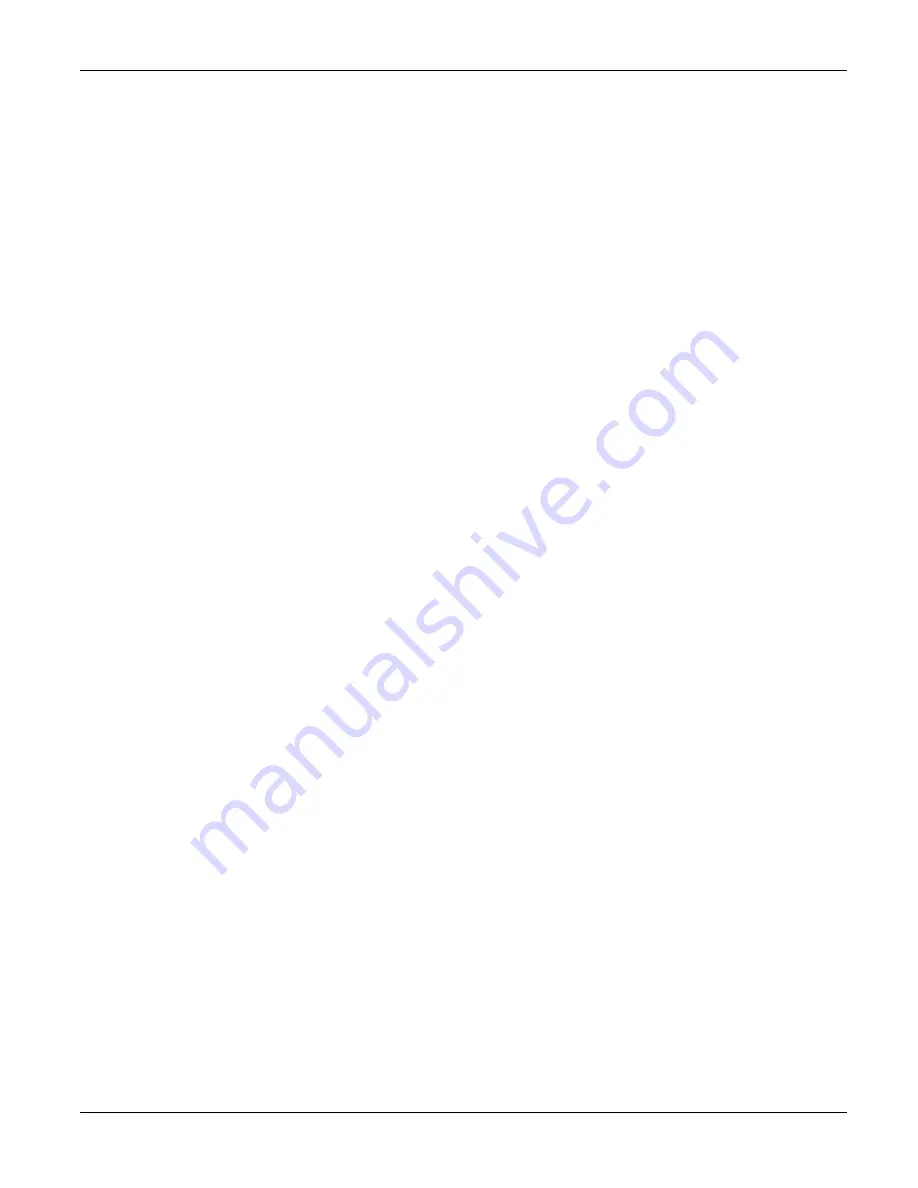
Status Indicator RAPs
WorkCentre 3119
07/06
2-3
1 Initial Checks RAP
WARNING
Switch off the electricity to the machine. Disconnect the power cord from the customer supply
while performing tasks that do not need electricity. Electricity can cause death or injury. Moving
parts can cause injury.
Basic Check List
1. Check the Power.
•
Does "Warming Up" appear on the display?
--> If not check power cable, switch or SMPS/HVPS, PL 1.
--> Does the wall socket work?
•
Do the motors or other components initialize (listen for the main motor, fan and LSU, PL 1
sounds)?
--> If not or there are none of the normal startup sounds, check the cable, switch and/or
SMPS/HVPS, PL 1.
--> Does the wall socket work?
2. Check the LCD Panel.
•
Refer to General Procedures.
•
Is there any display at all?
--> If not, check the power cable, switch and/or SMPS/HVPS, PL 1.
•
Is the display showing an error message? Are there any broken or badly formed characters?
•
Is the message on the LCD Panel, PL 8 a standard error message? Refer to GP 9.
--> Does the wall socket work?
--> Check the main PBA and cable harness, PL 1.
--> Check for paper jams, refer to GP 6.
3. Check the Paper Path
•
Is there a Paper Jam?
--> Remove any paper fragments caught in the paper path, refer to GP 6.
•
Paper Jam occurs repeatedly at a specific point in the Paper Path
--> Open the fuser cover, REP 9 and clear the jam, refer to GP 6.
--> Dismantle the machine and carefully inspect the region where the jam occurs.
Check if paper fragments are caught in the Fuser, refer to GP 6.
4. Print a test page.
•
Try printing a test page from a computer.
--> If there is an error, check cables and driver installation.
5. Check the Print Quality.
•
Is there a Print Quality Problem?
--> Go to Section 3, Image Quality.
Summary of Contents for WorkCentre 3119
Page 1: ...Part Number 708P88471 06 06 WORKCENTRE 3119 SERVICE MANUAL ...
Page 4: ...Introduction ii 06 06 WorkCentre 3119 Page intentionally blank ...
Page 14: ...Introduction xii 06 06 WorkCentre 3119 Page intentionally blank ...
Page 16: ...Service Call Procedures 1 2 06 06 WorkCentre 3119 Page intentionally blank ...
Page 20: ...Status Indicator RAPs 2 2 06 06 WorkCentre 3119 Page intentionally blank ...
Page 44: ...Image Quality 3 2 06 06 WorkCentre 3119 Page intentionally blank ...
Page 64: ...Image Quality 3 22 06 06 WorkCentre 3119 Page intentionally blank ...
Page 66: ...Repairs Adjustments 4 2 06 06 WorkCentre 3119 Page intentionally blank ...
Page 92: ...Spare Parts List 5 2 06 06 WorkCentre 3119 PL 1 Main Assembly ...
Page 94: ...Spare Parts List 5 4 06 06 WorkCentre 3119 PL 2 Housing Base Assembly ...
Page 96: ...Spare Parts List 5 6 06 06 WorkCentre 3119 PL 3 Frame Assembly 1 ...
Page 98: ...Spare Parts List 5 8 06 06 WorkCentre 3119 PL 4 Frame Assembly 2 ...
Page 100: ...Spare Parts List 5 10 06 06 WorkCentre 3119 PL 5 Fuser Unit ...
Page 102: ...Spare Parts List 5 12 06 06 WorkCentre 3119 PL 6 Drive Assembly ...
Page 104: ...Spare Parts List 5 14 06 06 WorkCentre 3119 PL 7 Scan Assembly ...
Page 106: ...Spare Parts List 5 16 06 06 WorkCentre 3119 PL 8 OPE Assembly ...
Page 108: ...Spare Parts List 5 18 06 06 WorkCentre 3119 PL 9 Cassette Assembly ...
Page 112: ...General Procedures Information 6 2 06 06 WorkCentre 3119 Page intentionally blank ...
Page 125: ...General Procedures and Information WorkCentre 3119 06 06 6 15 Main Control ASIC Figure 8 ...
Page 162: ...General Procedures and Information 6 52 06 06 WorkCentre 3119 Page intentionally blank ...
Page 164: ...Wiring Diagrams 7 2 06 06 WorkCentre 3119 Page intentionally blank ...
Page 165: ...Wiring Diagrams WorkCentre 3119 06 06 7 3 WD 1 PJ Locations Figure 1 ...
Page 166: ...Wiring Diagrams 7 4 06 06 WorkCentre 3119 WD 2 Connection Diagram 1 2 Figure 2 ...
Page 167: ...Wiring Diagrams WorkCentre 3119 06 06 7 5 WD 3 Connection Diagram 2 2 Figure 3 ...
Page 168: ...Wiring Diagrams 7 6 06 06 WorkCentre 3119 WD 4 Main PBA 1 6 Figure 4 ...
Page 169: ...Wiring Diagrams WorkCentre 3119 06 06 7 7 WD 5 Main PBA 2 6 Figure 5 ...
Page 170: ...Wiring Diagrams 7 8 06 06 WorkCentre 3119 WD 6 Main PBA 3 6 Figure 6 ...
Page 171: ...Wiring Diagrams WorkCentre 3119 06 06 7 9 WD 7 Main PBA 4 6 Figure 7 ...
Page 172: ...Wiring Diagrams 7 10 06 06 WorkCentre 3119 WD 8 Main PBA 5 6 Figure 8 ...
Page 173: ...Wiring Diagrams WorkCentre 3119 06 06 7 11 WD 9 Main PBA 6 6 Figure 9 ...
Page 174: ...Wiring Diagrams 7 12 06 06 WorkCentre 3119 WD 10 OPE PBA Figure 10 ...
Page 175: ...Wiring Diagrams WorkCentre 3119 06 06 7 13 WD 11 SMPS 110V 1 4 Figure 11 ...
Page 176: ...Wiring Diagrams 7 14 06 06 WorkCentre 3119 WD 12 SMPS 110V 2 4 Figure 12 ...
Page 177: ...Wiring Diagrams WorkCentre 3119 06 06 7 15 WD 13 SMPS 110V 3 4 Figure 13 ...
Page 178: ...Wiring Diagrams 7 16 06 06 WorkCentre 3119 WD 14 SMPS 110V 4 4 Figure 14 ...
Page 179: ...Wiring Diagrams WorkCentre 3119 06 06 7 17 WD 15 SMPS 220V 1 4 Figure 15 ...
Page 180: ...Wiring Diagrams 7 18 06 06 WorkCentre 3119 WD 16 SMPS 220V 2 4 Figure 16 ...
Page 181: ...Wiring Diagrams WorkCentre 3119 06 06 7 19 WD 17 SMPS 220V 3 4 Figure 17 ...
Page 182: ...Wiring Diagrams 7 20 06 06 WorkCentre 3119 WD 18 SMPS 220V 4 4 Figure 18 ...
Page 183: ...Wiring Diagrams WorkCentre 3119 06 06 7 21 Page intentionally blank ...