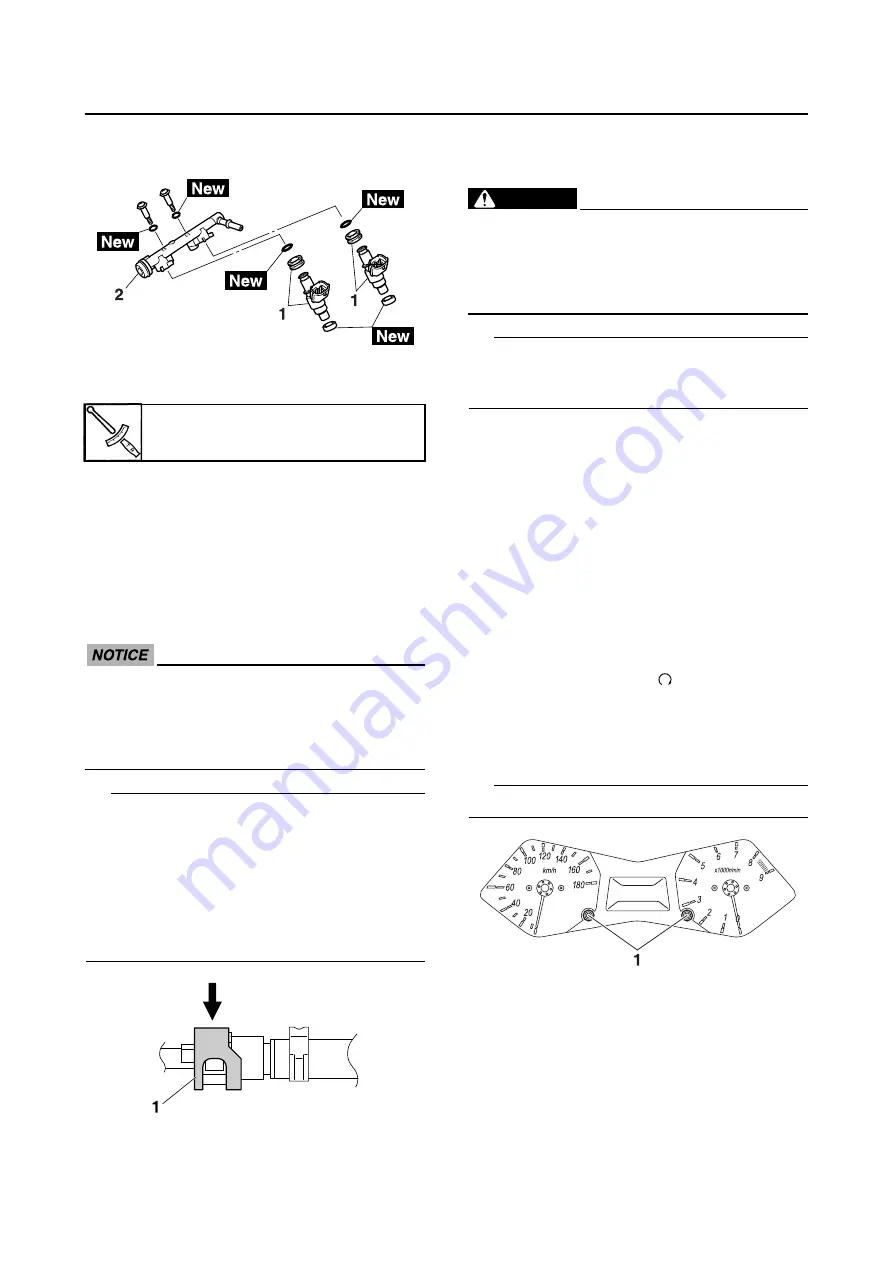
THROTTLE BODY
7-9
3. Install a new seal onto the end of each
injector.
4. Install the injector assembly to the intake
manifold with the screws and new gaskets.
5. Check the fuel pressure.
Refer to “CHECKING THE FUEL PRES-
SURE” on page 7-3.
EAS59C1707
INSTALLING THE FUEL HOSE (INJECTOR
SIDE)
1. Connect:
• Fuel hose (injector side)
ECA59C1706
When installing the fuel hose, make sure
that it is securely connected, and that the
fuel hose connector cover on the fuel hose
is in the correct position, otherwise the fuel
hose will not be properly installed.
TIP
• Install the fuel hose securely onto the fuel rail
until a distinct “click” is heard.
• To install the fuel hose onto the fuel rail, slide
the fuel hose connector cover “1” on the end
of the hose in the direction of the arrow
shown.
• It is prohibited to wear the cotton work gloves
or equivalent coverings.
EAS59C1706
ADJUSTING THE THROTTLE POSITION
SENSOR
WARNING
EWA59C1701
• Handle the throttle position sensor with
special care.
• Never subject the throttle position sensor
to strong shocks. If the throttle position
sensor is dropped, replace it.
TIP
Before adjusting the throttle position sensor,
the engine idling speed should be properly
adjusted.
1. Check:
• Throttle position sensor
Refer to “CHECKING THE THROTTLE
POSITION SENSOR” on page 8-139.
2. Adjust:
• Throttle position sensor angle
▼▼▼▼▼▼▼▼▼▼▼▼▼▼▼▼▼▼▼▼▼▼▼▼▼▼▼▼▼▼
a. Temporary tighten the throttle position sen-
sor.
b. Check that the throttle grip is fully closed.
c. Connect the throttle position sensor to the
wire harness.
d. Set the main switch to “OFF” and set the
engine stop switch to “
”.
e. Simultaneously press and hold the left set
and right set buttons “1”, set the main
switch to “ON”, and continue to press the
buttons for 8 seconds more.
TIP
“dIAG” appears on the odometer LCD.
f.
Diagnostic code number “d:01” is selected.
g. Adjust the position of the throttle position
sensor angle so that 14–20 can appear in
the meter.
h. After adjusting the throttle position sensor
angle, tighten the throttle position sensor
screws “2”.
Fuel rail screw
3.5 Nm (0.35 m·kgf, 2.5 ft·lbf)
Summary of Contents for 2012 TMAX XP500A
Page 1: ...SERVICE MANUAL XP500A 2012 59C 28197 E1 ...
Page 6: ......
Page 8: ......
Page 54: ...SPECIAL TOOLS 1 45 ...
Page 79: ...LUBRICATION POINTS AND LUBRICANT TYPES 2 24 ...
Page 82: ...LUBRICATION SYSTEM CHART AND DIAGRAMS 2 27 EAS20410 LUBRICATION DIAGRAMS ...
Page 84: ...LUBRICATION SYSTEM CHART AND DIAGRAMS 2 29 ...
Page 86: ...LUBRICATION SYSTEM CHART AND DIAGRAMS 2 31 ...
Page 88: ...LUBRICATION SYSTEM CHART AND DIAGRAMS 2 33 ...
Page 90: ...COOLING SYSTEM DIAGRAMS 2 35 EAS20420 COOLING SYSTEM DIAGRAMS ...
Page 92: ...COOLING SYSTEM DIAGRAMS 2 37 ...
Page 94: ...CABLE ROUTING 2 39 EAS20430 CABLE ROUTING Handlebar top side view ...
Page 96: ...CABLE ROUTING 2 41 Handlebar front side and left side view ...
Page 98: ...CABLE ROUTING 2 43 Front brake front side and left side view ...
Page 100: ...CABLE ROUTING 2 45 Frame front side view ...
Page 102: ...CABLE ROUTING 2 47 Frame left side view ...
Page 104: ...CABLE ROUTING 2 49 Frame right side view ...
Page 106: ...CABLE ROUTING 2 51 Rear frame top side and right side view ...
Page 108: ...CABLE ROUTING 2 53 Rear brake top side and left side view ...
Page 110: ...CABLE ROUTING 2 55 Throttle body left side view ...
Page 112: ...CABLE ROUTING 2 57 Fuel tank top side left side and right side view ...
Page 114: ...CABLE ROUTING 2 59 Hydraulic unit top side and front side view ...
Page 116: ...CABLE ROUTING 2 61 ...
Page 119: ......
Page 154: ...PERIODIC MAINTENANCE 3 35 ...
Page 258: ...SWINGARM 4 101 ...
Page 329: ...OIL PUMP 5 68 ECA13890 After tightening the bolts make sure the oil pump turns smoothly ...
Page 346: ...TRANSMISSION 5 85 ...
Page 371: ...THROTTLE BODY 7 10 Throttle position sensor screw 3 5 Nm 0 35 m kgf 2 5 ft lbf ...
Page 372: ...THROTTLE BODY 7 11 ...
Page 375: ......
Page 376: ...IGNITION SYSTEM 8 1 EAS27090 IGNITION SYSTEM EAS27110 CIRCUIT DIAGRAM ...
Page 380: ...ELECTRIC STARTING SYSTEM 8 5 EAS27160 ELECTRIC STARTING SYSTEM EAS27170 CIRCUIT DIAGRAM ...
Page 386: ...CHARGING SYSTEM 8 11 EAS27200 CHARGING SYSTEM EAS27210 CIRCUIT DIAGRAM ...
Page 389: ...CHARGING SYSTEM 8 14 ...
Page 390: ...LIGHTING SYSTEM 8 15 EAS27240 LIGHTING SYSTEM EAS27250 CIRCUIT DIAGRAM ...
Page 394: ...SIGNALING SYSTEM 8 19 EAS27270 SIGNALING SYSTEM EAS27280 CIRCUIT DIAGRAM ...
Page 399: ...SIGNALING SYSTEM 8 24 ...
Page 400: ...COOLING SYSTEM 8 25 EAS27300 COOLING SYSTEM EAS27310 CIRCUIT DIAGRAM ...
Page 404: ...FUEL INJECTION SYSTEM 8 29 EAS27331 FUEL INJECTION SYSTEM EAS27340 CIRCUIT DIAGRAM ...
Page 445: ...FUEL INJECTION SYSTEM 8 70 ...
Page 446: ...FUEL PUMP SYSTEM 8 71 EAS27550 FUEL PUMP SYSTEM EAS27560 CIRCUIT DIAGRAM ...
Page 449: ...FUEL PUMP SYSTEM 8 74 ...
Page 450: ...IMMOBILIZER SYSTEM 8 75 EAS27640 IMMOBILIZER SYSTEM EAS27650 CIRCUIT DIAGRAM ...
Page 459: ...IMMOBILIZER SYSTEM 8 84 ...
Page 460: ...ABS ANTI LOCK BRAKE SYSTEM 8 85 EAS28790 ABS ANTI LOCK BRAKE SYSTEM EAS27730 CIRCUIT DIAGRAM ...
Page 462: ...ABS ANTI LOCK BRAKE SYSTEM 8 87 EAS27740 ABS COMPONENTS CHART ...
Page 464: ...ABS ANTI LOCK BRAKE SYSTEM 8 89 EAS27750 ABS COUPLER LOCATION CHART ...
Page 468: ...ABS ANTI LOCK BRAKE SYSTEM 8 93 EAS27810 BASIC PROCESS FOR TROUBLESHOOTING ...
Page 493: ...ABS ANTI LOCK BRAKE SYSTEM 8 118 ...
Page 494: ...ELECTRICAL COMPONENTS 8 119 EAS27973 ELECTRICAL COMPONENTS ...
Page 496: ...ELECTRICAL COMPONENTS 8 121 ...
Page 498: ...ELECTRICAL COMPONENTS 8 123 EAS27981 CHECKING THE SWITCHES ...
Page 527: ......
Page 528: ......