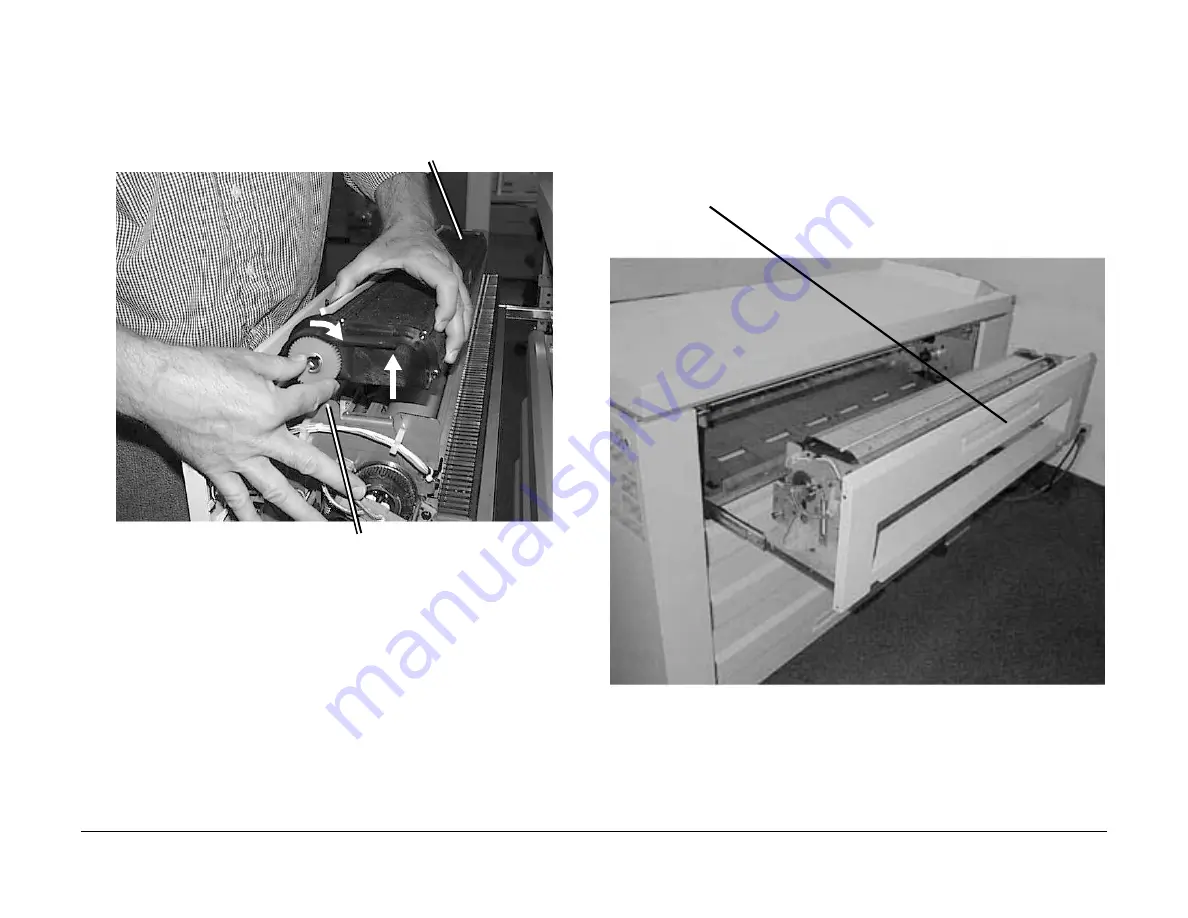
03/2003
4-126
8850/ 510DP
REP 10.5, REP 10.6
Repairs and Adjustments
3.
(Figure 6): Reinstall the Web Oiler Assembly on the Printer.
Figure 6 Reinstalling the Web Oiler Assembly
4.
Return the Printer to normal operating condition.
5.
Enter the Printer diagnostics and perform the following:
a.
10-30 Web Oiler Parameters Reset - to reset the meter if a new Web Oiler is
installed.
b.
10-31 Partial Web Oiler Parameters Reset - to reset the parameters for a partially
used Web. Measure the diameter of the remaining web on the Supply Roll in millime-
ters and enter this value.
REP 10.6 Thermal Fuse (F1)
Parts List on
Removal
1.
(Figure 1): Access the Fuser Module.
Figure 1 Accessing the Fuser Module
2.
Remove the Fuser Heat Roll (REP 10.2).
1
Position the Web Oiler Assembly so
that the drive side is on the right side of
the Fuser Drawer
2
Slide the two prongs on the left
side of the Web Oiler Assembly
into the slots on left side of the
Fuser Drawer
3
Lift the right side of the Web Oiler
Assembly slightly and turn the
Takeup Roll clockwise to remove
any remaining slack in that roll
4
Set the Web Oiler back down on
the Fuser Assembly and tighten
down the two mount screws
1
Pull up on the handle and pull open the
Fuser Module Drawer.
Summary of Contents for Synergix 8850
Page 1: ...03 2003 1 8850 510DP Transmittal Page Transmittal Page 3...
Page 2: ...03 2003 2 8850 510DP Transmittal Page...
Page 5: ...03 2003 1 8850 510DP Title Pages Title Pages...
Page 6: ...03 2003 2 8850 510DP Title Pages...
Page 8: ......
Page 10: ...03 2003 2 8850 510DP Introduction...
Page 16: ...03 2003 viii 8850 510DP Introduction...
Page 18: ...03 2003 1 2 8850 510DP Service Call Procedures...
Page 34: ...03 2003 1 18 8850 510DP Callback System Checkout Final Action Service Call Procedures...
Page 36: ...03 2003 2 2 8850 510DP Status Indicator RAPs...
Page 54: ...03 2003 2 20 8850 510DP Generic Sensor RAP Generic Switch RAP Status Indicator RAPs...
Page 56: ...03 2003 3 2 8850 510DP Print Quality...
Page 76: ...03 2003 3 22 8850 510DP PQ 22 PQ 23 Print Quality...
Page 78: ...03 2003 4 2 8850 510DP Repairs and Adjustments...
Page 100: ...03 2003 4 24 8850 510DP REP 7 14 Repairs and Adjustments...
Page 186: ...03 2003 4 110 8850 510DP REP 9 25 Repairs and Adjustments...
Page 214: ...03 2003 4 138 8850 510DP REP 10 11 Repairs and Adjustments...
Page 218: ...03 2003 4 142 8850 510DP REP 14 1 Repairs and Adjustments...
Page 234: ...03 2003 4 158 8850 510DP ADJ 10 3 Repairs and Adjustments...
Page 236: ...03 2003 5 2 8850 510DP Parts Lists...
Page 242: ...03 2003 5 8 8850 510DP Parts Lists Intentionally left blank...
Page 286: ...03 2003 5 52 8850 510DP Part Number Index Parts Lists...
Page 288: ...03 2003 6 2 8850 510DP General Procedures...
Page 304: ...03 2003 6 18 8850 510DP GP 9 General Procedures...
Page 336: ...03 2003 6 50 8850 510DP SPS 510dp Change Tag Information General Procedures...
Page 338: ...03 2003 7 2 8850 510DP Wiring Data...
Page 340: ...03 2003 7 4 8850 510DP Level 1 BSD Wiring Data Level 1 BSD...
Page 341: ...03 2003 7 5 8850 510DP Level 1 BSD Wiring Data BSD 8 1...
Page 342: ...03 2003 7 6 8850 510DP Level 1 BSD Wiring Data...
Page 343: ...03 2003 7 7 8850 510DP Level 1 BSD Wiring Data...
Page 344: ...03 2003 7 8 8850 510DP BSD 1 1 Wiring Data BSD 1 1 Main Power On 50 and 60 HZ...
Page 346: ...03 2003 7 10 8850 510DP BSD 1 2 Wiring Data BSD 1 2 DC Power Generation 1 of 3...
Page 348: ...03 2003 7 12 8850 510DP BSD 1 3 Wiring Data BSD 1 3 Interlock Monitoring 1 OF 4...
Page 349: ...03 2003 7 13 8850 510DP BSD 1 3 Wiring Data 1 3 Interlock Monitoring 2 0F 4...
Page 352: ...03 2003 7 16 8850 510DP BSD 1 4 Wiring Data BSD 1 4 Machine Cooling...
Page 353: ...03 2003 7 17 8850 510DP BSD 2 1 Wiring Data BSD 2 1 Mode Selection...
Page 354: ...03 2003 7 18 8850 510DP BSD 2 1 Wiring Data...
Page 355: ...03 2003 7 19 8850 510DP BSD 3 1 Wiring Data BSD 3 1 Machine Run Control...
Page 356: ...03 2003 7 20 8850 510DP BSD 3 1 Wiring Data...
Page 357: ...03 2003 7 21 8850 510DP BSD 4 1 Wiring Data BSD 4 1 Fuser Heat Roll Drive...
Page 358: ...03 2003 7 22 8850 510DP BSD 4 2 BSD 4 3 Wiring Data BSD 4 2 Developer Drive BSD 4 3 Drum Drive...
Page 359: ...03 2003 7 23 8850 510DP BSD 4 3 Wiring Data...
Page 360: ...03 2003 7 24 8850 510DP BSD 6 1 Wiring Data BSD 6 1 Imaging Right Side...
Page 361: ...03 2003 7 25 8850 510DP BSD 6 1 Wiring Data...
Page 362: ...03 2003 7 26 8850 510DP BSD 6 1 Wiring Data...
Page 363: ...03 2003 7 27 8850 510DP BSD 7 1 Wiring Data BSD 7 1 Media Drive...
Page 364: ...03 2003 7 28 8850 510DP BSD 7 1 Wiring Data...
Page 365: ...03 2003 7 29 8850 510DP BSD 7 2 Wiring Data BSD 7 2 Media Feed Roll 1...
Page 366: ...03 2003 7 30 8850 510DP BSD 7 2 Wiring Data...
Page 367: ...03 2003 7 31 8850 510DP BSD 7 3 Wiring Data BSD 7 3 Media Feed Roll 2...
Page 368: ...03 2003 7 32 8850 510DP BSD 7 3 Wiring Data...
Page 369: ...03 2003 7 33 8850 510DP BSD 7 4 Wiring Data BSD 7 4 Media Feed Roll 3...
Page 370: ...03 2003 7 34 8850 510DP BSD 7 4 Wiring Data...
Page 371: ...03 2003 7 35 8850 510DP BSD 7 5 Wiring Data BSD 7 5 Media Cutting...
Page 372: ...03 2003 7 36 8850 510DP BSD 7 5 Wiring Data...
Page 375: ...03 2003 7 39 8850 510DP BSD 8 2 Wiring Data...
Page 376: ...03 2003 7 40 8850 510DP BSD 8 2 Wiring Data...
Page 377: ...03 2003 7 41 8850 510DP BSD 8 2 Wiring Data...
Page 379: ...03 2003 7 43 8850 510DP BSD 8 3 Wiring Data Figure 2 Print Transportation 2 of 2...
Page 380: ...03 2003 7 44 8850 510DP BSD 9 1 Wiring Data BSD 9 1 Charging Figure 1 Charging 1 of 2...
Page 381: ...03 2003 7 45 8850 510DP BSD 9 1 Wiring Data Figure 2 Charging 2 of 3...
Page 382: ...03 2003 7 46 8850 510DP BSD 9 1 Wiring Data Figure 3 Charging 3 of 3...
Page 383: ...03 2003 7 47 8850 510DP BSD 9 2 Wiring Data BSD 9 2 Exposure Figure 1 Exposure 1 of 1...
Page 384: ...03 2003 7 48 8850 510DP BSD 9 3 Wiring Data BSD 9 3 Development Figure 1 Development 1 of 4...
Page 385: ...03 2003 7 49 8850 510DP BSD 9 3 Wiring Data Figure 2 Development 2 of 4...
Page 386: ...03 2003 7 50 8850 510DP BSD 9 3 Wiring Data Figure 3 Development 3 of 4...
Page 387: ...03 2003 7 51 8850 510DP BSD 9 3 Wiring Data Figure 4 Development 4 of 4...
Page 389: ...03 2003 7 53 8850 510DP BSD 9 4 Wiring Data Figure 2 Image Transfer and Media Stripping 2 of 2...
Page 391: ...03 2003 7 55 8850 510DP BSD 9 5 Wiring Data Figure 2 Drum Cleaning 2 of 2...
Page 393: ...03 2003 7 57 8850 510DP BSD 9 6 Wiring Data Figure 2 Drum Discharging 2 of 2...
Page 395: ...03 2003 7 59 8850 510DP BSD 9 7 Wiring Data Figure 2 Toner Developer Dispense 2 of 3...
Page 396: ...03 2003 7 60 8850 510DP BSD 9 7 Wiring Data Figure 3 Toner Developer Dispense 3 of 3...
Page 397: ...03 2003 7 61 8850 510DP BSD 9 8 Wiring Data BSD 9 8 Corotron and Developer Bias Power...
Page 398: ...03 2003 7 62 8850 510DP BSD 9 8 Wiring Data...
Page 399: ...03 2003 7 63 8850 510DP BSD 10 1 Wiring Data BSD 10 1 Fuser Heat Figure 1 Fuser Heat 1 of 3...
Page 400: ...03 2003 7 64 8850 510DP BSD 10 1 Wiring Data Figure 2 Fuser Heat 2 of 3...
Page 401: ...03 2003 7 65 8850 510DP BSD 10 1 Wiring Data Figure 3 Fuser Heat 3 of 3...
Page 402: ...03 2003 7 66 8850 510DP BSD 10 2 Wiring Data BSD 10 2 Fuser Oil Dispensing...
Page 403: ...03 2003 7 67 8850 510DP BSD 10 2 Wiring Data Figure 1 Fuser Oil Dispensing 2 of 2...
Page 404: ...03 2003 7 68 8850 510DP BSD 10 3 Wiring Data BSD 10 3 Fusing and Jam Detection...
Page 405: ...03 2003 7 69 8850 510DP BSD 10 3 Wiring Data...
Page 406: ...03 2003 7 70 8850 510DP BSD 10 3 Wiring Data...
Page 407: ...03 2003 7 71 8850 510DP BSD 10 3 Wiring Data...
Page 408: ...03 2003 7 72 8850 510DP BSD 10 3 Wiring Data...