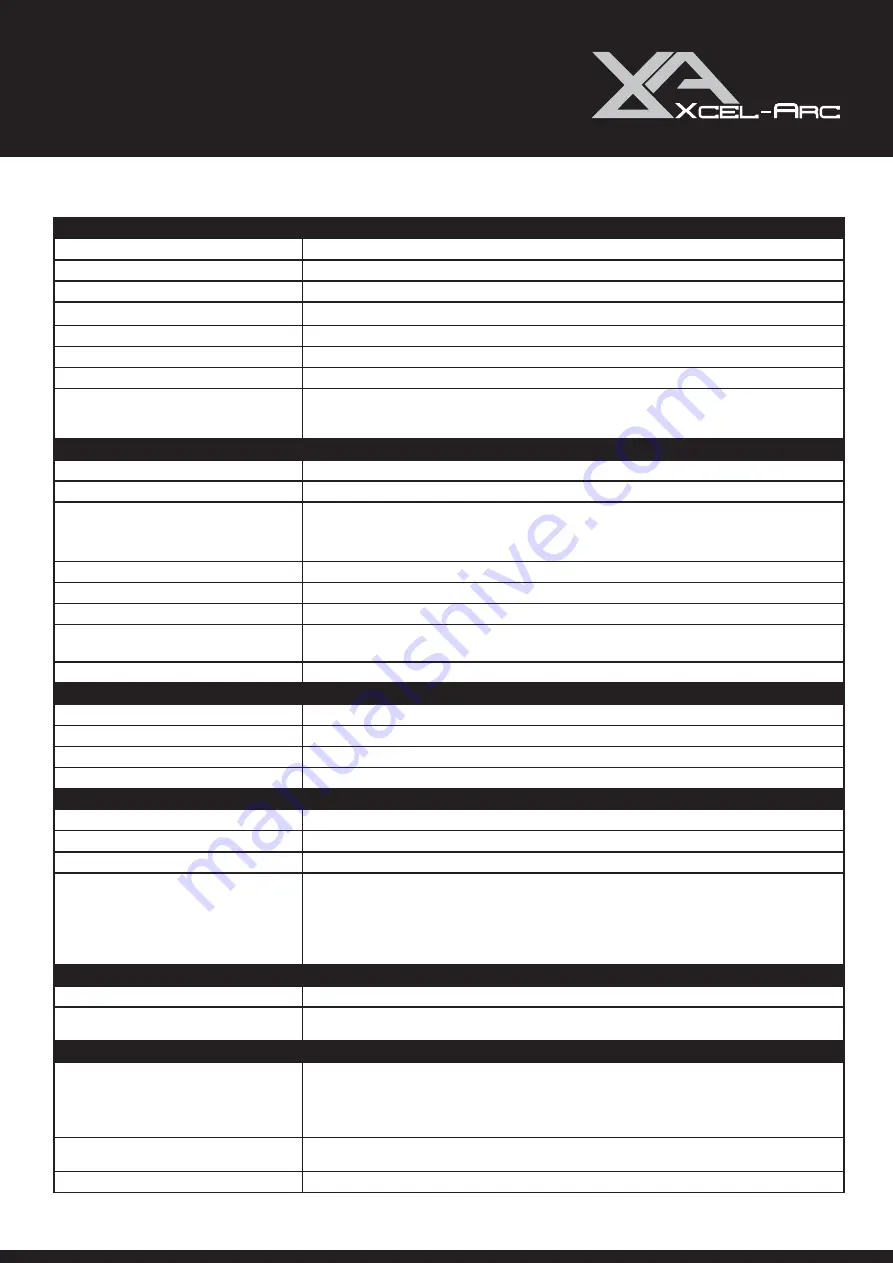
The following chart addresses some of the common problems of MIG welding. In all cases of equipment malfunction, the manufacturer’s
recommendations should be strictly adhered to and followed.
MIG WELDING TROUBLE SHOOTING
1: Excessive Spatter
Possible Reason
Suggested Remedy
Wire feed speed set too high
Select lower wire feed speed
Voltage too high
Select a lower voltage setting
Wrong polarity set
Select the correct polarity for the wire being used - see machine setup guide
Stick out too long
Bring the torch closer to the work
Contaminated base metal
Remove materials like paint, grease, oil, and dirt, including mill scale from base metal
Contaminated MIG wire
Use clean dry rust free wire. Do not lubricate the wire with oil, grease etc
Inadequate gas flow or too much gas flow
Check the gas is connected, check hoses, gas valve and torch are not restricted. Set the gas flow
between 6-12 l/min flow rate. Check hoses and fittings for holes, leaks etc
Protect the welding zone from wind and drafts
2: Porosity - small cavities or holes resulting from gas pockets in weld metal.
Possible Reason
Suggested Remedy
Wrong gas
Check that the correct gas is being used
Inadequate gas flow or too much gas flow
Check the gas is connected, check hoses, gas valve and torch are not restricted. Set the gas flow
between 10 - 15 l/min flow rate. Check hoses and fittings for holes, leaks etc.
Protect the welding zone from wind and drafts
Moisture on the base metal
Remove all moisture from base metal before welding
Contaminated base metal
Remove materials like paint, grease, oil, and dirt, including mill scale from base metal
Contaminated MIG wire
Use clean dry rust free wire. Do not lubricate the wire with oil, grease etc
Gas nozzle clogged with spatter, worn or out
of shape
Clean or replace the gas nozzle
Missing or damaged gas diffuser
Replace the gas diffuser
3: Wire stubbing during welding
Possible Reason
Suggested Remedy
Holding the torch too far away
Bring the torch closer to the work and maintain stick out of 5-10mm
Welding voltage set too low
Increase the voltage
Wire Speed set too high
Decrease the wire feed speed
4: Lack of Fusion − failure of weld metal to fuse completely with base metal or a proceeding weld bead.
Possible Reason
Suggested Remedy
Contaminated base metal
Remove materials like paint, grease, oil, and dirt, including mill scale from base metal
Not enough heat input
Select a higher voltage range and /or adjust the wire speed to suit
Improper welding technique
Keep the arc at the leading edge of the weld pool.
Gun angle to work should be between 5 & 15°
Direct the arc at the weld joint
Adjust work angle or widen groove to access bottom during welding
Momentarily hold arc on side walls if using weaving technique
5: Excessive Penetration − weld metal melting through base metal
Possible Reason
Suggested Remedy
Too much heat
Select a lower voltage range and /or adjust the wire speed to suit
Increase travel speed
6: Lack of Penetration − shallow fusion between weld metal and base metal
Poor in incorrect joint preparation
Material too thick. Joint preparation and design needs to allow access to bottom of groove while
maintaining proper welding wire extension and arc characteristics
Keep the arc at the leading edge of the weld pool and maintain the gun angle at
5 & 15° keeping the stick out between 5-10mm
Not enough heat input
Select a higher voltage range and /or adjust the wire speed to suit
Reduce travel speed
Contaminated base metal
Remove materials like paint, grease, oil, and dirt, including mill scale from base metal.
44
|
RAZORWELD™ 205SS MIG/TIG/STICK Welder Manual