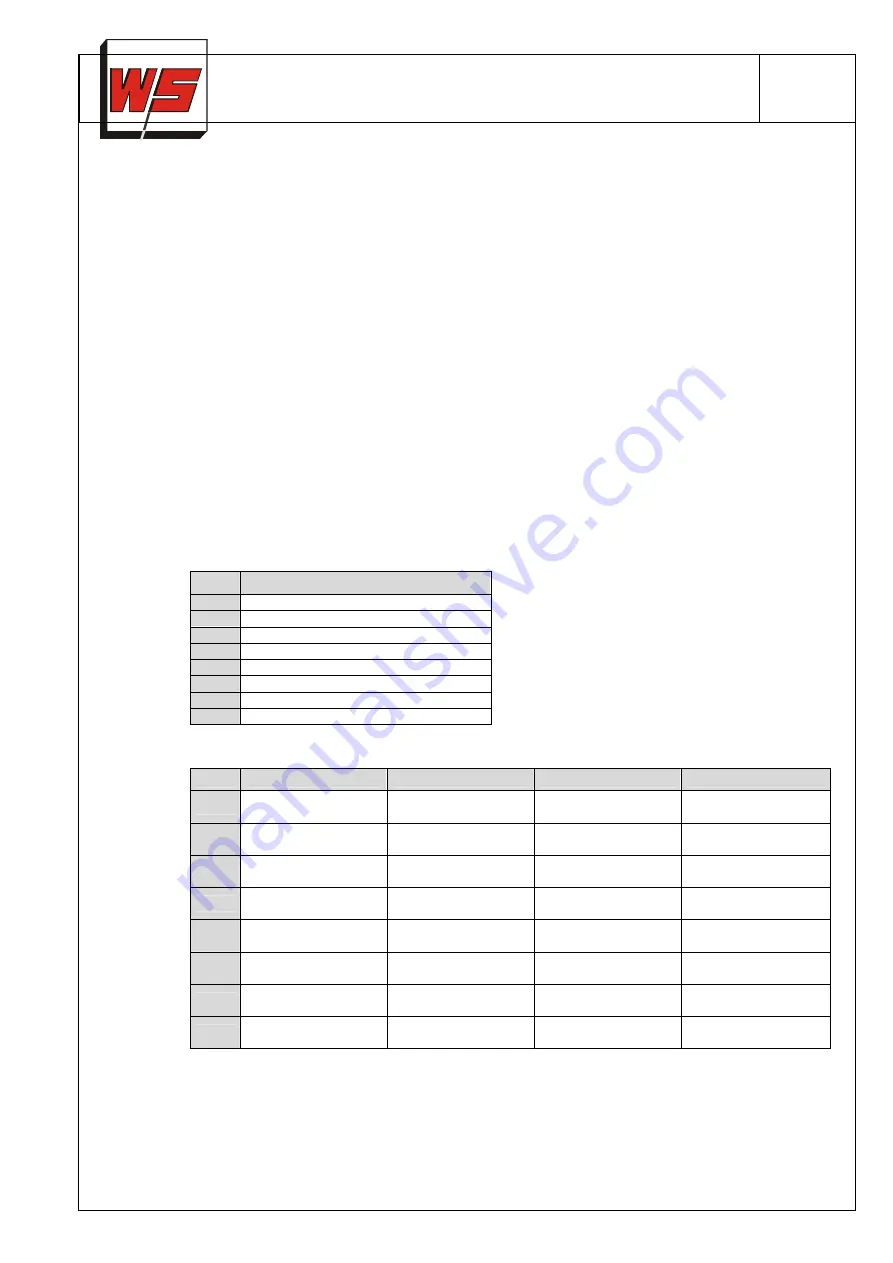
P. 9 / 25
Burner Control CBR
Profibus configuration:
When engineering a Profibus DP system, parameters and addresses must be configured for each device.
A GSD file is provided to simplify and standardize this engineering process. The GSD file format is
standardized, so it can be read and recognized by devices of all manufacturers.
Please contact our sales, service or engineering department for the GSD file applicable for your project.
The steps required to access the file should be available from your automation system manual.
The „Basic I/O“ version (minimum configuration) for data transfer, includes only the output byte (AB0)
and the 2 input bytes (EB0 + EB1).
The „Standard I/O“ version can transfer and analyze the four input bytes (EB0,EB1,EB2,EB3) as well the
output byte (AB0).
More information regarding the „Extended I/O“ version can be obtained upon request.
The address of individual bus devices can be set via the CBR function keys (refer to Profibus Address
Setting). Each CBR is delivered with the invalid address 127 preselected. However, it is still possible to
operate the burner control unit in manual mode, without a valid Profibus address.
Data transfer (Bytes/Bits) from master (host) to the CBR burner control unit:
Please follow all applicable safety regulations. Depicted configurations may differ from the actual scope of delivery, procedures
however, remain principally the same. Please contact our sales or engineering department.
Following tables illustrate the data transfer between master (host) and slave (CBR).
Table 1: Output byte (Master
→
CBR):
Bit
Output byte AB0
0
Remote reset (impuls 0,5s)
1
Heat demand
2
Cooling
3
Purge
4
unused
5
Flame mode
6
unused
7
reserved
Table 2: Input bytes (CBR
→
Master):
Bit
EB0
EB1
EB2
EB3
0
Burner operation
Manual mode
State/Error byte *)
Main gas valve ON
1
Burner fault
Delta-p switch air 1
(min)
Flame gas valve ON
2
Air valve ON
Safety chain OK
Gas valve FLOX 1 ON
3
Air purge ON
Excess temperature,
heating
Gas valve FLOX 2 ON
4
Cooling ON
Excess temperature
burner head/exhaust
Delta-p switch 2 (max)/
exhaust gas thermost.
5
Flame sensed
Cooling valve or air/
exhaust valve 1 ON
Delta-p switch 3
6
FLOX -mode ON
Eductor valve or air/
exhaust valve 2 ON
Gas pressure switch
(optional)
7
Heating stand-by
Common exhaust flap
ON
State/Error byte *)
POC switch for main
gas valve (optional)
*) see table 3