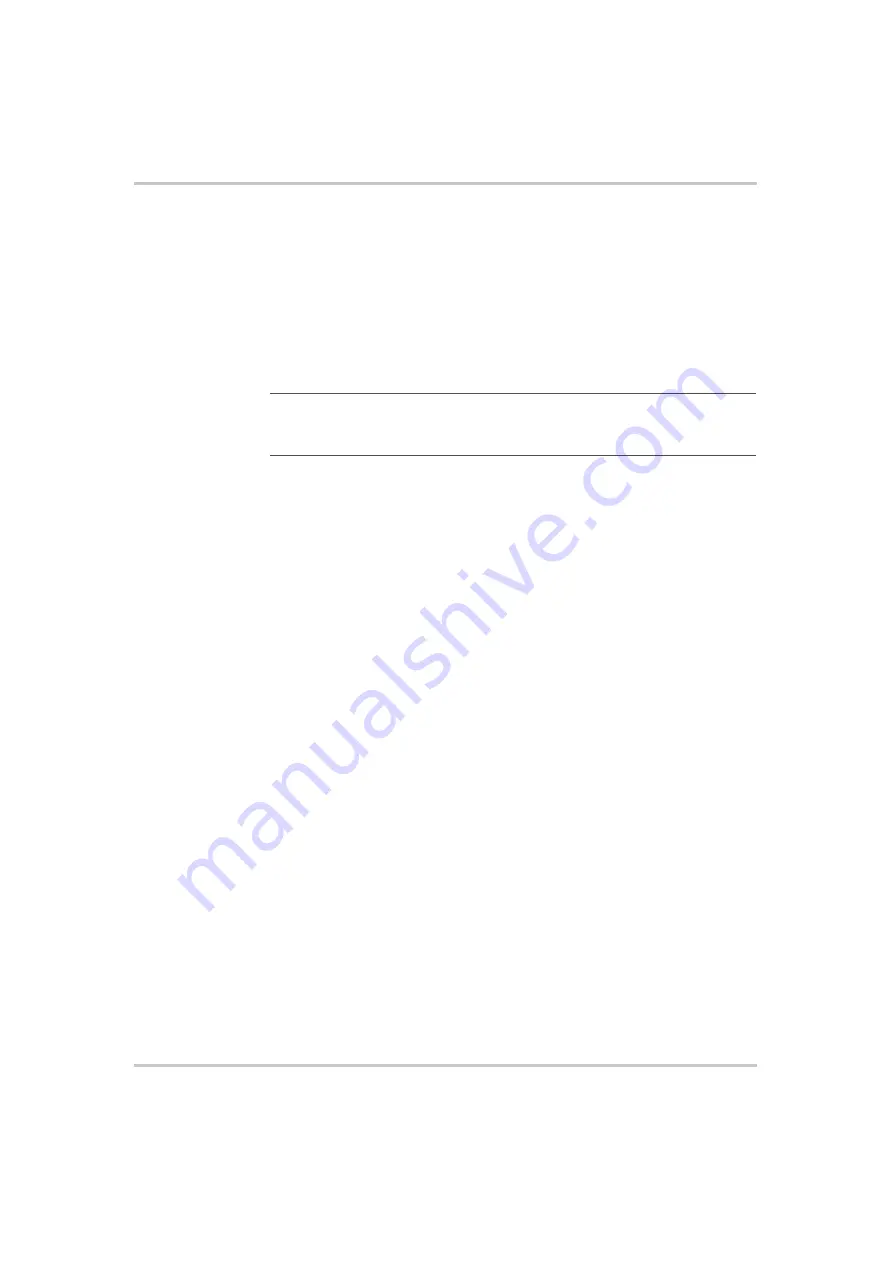
Local Operation
3-24
M370046-01
4. Press the Rotary knob/Enter button to commit the setting once the
desired value has been set.
5. The green FLD LED will turn off and the display will return to the
normal display mode.
The SCPI command (s) for these instructions are:
[:]OUTPut[<channel>]:PROTection:FOLDback[:MODE]
[:]OUTPut[<channel>]:PROTection:FOLDback:LATCh
Resetting Activated Foldback Protection
To reset activated and latched foldback protection, press and hold the
Rotary knob/Enter button for approximately 3 seconds.
The SCPI command (s) for these instructions are:
[:]OUTPut[<channel>]:PROTection:CLEar
Important:
If you set foldback while the output is enabled and the trigger you
select is the same as the current operating mode, the foldback timer will begin
counting immediately after the delay time has been set.
All manuals and user guides at all-guides.com
Summary of Contents for XTR 100-8.5
Page 2: ...All manuals and user guides at all guides com...
Page 6: ...All manuals and user guides at all guides com a l l g u i d e s c o m...
Page 18: ...xvi All manuals and user guides at all guides com...
Page 30: ...1 8 All manuals and user guides at all guides com...
Page 92: ...3 48 All manuals and user guides at all guides com...
Page 198: ...5 72 All manuals and user guides at all guides com...
Page 262: ...A 36 All manuals and user guides at all guides com...
Page 284: ...IX 4 All manuals and user guides at all guides com...
Page 285: ...All manuals and user guides at all guides com...