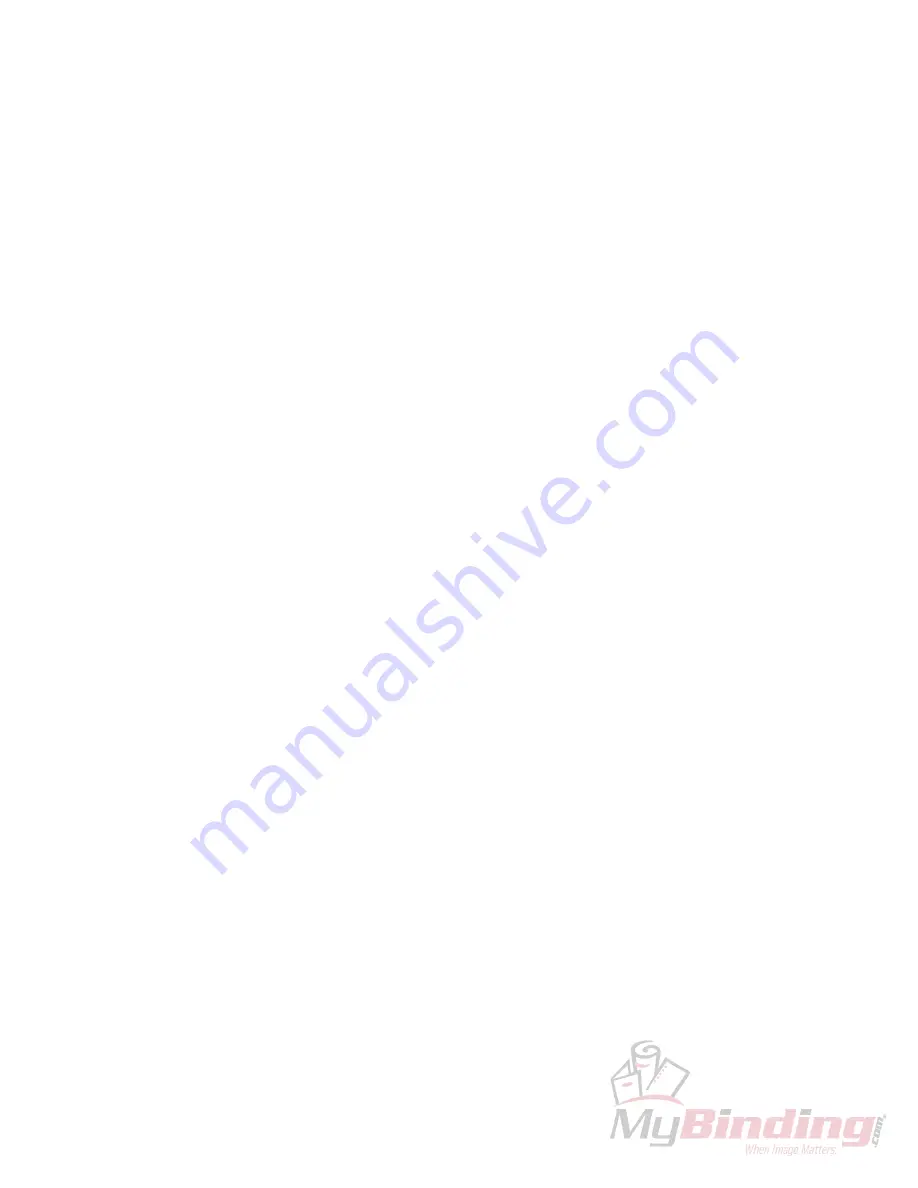
25
CONTACTING TECHNICAL SUPPORT
For machine parts and technical service in North America, please call: 1-800-793-3523. Please provide serial
number when calling for service. In Europe, please call: +49 711 8103 0.
PRODUCT WARRANTY
Xyron, Inc. warrants that the Xyron XM4400 is free from defects in material and workmanship for a period of one (1)
year from the date of purchase. Xyron, Inc. will repair or replace a defective product or part without charge provided
it is returned to the address below, freight prepaid with proof of purchase. If the product is damaged by neglect or
misuse the warranty is null and void.
WARRANTY CAUTION
The warranty made herein is in lieu of all other warranties, express or implied, including any warranty or
merchantability or fitness for a particular purpose. Xyron will not be liable for property damage or personal injury
(unless primarily caused by its negligence), loss of profit or other incidental or consequential damages arising out of
the use or inability to use the equipment.
EXCLUSIONS TO THE WARRANTY
This warranty specifically does not cover:
1. Damage to the laminating rolls caused by knives, razor blades, other sharp objects, or failure caused
by adhesives.
2. Damage to the machine caused by lifting, tilting, and/or any attempt to position the machine other
than rolling on the installed casters on even surfaces.
3. Improper use of the machine.
NOTICE
The information in this manual is subject to change without notice. Xyron shall not be liable for errors
contained herein or for incidental or consequential damages in connection with the furnishing, performance or
use of this material.
The purchase or acquisition of this product does not confer the right or license to use the machine and cartridges in
the retro-reflective field or to make or sell machines or cartridges for use in the retro-reflective field.
XYRON, INC. , 8465 N. 90th St., Suite #6, Scottsdale, AZ 85258
Esselte Leitz GmbH & Co KG, Siemensstr. 64, 70469 Stuttgart, Germany