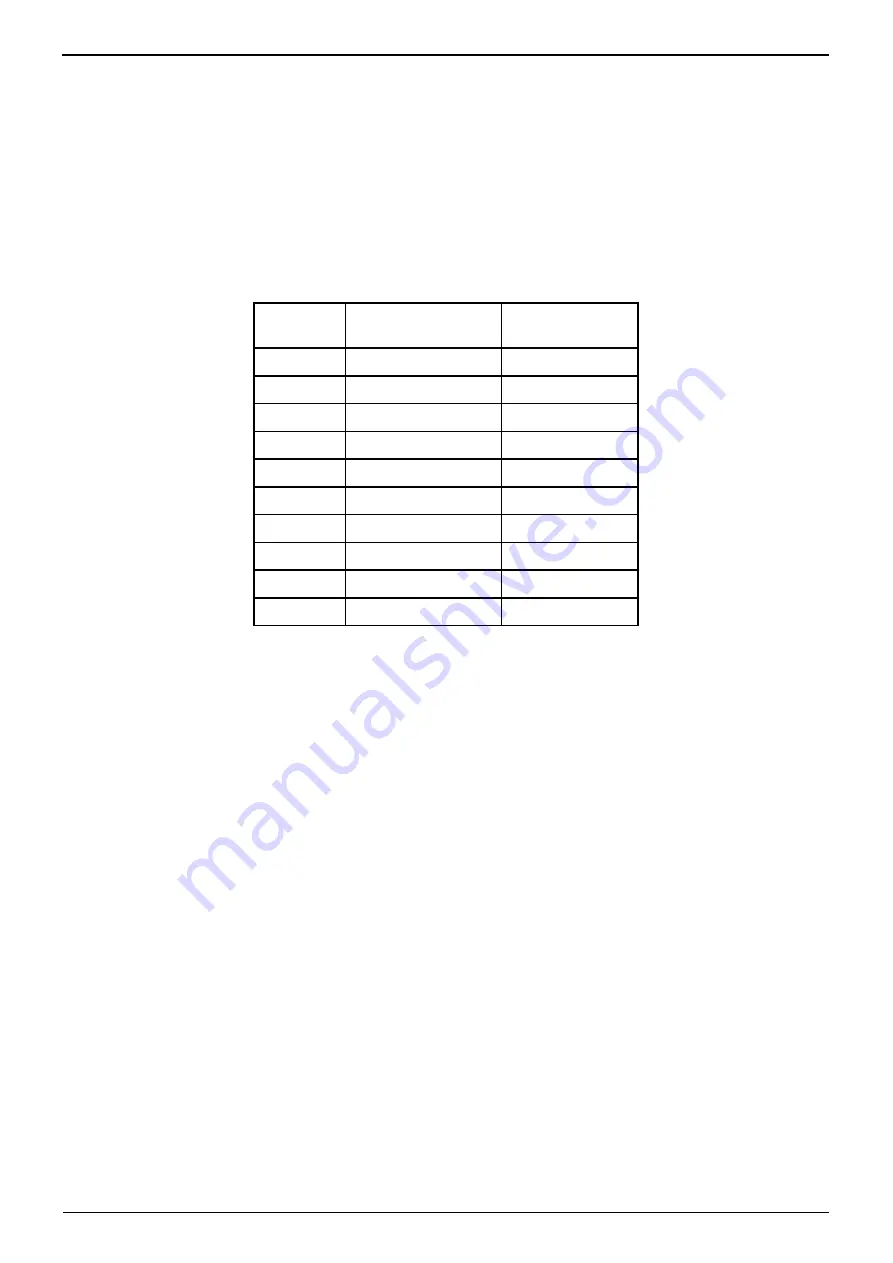
Xtralis ICAM
Xtralis ICAM ILS-1 Product Guide
6.3.2 Flow Delays
When airflow limits are exceeded, a Flow Fault will appear after a programmable Flow Delay time. The
default Flow Delay time is approximately 30 seconds. Once the airflow is returned to a normal level, the
fault condition will be cleared within 18 seconds. Available settings for Flow Delay are shown in Table 6-
2.
In environments where the sampled airflow may be affected by sudden temperature or pressure
changes or if there is a risk of physical interference of the sampling point (e.g. prison cell applications)
then it may be necessary to increase the Flow Delay time.
Table 6-2: Flow Delay Settings
Bargraph
LED
Flow into Fault
Delay (Seconds)
Flow out of Fault
(Seconds)
0 15
2
1 30
18
2 60
18
3 90
18
4 120
18
5 150
18
6 180
18
7 210
18
8 240
18
9 270
18
Note:
Timings are approximate.
Note:
The default flow delay setting is 1.
6.3.3 Flow Sensitivity
This setting determines the units responsiveness in reporting blocked sampling points or broken pipes.
The default flow sensitivity value of 9 will configure the unit to declare a flow fault whenever there has
been a change in volumetric airflow of ± 20% from the calibrated reading for at least the duration of the
flow delay, see Section 6.3.2. For most installations, especially if compliance with EN54-20 is required,
the default setting should be used.
In certain circumstances, such as rapid changes in ambient air pressures due to air handling units,
doors opening/closing etc. the default setting may appear to be too sensitive. Under these conditions,
the flow delay setting should be increased to allow time for the air pressures to stabilize after the
temporary event.
Only under extreme environmental conditions or non standard pipe configurations should decreasing
the flow sensitivity be considered.
www.xtralis.com
13