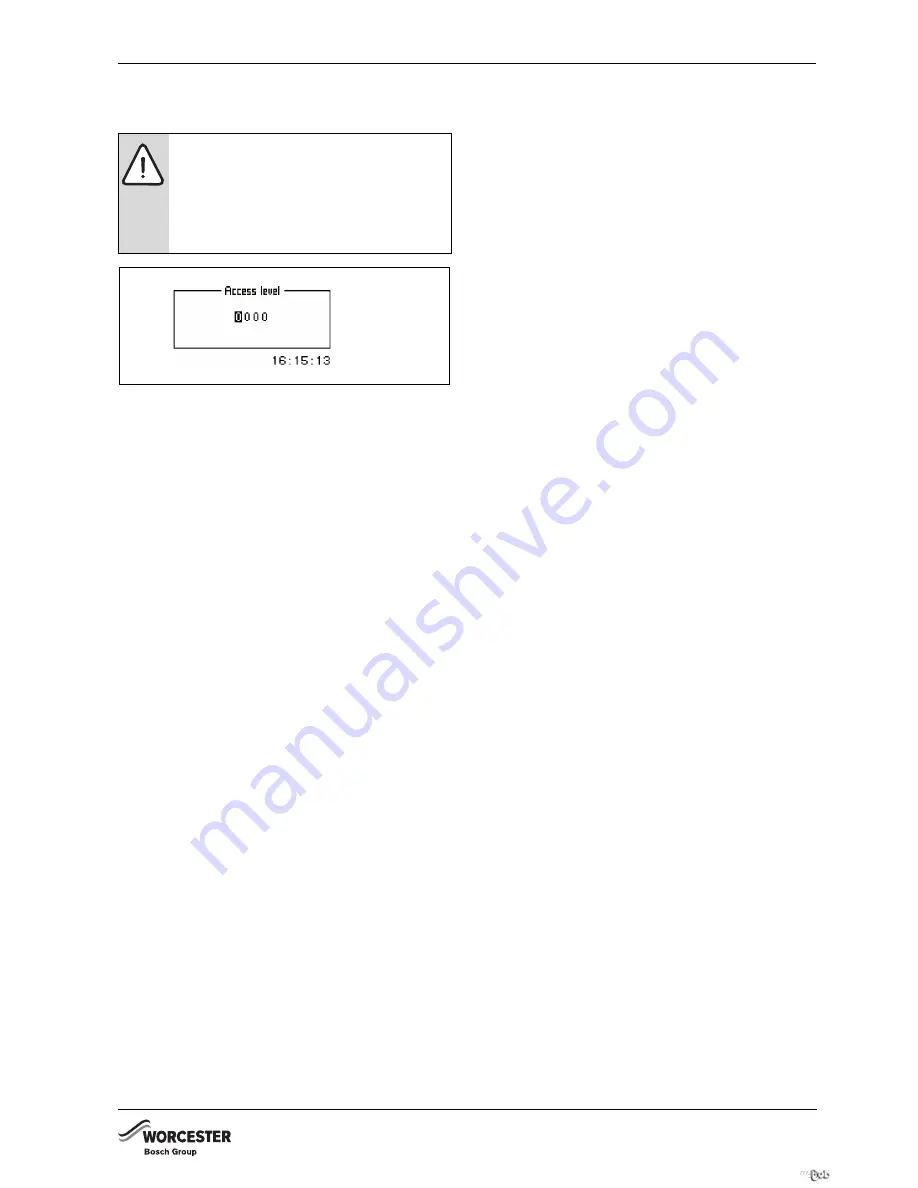
INSTALLATION AND SERVICE MENU (I/S)
6 720 641 467 (2010/01)
29
10 INSTALLATION AND SERVICE MENU (I/S)
Fig. 31
A 4-digit access code is required to open the installation
and service menu (I/S).
1. Hold down the menu dial for 5 seconds to open
Advanced menu
.
2. Select
Access level
.
3. Enter the 4-digit access code with the menu dial and
press to confirm your entry. The access code is the
current date and comprises two digits for the month
and two for the day (e.g. 0920 for the 20th
September). The display shows Access = service.
4. Press menu dial to open
Menu
. The most commonly
used menu points are accessible at the user level; the
menu points of the installation and service menu (I/S)
are only accessible at
Menu
. Hold down the menu dial
for 5 seconds to open
Advanced menu
.
5. In
Advanced menu
select point
Access level
. Enter
access code 0000 to return to the user level.
120 minutes after the last entry, the control unit returns
automatically to the user level.
CAUTION:
Changes in the installation and
service menu (I/S) can have severe
consequences for the system.
B
Only qualified contractors should make
adjustments in the installation and
service menu (I/S).
6 720 641 467-02.1I
For latest prices and delivery to your door visit MyTub Ltd - www.mytub.co.uk - [email protected] 0844 556 1818