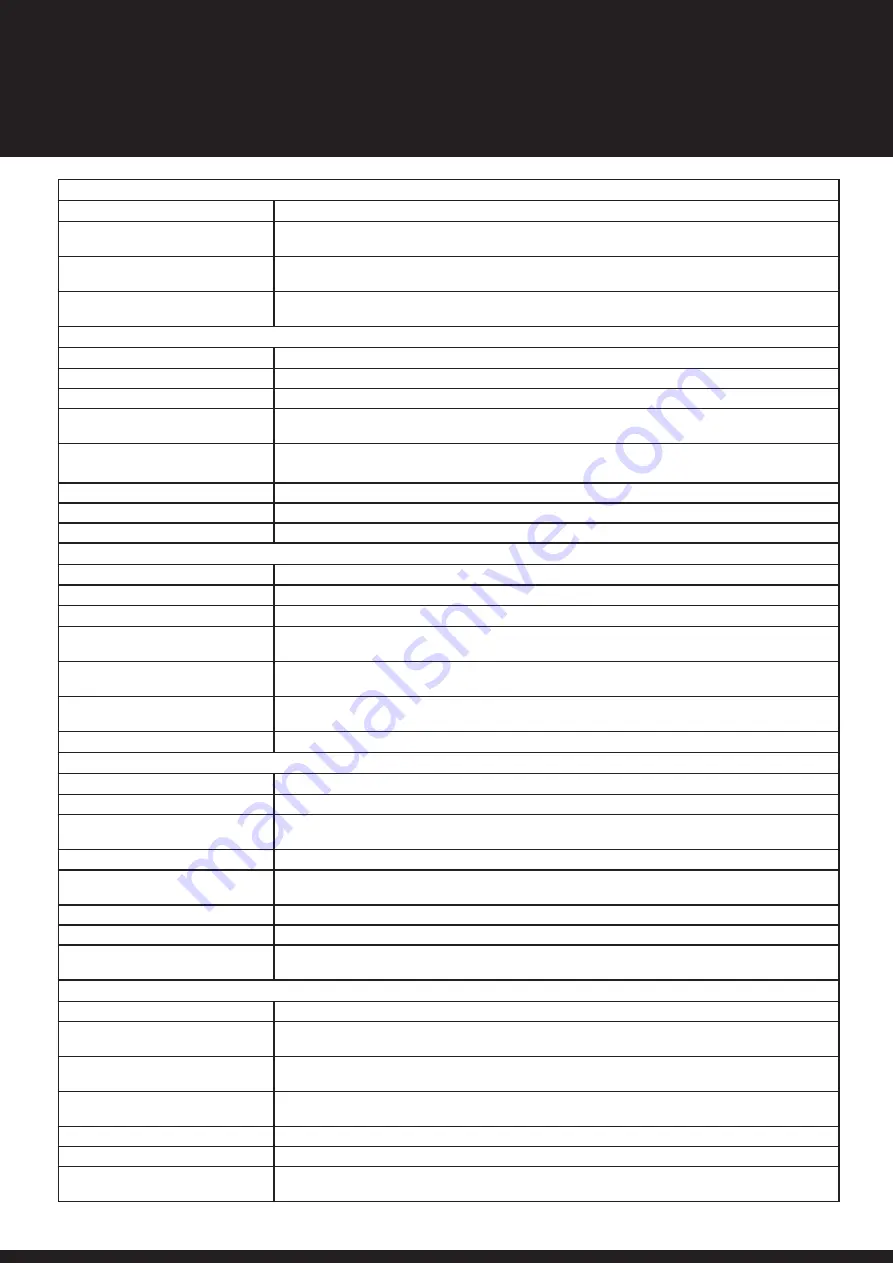
RAZORWELD™205SS MIG/TIG/STICK Welder Manual
|
47
Razor
Weld
TIG WELDING TROUBLE SHOOTING
6: HF present but no welding power
Possible Reason
Suggested Remedy
Incomplete welding circuit
Check earth lead is connected. Check all cable connections. If using a water cooled torch check that
the power cable is not separated.
No gas
Check the gas is connected and cylinder valve open, check hoses, gas valve and torch are not
restricted. Set the gas flow between 10 - 15 l/min flow rate
Tungsten melting into the weld pool
Check that correct type of tungsten is being used. Too much current for the tungsten size so reduce
the amps or change to a larger tungsten
7: Arc wanders during DC welding
Possible Reason
Suggested Remedy
Poor gas flow
Check and set the gas flow between 10 - 15 l/min flow rate
Incorrect arc length
Lower torch so that the tungsten is off of the work piece 2 - 5mm
Tungsten incorrect or in poor con-
dition
Check that correct type of tungsten is being used. Remove 10mm from the weld end of the tungsten
and re sharpen the tungsten
Poorly prepared tungsten
Grind marks should run lengthwise with tungsten, not circular. Use proper grinding method and
wheel.
Contaminated base metal
Remove contaminating materials like paint, grease, oil, and dirt, including mill scale from base metal.
Contaminated filler wire
Remove all grease, oil, or moisture from filler metal.
Incorrect filler wire
Check the filler wire and change if necessary
Arc wanders during AC welding
Possible Reason
Suggested Remedy
Inadequate gas flow
Set the gas flow between 10 - 15 l/min flow rate
Incorrect arc length
Set the torch so that the tungsten is off of the work piece 2 - 5mm
Tungsten is contaminated
Remove 10mm of contaminated tungsten and re grind the tungsten. Use a pointed tungsten with AC
Squarewave and inverter machines. The point will round off after welding
Incorrect tungsten size and or tung-
sten being used
Check and change the size and or the tungsten if required
Excessive rectification in the base
metal
Increase balance control. Increase travel speed. Add filler wire during welding
Contaminated base metal
Remove contaminating materials like paint, grease, oil, and dirt, including mill scale from base metal.
8: Arc difficult to start or will not start DC welding
Possible Reason
Suggested Remedy
Incorrect machine set up
Check machine set up is correct
No gas, incorrect gas flow
Check the gas is connected and cylinder valve open, check hoses, gas valve and torch are not
restricted. Set the gas flow between 10 - 15 l/min flow rate
Tungsten is contaminated
Remove 10mm of contaminated tungsten and re grind the tungsten
Incorrect tungsten size and or tung-
sten being used
Check and change the size and or the tungsten if required
Loose connection
Check all connectors and tighten
Earth clamp not connected to work
Connect the earth clamp directly to the work piece wherever possible
Loss of high frequency
Check torch and cables for cracked insulation or bad connections. Check spark gaps and adjust if
necessary
Arc difficult to start or will not start AC welding
Incorrect machine set up
Check machine set up is correct
No gas, incorrect gas flow
Check the gas is connected and cylinder valve open, check hoses, gas valve and torch are not
restricted. Set the gas flow between 10 - 15 l/min flow rate
Incorrect tungsten size and or tung-
sten being used
Check and change the size and or the tungsten if requir
Tungsten is contaminated
Remove 10mm of contaminated tungsten and re grind the tungsten. Use a pointed tungsten with AC
Squarewave and inverter machines. The point will round off after welding
Loose connection
Check all connectors and tighten
Earth clamp not connected to work
Connect the earth clamp directly to the work piece wherever possible
Loss of high frequency
Check torch and cables for cracked insulation or bad connections. Check spark gaps and adjust if
necessary