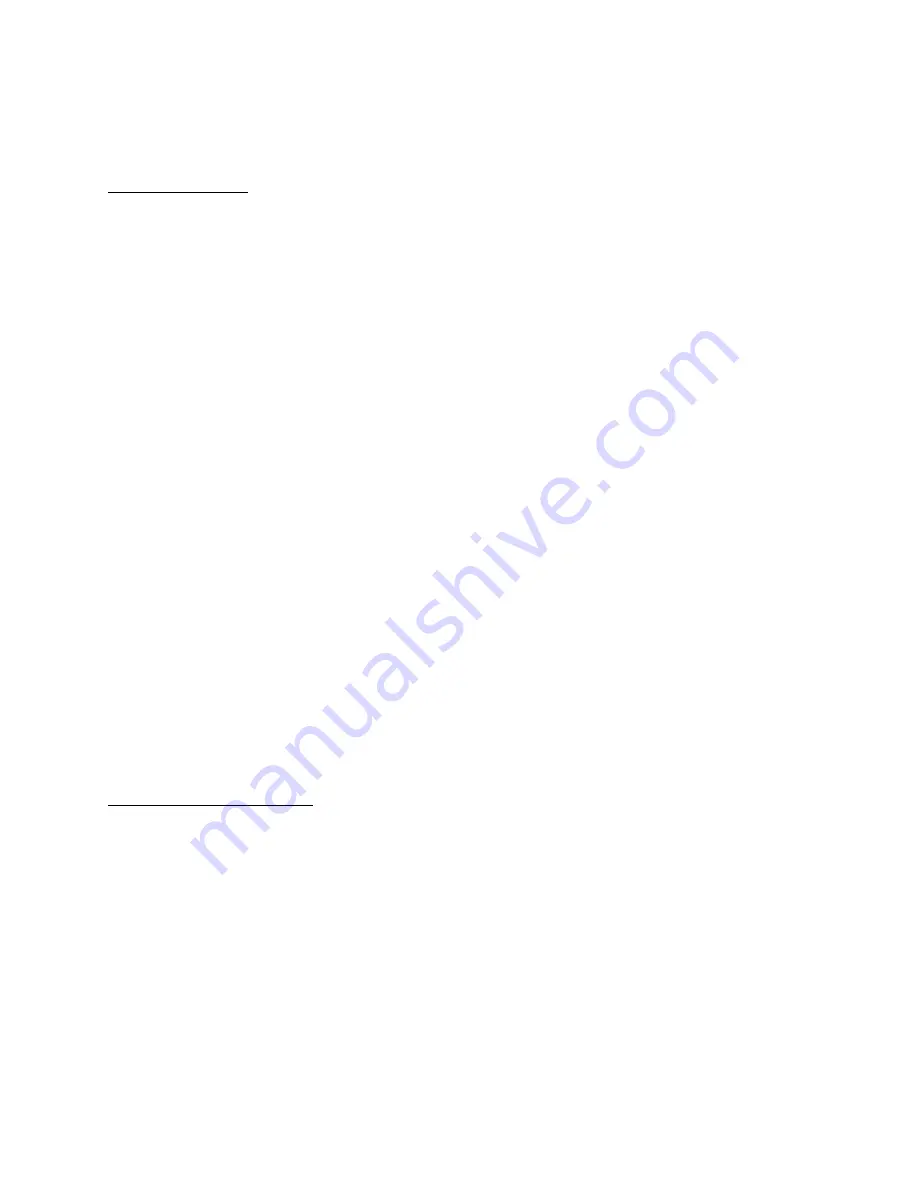
SECTION 6 – GENERAL SERVO INFORMATION
Servos - PWM
Servos operate using a Pulse Width Modulated (PWM) signal. This signal is
measured in microseconds, typically labeled as “µs”.
Sometime between 1950 and 1970 (nobody seems to know the exact date)
a couple of the radio control system manufacturers got together and came
up with the PWM protocol and what it means. The original specification
allowed for a servo pulse between 750µs and 2250µs to represent a
rotational position of a servo. In reality, the range was limited to between
1000µs and 2000µs. It was decided at some point that officially 100%
throws would be 1100µs to 1900µs, with 1500µs being dead center.
So, when you change your end point adjustments (EPA) or travel throw
limits (TTL) – all depending on the radio system you use – the percentage
you are adding is based on 100% being a 400µs difference from center. So,
at 125% throws the servo could move 125% of 400, which is 500. So,
125% throws are 1000µs to 2000µs. 150% of 400 is 600. So 150% throws
are 900µs to 2100µs. Center is always 1500µs except for Futaba, which
typically uses 1520µs. Multiplex systems have a mode where center is
1400µs.
The X24 can increase your throw well beyond what a servo will handle,
especially if you have your transmitter's end points at 150% already. So be
careful when changing end points with the X24 unless your transmitter's end
points are all set to 100%.
Servos – Frame rate
Servos require that the PWM pulse be “refreshed” at some interval. In the
history of R/C this refresh has been around every 22ms (about 44.45 times
per second). So, for example every 22ms the PWM pulse of 1500µs is
output to make a servo go to center.
There is a limitation of how fast the refresh rate can be. Analog servos are
typically limited to a max of about 15ms refreshes. Any faster and the
amplifier circuit never reduces its current draw and the servo can burn up.
The faster the frame rate, the less latency the system will have.
52