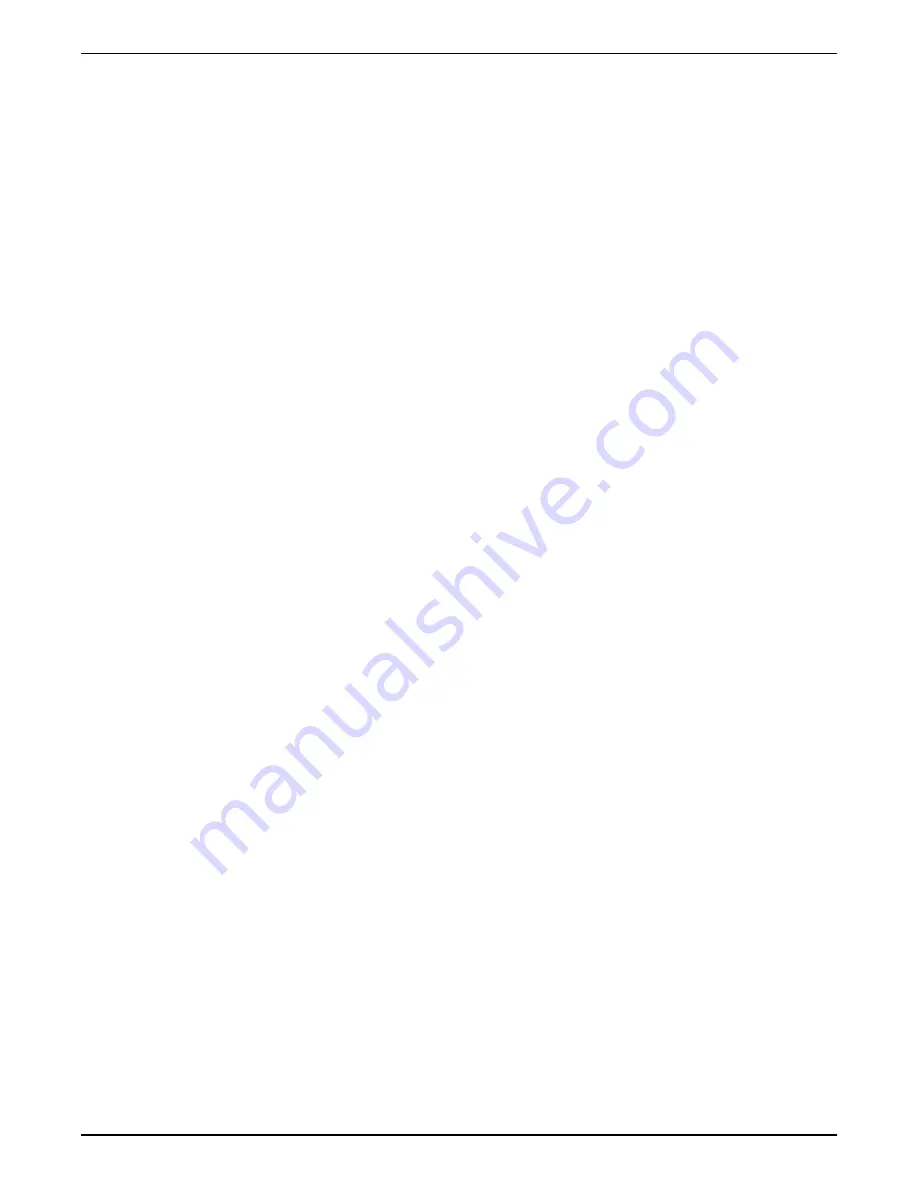
Table of Contents
1.1 Introduction.......................................................................................................................... 3
1.2 Safety terminology and symbols........................................................................................3
1.3 User safety.............................................................................................................................4
1.4 Special hazards.....................................................................................................................4
1.5 Protecting the environment................................................................................................5
1.6 Spare parts............................................................................................................................5
1.7 Warranty................................................................................................................................5
4.1.1 Pump design............................................................................................................... 13
4.1.2 The data plate............................................................................................................. 16
4.1.3 Product denomination............................................................................................... 16
4.2.1 Product design............................................................................................................17
4.2.2 Approvals.....................................................................................................................17
4.2.3 Parts.............................................................................................................................. 18
4.2.4 The data plate............................................................................................................. 18
5.1 Precautions......................................................................................................................... 19
5.2 Requirements..................................................................................................................... 20
5.3 Make the mechanical installation.....................................................................................20
5.3.1 Prepare the site: new P-installation.......................................................................... 20
5.3.2 Install the pump: P-installation..................................................................................21
5.3.3 Install the pump: S-installation..................................................................................22
5.3.4 Install the gateway...................................................................................................... 23
6.1 Precautions......................................................................................................................... 24
6.2 Requirements..................................................................................................................... 25
6.3 Make the electrical connections...................................................................................... 26
cables....................................................................................26
Table of Contents
Concertor
™
6020 Installation, Operation, and Maintenance Manual
1
Summary of Contents for Flygt Concertor 6020
Page 1: ...Installation Operation and Maintenance Manual Concertor 6020 ...
Page 2: ......
Page 53: ......
Page 54: ......
Page 55: ......