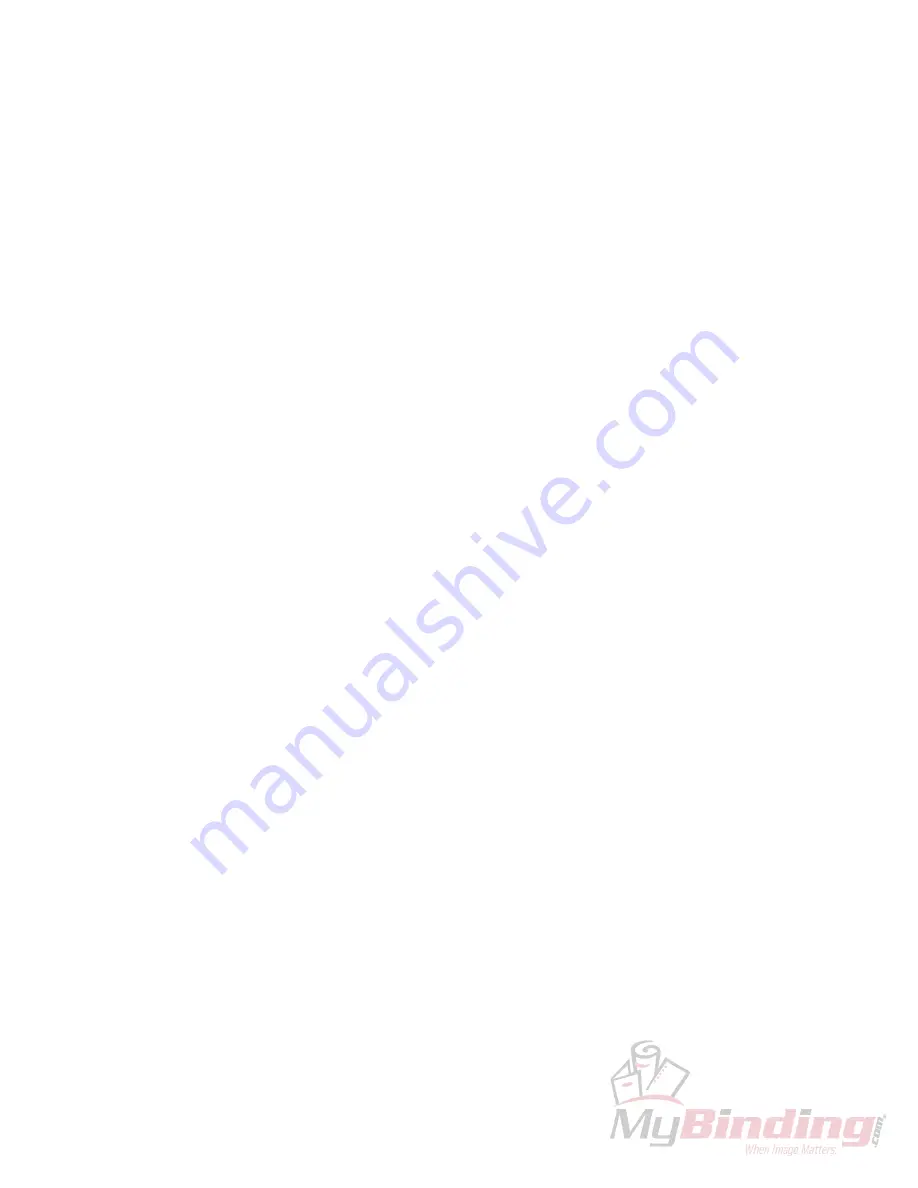
3
Introduction
Thank you for purchasing the XyronPro XM4400 Adhesive Transfer and Laminating System. We are
sure you will find this laminator to be useful, reliable, and easy-to-use. The XM4400 is designed to apply high
quality, adhesive or bubble free laminate to posters, banners, and any other visuals up to 42 inches wide and up to
300 feet long that you want to protect for future use. The machine and supplies are compatible with all types of
computer-printed media including laser, inkjet, color and thermal in a wide range of material sizes.
Technical Specifications
Mechanical Electrically Driven cold lamination 110V @ 2 Amp (max)
Supplies See page 17 for detailed supply roll information
Electrically driven cold lamination 110V @ 2 Amp (max)
Document size (max) 42” (W) x 300 feet (L) [108 cm (W) x 91.4 m (L)]
Laminate total thickness 0.004 inches (0.1 mm)
Document thickness 0.0 to 0.10 inches (2.54 mm)
Machine footprint [Inches] 50.5" L x 11" W x 14.5" H
Machine footprint [cm] 128.3 cm (L) x 27.94 cm (W) x 36.83 cm (H)]
Stand footprint [Inches] 49.5" L x 22" W x 28" H
Stand footprint [cm] 125.7 cm (L) x 55.88 cm (W) x 71.12 cm (H)
Machine weight 155 lbs. (70.45 kg)
Warnings
1.
Read and understand the Operation Manual and all safety labels before operating this machine.
2. Only a trained person is to be permitted to operate this machine. Training should include instruction
in operation under normal conditions and emergency situations.
3. This machine is to be serviced only by trained and authorized personnel. Follow lockout procedures
before servicing.
4. Never reach into the machine for any reason unless the machine is at a COMPLETE STOP.
5. Never leave the machine stopped in such a manner that another worker can start the machine while
you are working on or within the machine.
6. Never change or defeat the function of electrical interlocks or other machine "shutdown" switches.
7. Before starting this machine, check that:
- All persons are clear of the machine.
- No maintenance work is being performed on the machine.
- All guards are in place.
- All laminate rolls are well secured in the side plate slots.
- The machine is free of paper scraps, wraps and jams.
8. Equipment has pinch points that can cause injury. Keep hands, loose clothing, jewelry or hair away
from rollers during loading of the film.
9. Cutter has an exposed blade that could cause personal injury if contact is made. Use caution when
using or handling the hand held cutters.
10. Electric Shock Hazard. Do not open machine covers. No user serviceable parts inside covers.
11. The socket-outlet shall be installed near the equipment and shall be easily accessible.