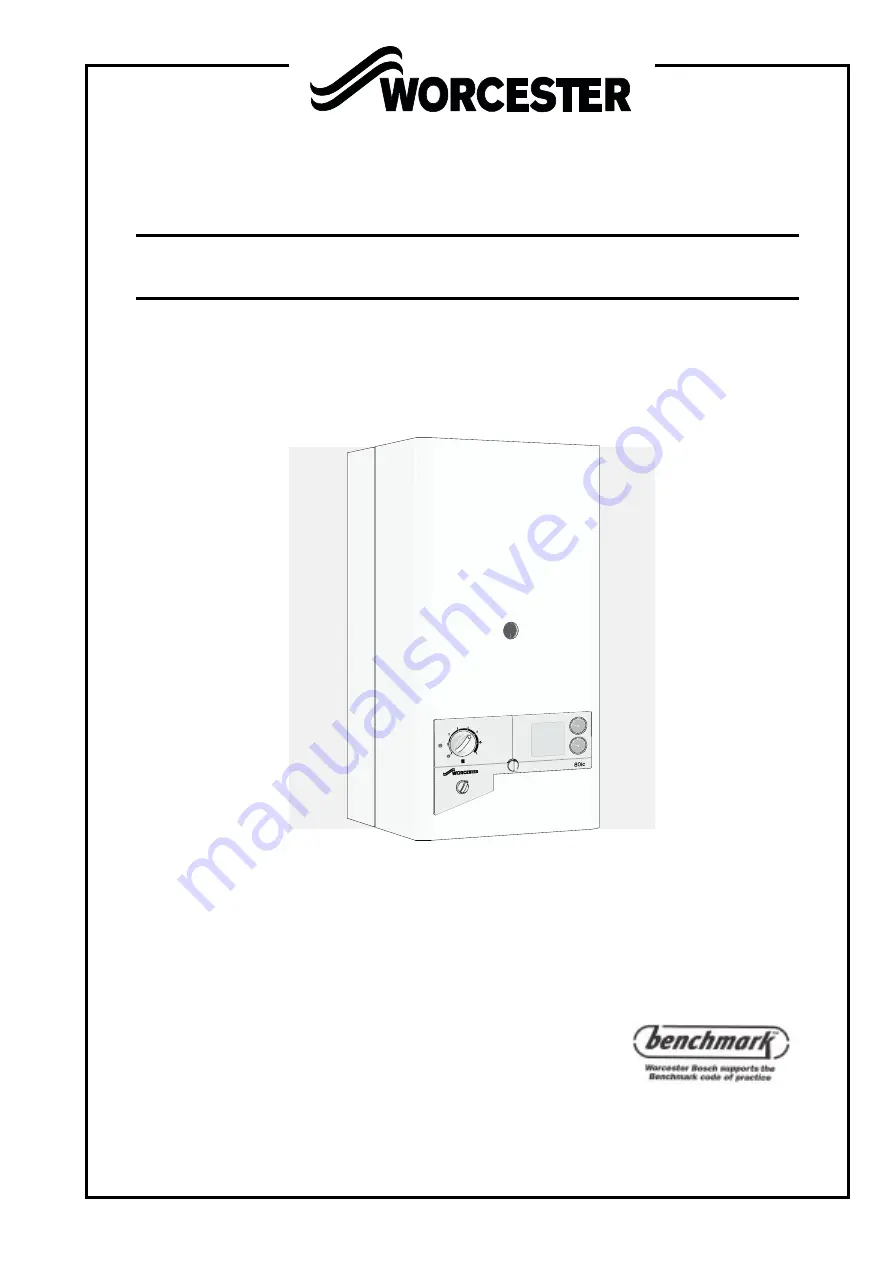
6
720
605
553
PT
2000.1
1
80ic RSF
WALL MOUNTED COMBINATION BOILER FOR CENTRAL HEATING
AND MAINS FED DOMESTIC HOT WATER
INSTALLATION AND
SERVICING INSTRUCTIONS
Cat:
II
2H3+
GC NUMBER
NG: 47 311 43
LPG: 47 311 46
BOILER OUTPUT
To Domestic Hot Water - Modulating control
Minimum 7.0 kW
Maximum 23.0 kW
To Central Heating
Minimum 10.0 kW
Maximum 20.0 kW
IMPORTANT: THESE INSTRUCTIONS APPLY IN GREAT BRITAIN AND IRELAND ONLY
THESE INSTRUCTIONS ARE TO BE LEFT WITH THE USER OR AT THE GAS METER
This appliance must be installed by a competent person in accordance
with the CURRENT Gas Safety (Installation and Use) Regulations
Summary of Contents for 47 311 43
Page 11: ...11 Fig 7 System filling and make up ...
Page 27: ...27 Fig 27 ...
Page 30: ...30 19 Functional Flow Diagrams ...
Page 31: ...31 ...