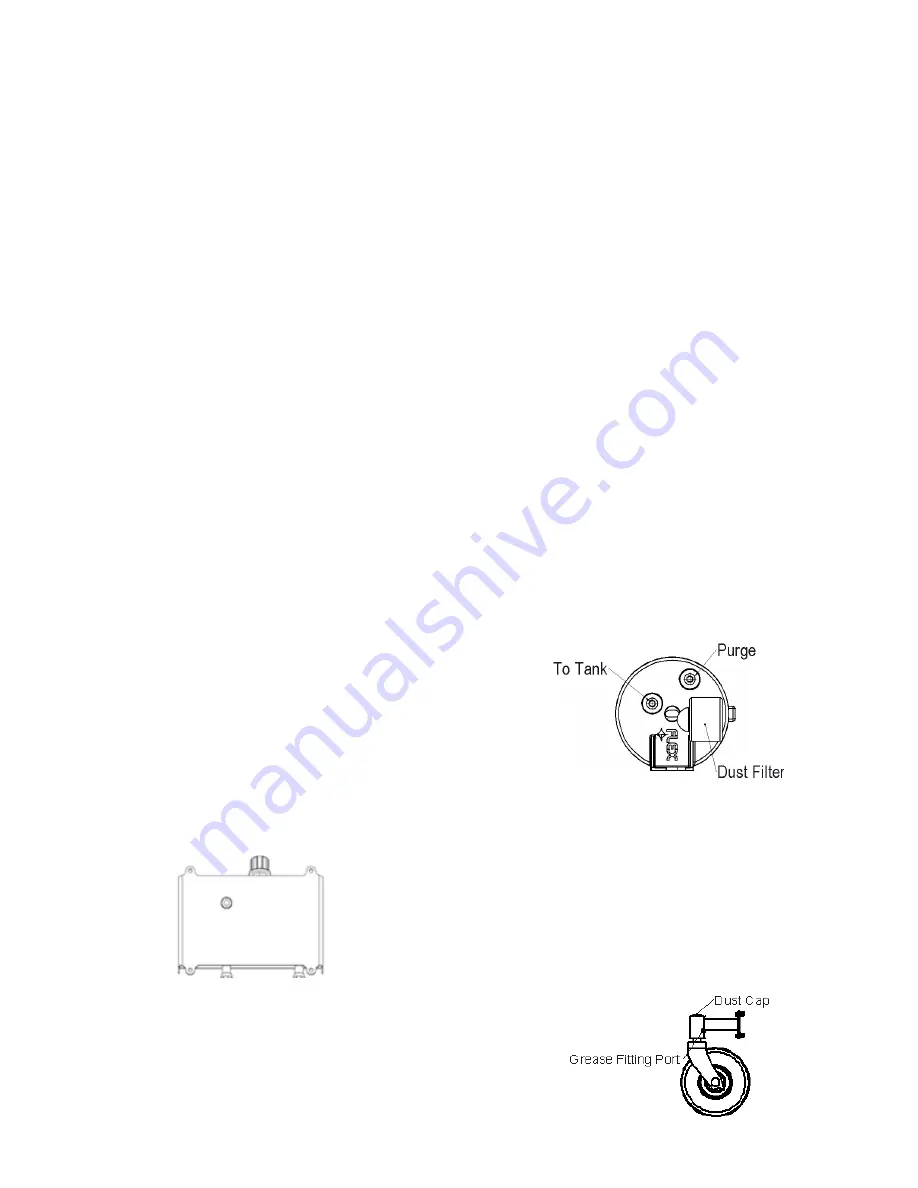
6-4
Hydraulic System
When servicing the hydraulic system it is critical to
keep any dirt or debris from getting into the system.
Clean off all parts before disassembly and assembly.
When any of the hydraulic parts are disconnected
or removed or when the oil is changed, air must
be bled from the system. If air is entrained in the
system, loss of power, excessive heat, and damage
to the hydraulic pumps may occur. WARNING: Fluid
escaping under pressure may have sufficient force
to penetrate skin and cause serious injury. If fluid
is injected into the skin, seek immediate medical
attention. Keep body and hands away from pin holes
or nozzles that eject fluid under high pressure. If a
leak occurs, have the machine immediately serviced
by a trained technician. Never use hands to search
for hydraulic leaks. Use paper, cardboard, or UV dye.
Keep body and hands away from pin holes or fittings
that eject hydraulic fluid under high pressure.
Bleeding Air from the Hydraulic System
If air is entrained in the system, loss of power,
excessive heat, and damage to the hydraulic pumps
may occur. The cause of air in the system can be
from a leaking hose pulling in air or after replacing a
major component.
1. Fill the reservoir.
2.
Lift the machine so that the rear wheels are off
the ground. Be careful to support the machine
so that it will not fall or tip while the system is
bled of air.
3. With the bypass valves open and the engine
running, slowly move the control levers back
and forth five or six times.
4. Now close the bypass valves and with the
engine running, slowly move the control levers
back and forth five or six times.
5. It may be necessary to repeat the above steps
until all the air is purged and the rear wheels
are turning at normal speed.
6. After purging is complete, adjust the oil level in
the reservoir if necessary.
Checking oil
1. Ensure mower is on a level surface.
2. Lift hinged pad to access the sight-glass
3. Oil should be at the center of the sight-glass.
Filling oil
1. Lift hinged pad and remove vent cap.
2.
Use a funnel to fill tank
Changing Oil
1.
Remove filter from tank and allow the oil to
drain from the tank into a catch pan.
2. It is not necessary to drain the oil from the
pumps and motors unless a total purge is
required. Draining the oil from the pumps and
motors introduces air into the system and opens
the system for contamination.
3.
Using a new filter, oil the gasket and hand
tighten. Note this machine uses a non-bypass
suction filter; do not cross reference a standard
automotive pressure filter.
4.
Using a funnel, fill tank until oil reaches the
center of the sight glass.
5. Start the machine and allow the system to warm
up. Check level and top up as necessary.
6. DO NOT USE OIL NOT APPROVED FOR
YOUR MACHINE. Hydraulic and transmission
oils will damage your system, void your
warranty, and are not made for a hydrostatic
system. Use Mobil 1 15W-50.
Fuel Evaporation System
All Wright Standers need to have this mandatory
feature.
•
Do not alter or remove.
•
Do not fill past the “Max Fill Level” line.
•
Over-filling could result in clogging the roll-over
vent and/or contaminating the purge canister.
•
The vapor canister is located under the dash.
•
Inspect and clean dust filter every 500hrs or
annually.
Lubrication
Your machine is made with sealed bearings and
synthetic dry lubricant bushings; therefore only the
front caster pivots need to be greased. Grease yearly
by either, removing the ¼-28 bolt and install a grease
fitting or by removing the dust cap, disassembling
and re-packing the wheel bearings. Use Mobil
Polyrex-EM grease. Use care filling with grease gun
as too much pressure could blow out the grease seal.
When re-installing dust cap, use two drops of thread
locker to prevent the dust cap coming off during
operation.
Sight Glass