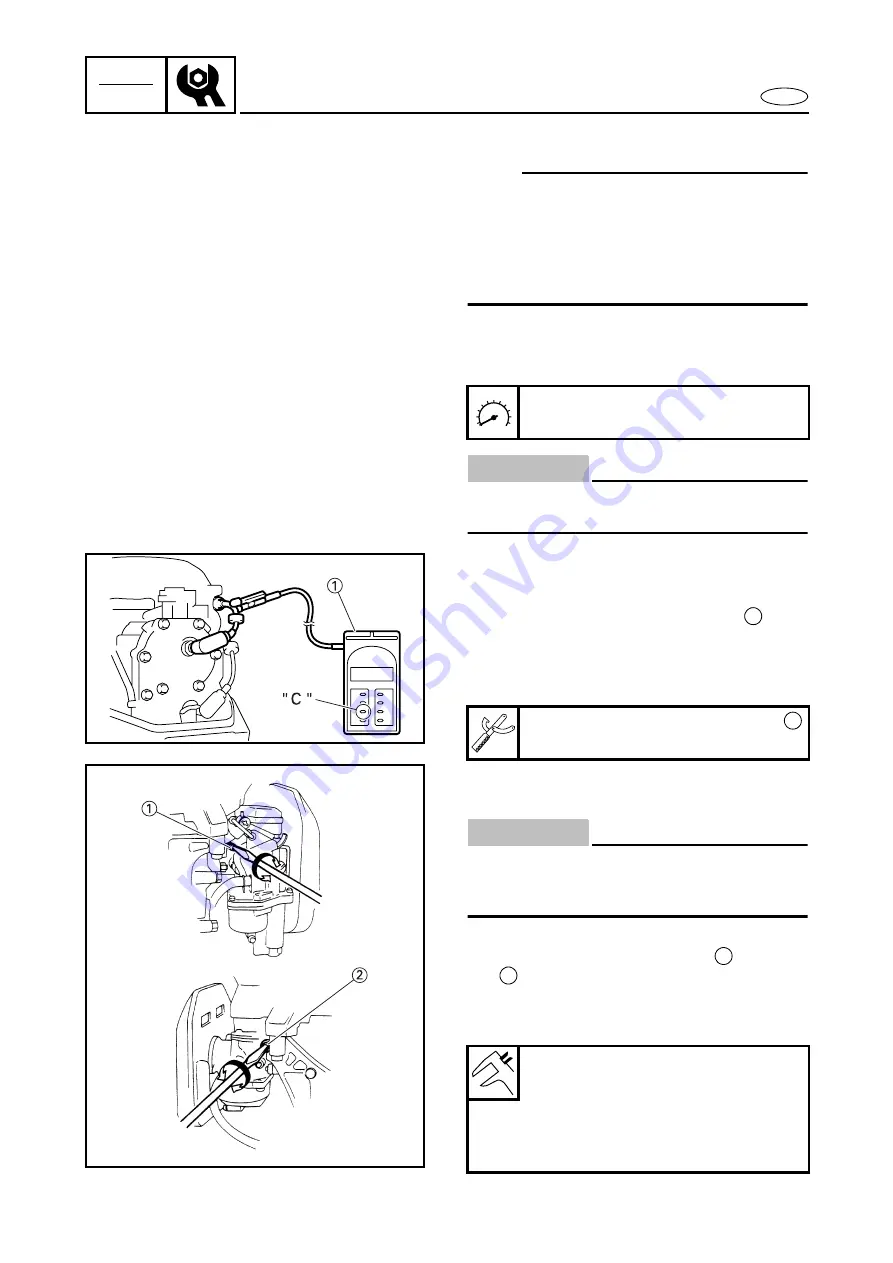
CONTROL SYSTEM
CHK
ADJ
3-15
E
ADJUSTING THE ENGINE IDLE SPEED
NOTE:
• The engine should be warmed up for the
adjustment. Correct adjustment cannot
be obtained when the engine is cold.
• Make sure that the pilot screw adjust-
ment is normal before implementing
idling stop screw adjustment.
1. Measure:
•
Engine idle speed
Out of specification
→
Adjust.
CAUTION:
Install the engine in the test tank to check
the engine idle speed.
Measuring steps
(1) Start the engine and allow it to warm
up for a few minutes.
(2) Install the digital tachometer
onto
the spark plug lead of cylinder #1.
(3) "Press the position key "C" on the digi-
tal tachometer."
2. Adjust:
• Carburetor pilot screw
CAUTION:
Do not adjust the carburetor when it is
operating properly. Excessive adjustment
may cause the engine poor performance.
Adjustment steps
(1) Turn in the pilot screw (
:Gasoline,
:Kerosene) until they are lightly seated.
(2) Turn out the pilot screws by specified
number of turns.
Engine idle speed
1,300 ± 50 r/min
Digital Tachometer
........................
90890-06760
Pilot screw turn-out
Gasoline carburetor
::::
1 - 1/2 ± 1/2
Kerosene carburetor:
1/2 + 2
1/2 - 1/2
1
1
1
2
Summary of Contents for EK25BMH
Page 8: ......
Page 21: ...FEATURES AND BENEFITS 1 12 E GEN INFO COOLING SYSTEM Fig 5 ...
Page 24: ......
Page 33: ...MAINTENANCE SPECIFICATIONS SPEC 2 8 E DIMENSIONS ...
Page 38: ......
Page 87: ......
Page 141: ......
Page 174: ......
Page 202: ......
Page 218: ...CHARGING SYSTEM ELEC 8 15 E CHARGING SYSTEM WIRING DIAGRAM 1 Lighting coil G Green ...
Page 220: ......
Page 226: ......
Page 227: ......
Page 228: ...Printed on recycled paper Printed in Japan Oct 2000 0 3 1 EK25BMH YAMAHA MOTOR CO LTD ...
Page 230: ......